2007年我國滌綸纖維年產量1900多萬噸,其中近一半份額(約900萬噸)用於純滌綸染色產品。一般純滌綸染色工藝耗水量,若以染色用水10~20噸/噸纖維計,染色後水洗用水(包括還原淨洗、皂洗、熱水洗、冷水洗等)為80~120噸。使用後的染色廢水含有大量助劑和殘留染料,污染程度大,處理成本高,反覆的水洗還消耗了大量的熱能。
本課題將採用自主研發的“分散染料微膠囊無助劑免水洗染色”技術,對傳統的高溫高壓染色工藝和設備實施改造,實現各種純滌綸織物的無助劑清潔染色,使染色後排出廢水的色度降低為原有的1/40,COD僅為200mg/L左右,經簡單處理即可使染色廢水脫色,染色廢水100%得到回用,實現染色廢水“零排放”;“免水洗”技術可免除染色後的水洗工序,節省大量的水、助劑、能源和工時。
該技術將普通的分散染料進行微膠囊化,利用微膠囊的緩釋和隔離作用,實現無助劑、免水洗的工藝要求。在保證染色品質不低於傳統染色工藝的前提下,其染色廢水的COD、BOD和色度等指標均達到或接近國家一級排放標準。染色廢水經過濾後即可循環利用,以實現染色廢水的零排放。該工藝可節約大量用水和熱能。通過試驗室規模的試驗,證明該技術具有良好應用前景。
經過研發和中試生產,使該技術進入了生產試驗階段,取得了重大的突破。該技術包括分散染料微膠囊制備方法、染色方法和免水洗染色方法等、染色萃取機、微膠囊染色廢水回用技術。
本技術不改變原有的前處理工藝,但實現染色廢水的回用,免除了染色後的水洗工藝,從而實現了節水、節能,大大減少了污水和二氧化碳的排放,大大降低了生產成本。
“微膠囊分散染料無助劑免水洗染色技術”是我國擁有原創成套自主知識產權的清潔生產技術,處於國際領先地位。它的研究成功和推廣應用,將大幅度減少我國印染行業的廢水污染,節約水及能源消耗,為社會和企業帶來巨大的環境效益和經濟效益。

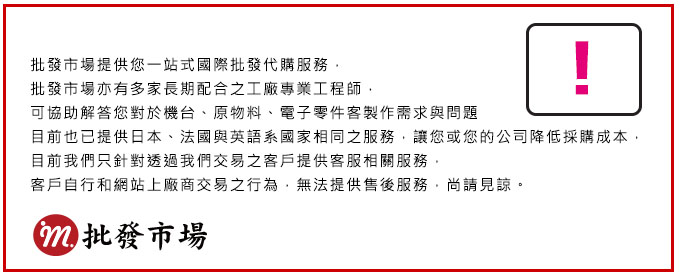
批發市場僅提供代購諮詢服務,商品內容為廠商自行維護,若有發現不實、不合適或不正確內容,再請告知我們,查實即會請廠商修改或立即下架,謝謝。