目前燈桿件的制作有兩種方式:一是板料折彎成多棱形或圓形後,用自動合縫焊機焊直縫,邊合縫邊焊接,這種方法的優點是:效率高、質量好,生產一致性好,制造成本及輔助成本低,設備適應麵廣,使用機動靈活;另一方法是先將工件點固,後采用龍門焊機讓工件固定、焊頭移動的方式對工件進行焊接,這種方法的缺點:生產效率低,輔助工位多,操作工人勞動強度大,合縫質量差。
我公司采用第一種方法的焊接設備已提供十餘傢用戶使用,積累瞭豐富的經驗。經過近十年的使用,一直性能穩定。
ZG-I自動合縫焊接機焊接設備介紹
1、機械合縫主機
ZG型錐桿自動合縫焊接機的主要部分是浮動機械合縫主機,它由龍門架、上壓輪裝置、側向壓輪裝置、浮動梁、下滾輪裝置、液壓系統及焊接系統等組成。四個方向的壓輪組件將成型後的燈桿的縱縫合攏,使縱縫間隙最小,同時控制縱縫的徑向錯邊量;壓輪組件由液壓系統驅動,自動適應燈桿的錐度。焊縫導向輪保證焊縫處於焊槍的焊接位置,防止在焊接過程中焊縫跑偏。
行走機構由交流電機驅動,進口變頻器調速。具有焊接時低速運行、回程時高速運行兩種速度,保證合理的生產節拍。
龍門架由優質型材和鋼板焊接而成,焊接後消除焊接產生的應力,然後精加工而成。龍門架上橫梁上配置有上壓輪裝置,上壓輪主要是鋼輪和液壓缸組成,通過液壓缸給出力量來多工件的直徑變化進行壓緊,讓工件的被焊焊縫始終處於近似合攏狀態;
測壓輪主要是兩組鋼輪和兩個液壓缸在左右兩側對工件進行壓緊,使工件始終處於合攏狀態,測壓輪在焊接過程中始終處於壓緊狀態,隨工件的直徑變化而壓緊;測壓輪整個機構可以根據工件的直徑大小上下調節,使壓輪壓緊工件的位置在直徑的水平中部。上下調節的導向依靠直線導軌,該導軌采用臺灣ABBA的直線導軌。
送料裝備采用機械式送料,將工件置於輸送軋道上,用機械擋塊將工件尾部固定,機械擋塊固定在鏈條上,通過鏈條傳輸將工件推進。還有一種送料裝置,是在工件承料架上增加一套機械固定機構,通過電機推到工件將工件推進。該到機構的導向是在承料架兩側加工有導向軌道,在該軌道上配置機械推進機構,機械推進機構上安裝有工件夾持機構將工件的3點和9點位置固定,電機推動機械推進機構將工件推進。
退料架是工件焊接完成後可以直接放在退料架上,該退料架有一定的坡度,工件焊接完場後到達退料架上,工件在退料架上會自動滾動到料架的一側,該側有機械擋塊。到達一定數量一起吊離料架;也可以根據用戶的選擇增加一套自動下料機構,工件到達退料架後,該機構啟動將工件移動承料架上。
焊接系統采用我公司的NB-500IGBT氣體保護焊機,焊槍采用德國賓采爾直柄水冷焊槍。
控制系統采用PLC作為主控單元,燈桿的驅動電機采用變頻無級調速,恒轉矩輸出,電控系統能根據燈桿的不同位置調節液壓系統的壓力使之適合最佳合縫狀態,具有多種位置、焊接參數檢測功能,使合縫、焊接過程自動完成,無須人工調整。
2、設備特點
ZG型錐桿自動合縫焊接機具有模塊化、機械化、自動化等優點。
生產效率高:該設備是將折彎後的燈桿進行合縫焊接,邊合縫邊焊接,焊接速度可達到1.0m/min,通常20分鐘可完成一根燈桿的焊接,焊後工件成型好,無須打磨焊縫。
產品質量高:采用進口焊接系統輔以先進的焊接工藝進行燈桿的合縫焊接,焊接過程中的的飛濺小,焊縫表麵光潔,焊後無須修磨焊縫表麵,省約瞭輔助工序。
設備性能穩定性高:該設備采用液壓方式進行錐管的合縫,采用同步液壓缸保證瞭合縫的同步精度;采用精密直線導軌支撐各主要運動部件,使得壓輪在合縫過程中運動平穩;采用變頻電機驅動齒輪齒條帶動整機運動,使得焊接速度穩定可靠。
自動化程度高:本設備采用PLC進行中央控制,采用變頻調速器進行焊接速度的調節,采用進口先進器件作為執行機構,保證瞭本設備的自動控制的可靠性,達到瞭國內外同類產品的先進水平。
適用范圍廣:本設備可焊錐形桿的直徑范圍為φ58~φ300mm,可焊燈桿長度為14m,焊接錐管的壁厚為δ2~δ6mm。
3、主要技術指標:
適合工件:各種圓形、菱形規格的燈桿
焊接長度:140000mm(工件不動)
工件最大端直徑:1500mm
工件最小端直徑:300mm
最大快速移動速度:10000mm/min
焊接厚度:2-6mm
最大工作油壓壓力:15Mpa
調壓范圍:0-15Mpa無級調節
壓輪定位方式,根據工作參數,全自動定位方式。
壓力控制方式:根據工作參數,自動調整和手動調整的聯合控制方式。
φ300mm時的變形度:5mm
焊接方式:MAG氣體保護焊
焊接速度:0-2.0m/min
焊絲直徑:Φ1.0~1.2
合縫方式:同步液壓方式
錯邊控制:≤1.0mm

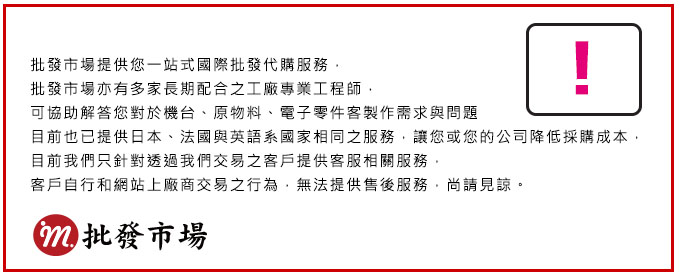
批發市場僅提供代購諮詢服務,商品內容為廠商自行維護,若有發現不實、不合適或不正確內容,再請告知我們,查實即會請廠商修改或立即下架,謝謝。