消石灰在燒結配料車間的作用: 隨著高爐技術日新月異的發展,高爐對燒結技術和生產能力不斷提出更高的要求,使得多年凝滯不前的燒結技術深感力不從心,近幾年來,行業發展迅猛,使得燒結多年來無法解決的問題:燒結強化製粒造球。就現有生石灰配消系統,作如下分析: 1.消化率過低 第一、一般石灰的活性度在300左右,也就是從噴水到石灰升溫到60度左右的時間大致是在3-4分鐘左右才開始釋放蒸汽開始消化,等消化完全沒有熱蒸汽和粉塵釋放需要8-9分鐘,也就是生石灰從消化配水到消化完全整個過程大概需要8-9分鐘,而且消石灰的比表麵積越大,就越能提高混合料小球的生成率和穩定性。 第二、普通的消化器對生石灰的消化時間不到一分鐘,隻是起到瞭打濕的目的,並沒有開始反應就被推出機倉,運輸至一次混合機,未消化完全的生石灰與其它原料(包括混合料、燃料、冷熱反礦)又一次在混合機內加水一起進行混合,沒有消化好的生石灰會進一步消化,從而使造好的小球因生石灰消化發熱膨脹造成小球的破壞,造成乾濕不均,物料混合效果差,大大影響瞭造球效果。從而影響瞭燒結過程中的透氣性和燒結礦的穩定性,燒結礦中白點較多,結塊率低,致使反礦率較高造成燒結礦產質量下降等不利因素。生石灰的主要成分是CaO,與水反應生成Ca(OH)2,發生膨脹並放出熱量,對改善混合料製非常有利。所以生石灰應該進行提前消化。 2.污染嚴重,無專業配套除塵設備 加濕機對生石灰的消化時間不到一分鐘,消化時間過短,造成消化率過低,大部分的生石灰要在配料輸送皮帶上才能完成消化,造成大量的熱蒸汽和粉塵散佈在配料現場,造成現場蒸汽和粉塵污染極為嚴重。而且加濕機沒有完善的除塵設備,造成配料輸送管道經常性的嚴重堵塞,增加現場工作人員的勞動強度,降低作業率。因為散發出的熱蒸汽和粉塵是堿性物質,不但嚴重的污染瞭現場環境,還會對現場其它設備產生瞭嚴重的腐蝕,使設備的整體作業率降低,故障率增高。散發到現場的氧化鈣(CaO)和氫氧化鈣(Ca(OH)2)還會對現場操作人員的身體健康造成嚴重的危害。 3.生石灰的消化不充分會直接影響燒結礦的造球製粒穩定性和生成率,如果石灰消化不充分會引起造球後的球體因石灰消化而產生的熱膨脹而爆裂,從而影響燒結礦的產量和質量。 本公司產品性能介紹 XH-CU系列乾粉消化系統,能夠有效地將生石灰充分消化並將消化過程中產生的熱蒸汽和粉塵完全的進行處理凈化,保證瞭現場無粉塵污染,蒸汽口排放濃度完全符合國傢排放標準。此系統能夠實現PLC自動控製,可根據生產工藝的要求進行調整,減輕瞭現場工人的勞動強度,保護瞭現場工人的身體健康,設備作業率達到≥96%。 三級消化器具有以下特點: 1.配水自動噴淋系統,采用不同角度進行配水; 2.配水均勻,攪拌合理,根據物料特性進行工藝設計; 3.節能、減排(生石灰消化過程中的粉塵和熱蒸汽回收再利用) 4.根據物料特性進行PLC電腦控製配水比例; 5.占地麵積小、裝機功率低 6.進行非標設計,根據現場空間測量,進行改造 標準技術參數: 設備年作業率:96% 產 量:3-65噸/時 噸耗電量:3KW/時 比表麵積:18+/-2 粉塵排放:國標(30mg/m3) 生石灰轉化率:96% 殘留水分:1.5-5% 細 度:200目通篩濾65%(有效鈣含量85以上,活性度300)

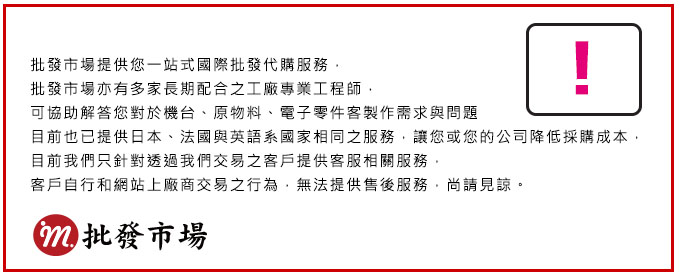
批發市場僅提供代購諮詢服務,商品內容為廠商自行維護,若有發現不實、不合適或不正確內容,再請告知我們,查實即會請廠商修改或立即下架,謝謝。