D爐介紹 VD(Vacuum Degasser)是一種應用廣泛的真空精練設備,具有很好的去氣和脫氧效果,能有效地減少鋼中氫氮含量,通過碳、氧反應去除鋼中的氧,通過堿性頂渣與鋼水的充分反應脫硫,此外還具有均勻成分和溫度的功能。 3、工藝流程 精煉爐——VD爐(座包——接氬氣——蓋罐——抽真空——真空保持——破空——取樣、測溫——軟吹氬——吊包)——連鑄 4、真空泵系統性能參數
真空泵系統性能參數 數值 泵的抽氣能力時 67Pa 260kg/h 500 Pa 1000 kg/h(混合氣體) 8KPa 1600 kg/h(雙流) 35KPa 3200 kg/h(雙流) 工作真空度 67Pa 極限真空度 13Pa 真空系統的漏氣量 ≤20 kg/h 蒸氣壓力 ≥0.8Mpa(表壓) 蒸氣溫度 180—195°C(過飽和乾蒸氣) 蒸氣耗量 ≤12000 kg/h 冷凝器冷卻水進水溫度 ≤35°C 冷凝器冷卻水進水壓力 ≥0.30Mpa 冷卻水耗量 ≤600 m³/h 壓縮空氣壓力 0.4~0.6 Mpa
4 5、生產準備 5.1 爐前工A認真檢查各開關是否處於正確位置。 5.2 主控工檢查各指示燈、機表顯示、計算機系統是否正常,發現問題及時通知相關人員進行處理。 5.3 爐長檢查電力系統是否正常,油水冷卻裝置是否異常。 5.4 爐長檢查水冷系統管道、閥門是否漏水,壓力是否正常。 5.5 爐前工B檢查罐蓋是否牢固,升降有無障礙,密封是否有問題。 5.6 爐前工A檢查氬氣系統是否漏氣,壓力大小是否正常。 5.7 爐前工B檢查液壓系統是否正常,有無漏油,溫度合適等。 5.8 爐長檢查罐蓋車、軌道是否正常。 5.9 爐長檢查測溫、定氫、取樣等工具是否齊全,物料是否備齊。 6、LF爐鋼水要求 6.1成份要求:LF爐將所有的合金元素化學成份調整到符合工藝要求(要考慮到喂矽鈣線的增矽量及Als、微量元素的衰減)。 6.2溫度要求:盡力保證抽氣結束後溫度達到上連鑄要求。 6.3出鋼量控製:根據鋼包狀況嚴格控製出鋼量,要求出鋼後(或事故倒包)後,渣麵距包口凈空不少於800mm。 6.4渣況要求:黏度合適,盡力保證抽氣過程不溢渣。 7、VD工藝操作
抽氣時間 預抽 ≤3.5 min 不預抽 ≤7.0 min
5 7.1抽真空準備 7.1.1 接鋼水要由爐長指揮,指揮天車坐包前必須確認鋼包清潔,無粘渣、鋼後方可靠近工位進行指揮,防止掉渣、鋼傷人。 7.1.2 爐長用對講機指揮天車,爐前工A接好氬氣管,將鋼包吊入VD罐。 7.1.3 爐前工B打開吹氬閥門,調整好氬氣壓力(或流量),檢查吹氬是否滿足要求,出現問題及時處理,底吹氬不透不得進行抽真空操作。 7.1.4 室內操作工確認罐蓋車行車區域、彎管車行車區域內無人時方可將罐蓋車、彎管車開到同一工位。 7.1.5 主控工確認後啟動濁環泵、熱井泵,打開冷卻塔。 7.2抽真空操作(手動操作) 7.2.1 主控工打開主蒸汽閥,如果溫度低於180℃,打開放散閥,溫度正常後,關閉放散閥;若溫度高於230℃,通知發電車間降低蒸汽溫度。 7.2.2爐前工A 將罐蓋車開到抽真空工位,下降罐蓋,爐前工B檢查密封圈上是否有渣,防止密封不嚴,打開罐蓋保護氬氣。 7.2.3主控工打開真空主截止閥,關閉閥前破空閥,打開5b、5a閥,5級真空泵開始工作,當真空度下降到33kPa時,打開4b、4a閥,4級真空泵開始工作;當真空度下降到8kPa時,打開B3閥,關閉B列閥(4b、5b閥),打開進水閥C1下,關閉進水閥C2b、C3b閥,3級真空泵開始工作;當真空度下降到2.5kPa時,打開B2閥,2級真空泵開始工作;當真空度下降到500Pa時,打開B1閥,1級真空泵開始工作。 7.2.4 主控工看守在真空度低於0.5乇(67Pa)的情況下,根據各鋼種的要求,保持足夠的時間。 7.2.5 主控工在真空度低於0.5乇的情況下保持時間到後,依次關閉B1閥,關1級真空泵;關閉B2閥,關2級真空泵;關閉B3閥,關3級真空泵;關閉4a閥,關4級真
6 空泵;關閉5a閥,關5級真空泵;關閉進水閥C1下。 7.2.6 主控工關閉真空主截止閥,打開空氣破空閥,待真空度升至85kPa,進行破空操作,爐前工A抬起罐蓋。 7.2.7 破真後根據要求進行爐前工A測溫、爐長定氫、爐前工B取樣操作。 7.2.8爐前工B將樣送至化驗室。 7.2.9軟吹結束後,爐長確認龍門鉤將鋼包掛好後將鋼包吊出,爐前工A取掉氬氣管。註意事項:爐長觀察真空除氣過程前期要緊湊,以縮短真空除氣時間。註意鋼液的沸騰,防止發生熔渣噴濺,當鋼液沸騰過於激烈時,立即關閉B1閥或在罐蓋處手動打開破空閥進行破真空,防止發生熔渣噴濺。 7.3吹氬操作 7.3.1 爐長確保真空除氣過程應保證全程吹氬。 7.3.2 爐長在VD過程中應根據不同階段調整不同的氬氣量,真空除氣中控製氬氣壓力0.2~0.5MPa,流量100-150NL/min。解除真空前,氬氣流量恢復到20~50NL/min進行弱攪拌。解除真空後軟吹氬氣壓力小於0.2MPa,流量5~20NL/min,以鋼液不裸露為準,軟吹時間滿足鋼種要求。 7.3.3 如果吹氬不能滿足工藝要求,爐長可使用事故吹氬,吹透後改為正常吹氬。 7.4測溫、取樣及定氧、定氫操作 7.4.1爐前工A 測溫、爐前工B取樣,爐長關小氬氣,定氫、定氧操作前關閉氬氣。 7.4.2 操作應穩定,保證所測數據準確。 8、喂絲操作 8.1 爐前工A根據工藝規定的喂絲種類、數量、速度喂入。 8.2 爐長使喂絲導管正對吹氬位置,垂直喂入。 8.3 喂絲結束切斷電源,改軟吹氬,吊包時爐前工B向鋼包投入適量覆蓋劑。
7 9、事故處理 9.1透氣磚透氣性差,應加大吹氬壓力,3分鐘後不見好轉,停止精煉。 9.2因蒸氣和設備原因不能正常執行工藝時,允許真空度≤3.0×133Pa(3乇)且3.0乇以下保持≥15分鐘。異常情況時的真空處理,必須盡力提高並維持最高真空度,並在操作記錄上註明最高真空度,保持時間、蒸汽壓力、溫度及異常情況。。 9.3包蓋塌落,包蓋漏水,立即停止操作,吊出鋼包進行處理。 9.4鋼包穿鋼,立即停止操作,提升爐蓋,迅速吊出事故包進行處理。 9.5因為季節(冬季)或鋼包烘烤器等因素,導致鋼包蓄熱不飽和,允許出鋼溫度高出工藝規定上限。 9.6溫度達不到上連鑄要求的,重新吊回LF爐升溫
所謂精煉,就是將在轉爐或電爐內初煉的鋼液倒入鋼包內進行脫氧、脫硫、脫碳、去氣、去除非金屬夾雜物和調整鋼液成分及溫度以達到進一步冶煉目的的煉鋼工藝,即將在常規煉鋼爐中完成的精煉任務,如去除雜質(包括不需要的元素、氣體和夾雜)、調整和均勻成分和溫度的任務,部分或全部地移到鋼包或其他容器中進行。
鋼包精煉爐常規設備包括:LF、VD、VOD、AOD、RH、SKF等是目前世界上使用最廣泛的爐外精煉設備,是用來對初煉爐(電弧爐、轉爐)所熔鋼水進行精煉,並且能調節鋼水溫度,工藝緩沖。它具有設備結構合理,運行可靠及成本低,精煉鋼種多,質量高,操作方便等諸多優點。鋼包精煉爐具有加熱升溫,合金成分微調,氬氣攪拌、快速測溫取樣,脫硫,去雜質、真空脫氣、喂絲調整成分等多種功能,使整個煉鋼進程合理匹配,提高生產連續性。
我公司在以往的鋼包精煉項目中積累瞭設計製造鋼包精煉爐的豐富經驗和理論基礎。在公司的發展中我們總結瞭很多技術經驗:
一是加大變壓器功率采用側出線變壓器,升溫速度根據冶金工藝需要提高到3~4ºC/min,最大達到5~6ºC/min。
二是首次采用銅鋼復合導電橫臂結構,並結合國內情況在鋼包爐上開發采用。
三是在鋼包爐上,采用水冷爐蓋結構並設置有外排煙系統,來滿足國內對環保的要求。
四是在鋼包爐上采用自動測溫取樣裝置成功的移植瞭瑞典SL公司測溫取樣裝置,並進行瞭國產化。
五是在鋼包爐上采用計算機PLC+CRT系統來對鋼包爐進行程序監控測量和圖麵顯示提高自動化水平。
目前鋼包精煉爐技術上,我公司主要特點在於:
可根據用戶冶金工藝需要設計製造所需的鋼液升溫速度,變壓器可配到200KVA/t左右。升溫速度可達到國外同類產品水平,平均升溫速度3~4ºC/min,最大升溫速度5~6ºC/min。
合理設計供電系統,滿足鋼包精煉爐大電流、低電壓運行工況,加熱系統的設計主要技術參數與國外鋼包爐相似。
三相不平衡系數等於或小於5%
短網阻抗約2.4~2.6mΩ
在結構設計上,特點在於:
采用體積小,結構合理的側出線變壓器,減少穿墻銅管的長度,合理佈置設計短網系統,並采用管式匯流組及水冷補償器,采用三角形佈置。
根據用戶不同要求,對電療橫臂結構不斷改進,采用導電橫臂。
采用邊相八字結構導電橫臂,大大減少電療分佈園直徑,以降低鋼包包襯耐火指數,提高鋼包使用壽命。
采用水冷爐蓋及爐蓋外排煙結構,在鋼包運行中使爐內處於微正壓惰性氣氛下,降低電療的氧化程度,以便使電療消耗降低。水冷爐蓋的壽命達3000以上爐次,與國外水平不差上下。
根據用戶煉鋼工藝要求,提供所需要的功能齊全的鋼包精煉設備。例如:工藝要求除氣,我們可以配套真空脫氣設備。要求實現低(P),低(S)鋼生產,實現Al2O3夾雜物變形可以配套噴粉裝置或頂吹氬裝置。實現成分精確度調整,可以配備合金微調系統和喂絲系統。
為瞭實現成分、溫度均勻、夾雜物上浮,鋼包精煉爐具有吹氬攪拌功能。
為瞭實現溫度調整,協調煉鋼爐與連鑄生產過程,鋼包精煉爐具有加熱功能。…等等
用計算機PLC+CRT或LCD系統對鋼包精煉爐進行監控、測試外,還可以進行車間聯網,以提高自動化管理水平

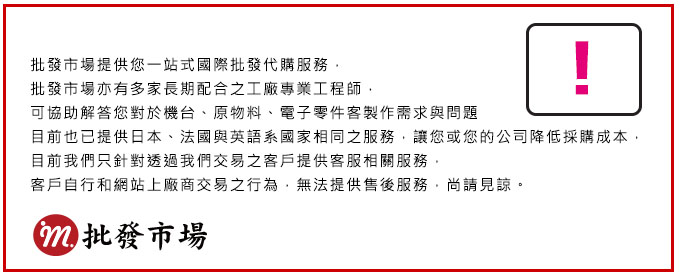
批發市場僅提供代購諮詢服務,商品內容為廠商自行維護,若有發現不實、不合適或不正確內容,再請告知我們,查實即會請廠商修改或立即下架,謝謝。