一、 成型機整體
方案示意圖:
放料架→進料臺→成型機 →校平→剪切→ 定位→接料臺
二、主要技術指標及設備要求
| 項目 | 技術參數及規格 |
成型材料 | 材料 | SPCC、冷軋板、熱軋板等 |
材料厚度 | δ0.6-2mm | |
材料內徑 | φ450~530mm | |
加工能力 | 成型速度 | 10-12m/min |
加工長度 | 按需要 | |
壓力 | 約40T(一套) | |
加工質量 | 長度精度 | L=1000±0.3mm |
成型截麵 | 按圖紙 | |
電源 | 功率 | 約12KW |
2.1占地麵積(約):長15000mm×高1800mm/寬1200mm
2.2生產線方向:麵向操作臺由 左至右
2.3生產操作人員:開車1人 普工1人
2.4設備顏色:設備主體 部分噴黑色波紋油漆,門板等附件噴紅色波紋油漆,可動部分為黃色警示色(客戶可自選)
三:設備概述:
全自動定長成型機生產線工作流程:放料機→校平伺服送料→成型機→校平→剪切。整個過程自動完成。
3.1、放料機
放料部分采用雙懸臂結構,卷料料心大小由手動張緊調節(φ480~φ520),由校平部分帶動卷料,通過剎車帶停轉。
3.2.主成型部分
它主要由導料架、成形部分、傳動部分、等組成。
3.2.1、a.導料架:即為板料的導向裝置,以保證板料平直對中進入成形部分。
b.成形部分:成形部分主要由機架、側板、模具(滾輪)支承部分和滾壓模具組成。
3.2.2機架采用型鋼焊接,結構牢固,經時效處理後再進行加工,其變形小,內應力消除。精加工臺麵(龍門雕銑),平整度±0.2MM,確保設備的強度、剛性、穩定性及精度。
3.2.3、側板均采用45#鋼加工,材質優良,加工後表麵平滑。主側板厚70mm、副側板厚45mm磨六麵,鏜孔加工而成。
3.2.4、模具支承部分的主要部件——軋轆軸為45#鋼材,調質後精車、精磨而成,配合部位尺寸精確,彎曲及撓度性能良好。其軸端工作軸承采用著名的國內外生產廠傢產品,保證工作的穩定性及其工作壽命。
3.2.5、滾壓模具采用國外先進的COPRA軟件進行CAD設計。其材料為GCr15鋼材,熱處理後表麵硬度達到HRC58~60,磨損極小。經過嚴格的工序、工藝,由精密數控機床加工,尺寸精度達到IT6~IT7級,表麵粗糙度達到1.6μm以上,成形後尺寸準確,成形工作表麵美觀。滾壓模具裝置於滾輪軸上,經螺母鎖緊,穩定可靠。成型滾輪14-16組滾輪成型, 孔徑(滾輪軸徑)φ50,滾輪外徑最小φ110。
校直:采用五輪校直機構。
3.2.6、整機經過合理設計後,成形滾輪采用多路軋轆逐步成形,成形後產品尺寸確,表麵美觀。
3.2.7、主動部分采用減速機及聯軸器相互傳動,滾輪之間采用萬向聯軸器傳動,配中心距a=300,減速比i=30蝸輪箱、主電機7.5KW(南洋電機)變頻調速控製。
3.2.8、主軸材料為45#鋼,經過熱處理調質後車加工精磨而成。
3.3.剪切
概述:本系統工作方式分為以下三種:當系統電源閉合的所有條件滿足後,系統才能啟動,啟動後系統應進入手動模式。而通常在生產過程使用自動方式。
3.3.1、手動模式
系統正常運行所需的條件具備以後,系統通電後進入手動模式,而實際生產使用的是自動模式,在手動模式下,當按下正向點動按鈕,刀架向正方向走,當按下反向點動按鈕,刀架向反方向走,按下回零按鈕,刀架回零點。
3.3.2、自動模式
這是為正常生產設置的操作方式,根據設定的切斷長度,刀架自動與材料移動並按照設定長度對材料進行切斷,然後刀架反回原點位置。切刀的速度由設定長度和材料速度自動計算決定。在指定的環境條件具備後,按下“自動模式”按鈕,系統就能進入自動操作方式。
3.4、自動化控製系統
3.4.1、整條生產線集中全自動控製,校平伺服送料機與液壓沖孔機之間聯動,各動作自動完成。
3.4.2、伺服控製系統伺服控製系統中央處理器采用日本安川伺服電機、日本三菱生產的可編程序控製器,驅動裝置采用德國博世力士樂智能全數字交流伺服系統、人機界麵為臺達的彩色高分辯率觸摸屏,系統界麵設有10個定單管理,各定單間配備完整,獨立的計數保持功能,能方便操作者查閱當天的工作記錄情況。接觸器選用西門子,中繼選用歐姆龍,按鈕采用施耐德或ABB,其他元件采用國內外優質產品。
四.設備配置
4.1: 二合一校平放料機 一臺
4.2: 伺服送料機 一臺
4.3:成型機 一套
4.4: 剪切 一臺
4.5: 液壓系統 一套
4.6:自動控系統 一套

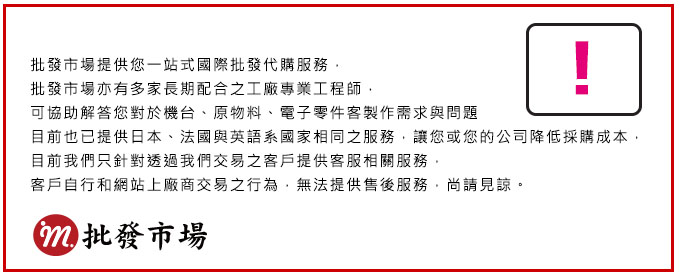
批發市場僅提供代購諮詢服務,商品內容為廠商自行維護,若有發現不實、不合適或不正確內容,再請告知我們,查實即會請廠商修改或立即下架,謝謝。