加工定制:是 | 類型:風冷卻器 | 品牌:志遠熱工 |
型號:ZGRH-Z | 功率:1111100000000(KW) | 溫度范圍:11111111111111 |
外形尺寸:111111111(m) | 重量:11111111(kg) | 結構形式:立式 |
型號種類:至元 | 別名:爐窯節能器 | 適用范圍:鍋爐。窯爐,冶煉爐 |
爐膛最高溫度:200-800 |
熱回收魔力
目前熱定型機餘熱回收的方法是:從排出的熱廢氣中回收熱能再返入熱定型號機內而實現節能。
保護環境一般都需要大量資金的投入,能源(水、蒸汽、油、煤等)又頻繁漲價,開發一種既環保又節能的產品顯得尤為重要。我公司的技術人員在長期進行定型機廢氣處理的實踐中,探索出很多節能改造的項目,經過研究論證開發出一套既環保又節能的新產品:定型機廢氣凈化—熱風回收魔術棒,它具有投資少,節能效果顯著等特點。
隨著社會進步,科技的發展,環境污染逐漸成為一個廣泛問題,環境保護和能源節約成為人們的首要任務。我國是紡織與印染大國,定型機是紡織印染後整理的關鍵設備,熱定型機是利用熱空氣對紡織物(如佈匹)進行乾燥和整理並使之定型的裝置。在定型機加工過程中排放出大量廢氣,廢氣中含有煙塵、油漬、揮發的染料助劑等有害成分。一般熱定型機內所需熱風溫度約為200℃左右,隨著社會的進步,科技的發展,環境污染逐漸成為一個廣泛關註的一個問題。環境保護,離開熱定機的廢氣溫度一般在170℃左右,大量餘熱被帶出定型機外。如果加上燃料燃燒損失以及機體散熱損失等,經估算輸入熱定型機的熱量有90%以上由排氣散入大氣,真正用於處理織物所消耗的熱量隻占瞭輸入定型機熱量的2.9%。散失的熱量不僅浪費能源而且造成定型機車間環境溫度的升高而影響操作工人的身心健康,因此對熱定型機的餘熱回收是勢在必行的。
紡織印染是能源消耗大戶,企業每年在能源消耗方麵都要花費大量的費用購買煤炭、蒸汽用於生產過程中的退漿、煮練、漂洗、蒸堿、軋染、高溫高壓溢流染色、卷染、印花蒸化、烘乾、熱定型、鍋爐連續排污或定期排污、三效或擴容堿回收、水膜除塵等工藝過程。而加工後的產成品並未帶走任何熱能,過程中的能源消耗均以廢熱氣、廢煙氣、熱污水、廢棄熱水、熱輻射的方式流失到環境中,給生產環境、污水處理帶來很大危害。一方麵企業拿出資金購買煤炭或蒸汽,另一方麵企業又要花費資金增加空調送風、污水降溫,造成瞭生產成本加大和不合理的開支。
據測算:一個規模在年加工5000萬米的印染企業消耗煤炭可達3.5萬噸/年以上。折合蒸汽消耗28萬噸左右,由於煤炭的市場需求量在逐年加大,煤炭和蒸汽的市場價格年年攀升且居高不下,直接導致瞭印染行業的百米成本也隨之增加。印染企業的盈利能力直線下降,許多企業處於維持保本的水平上。
如果企業能夠開展熱能回收工作,規模型企業按照年消耗煤炭3.5萬噸或蒸汽消耗28萬噸進行估算,企業每年花費在煤炭或蒸汽上的資金分別為1925萬噸和3080萬噸。而每回收年消耗的1%熱能就可以節約煤炭350噸/年或蒸汽2800噸/年。按照煤炭市場價550元/噸、蒸汽市場價110元計算可知:年節約煤炭成本19.25萬元或蒸汽成本30.8萬元。如果達到20%的回收率,可獲得年效益分別為385萬元或616萬元。如果按照中型企業煤炭消耗在9000噸/年或蒸汽消耗71558噸/年,熱回收率按20%計算,企業回收效益也在99萬元或157萬元。所以,在企業生產過程中進行熱能回收工作是增加企業收益最行之有效的方法,也是減少資源消耗、降低百米成本、提高企業在市場中的竟爭力的捷徑。同時符合當前國傢倡導的清潔生產、資源循環利用和可持續發展的要求。
簡介:
工業燃油、燃氣、燃煤鍋爐設計制造時,為瞭防止鍋爐尾部受熱麵腐蝕和堵灰,標準狀態排煙溫度一般不低於180℃,最高可達250℃,高溫煙氣排放不但造成大量熱能浪費,同時也污染環境。熱管餘熱回收器可將煙氣熱量回收,回收的熱量根據需要加熱水用作鍋爐補水和生活用水,或加熱空氣用作鍋爐助燃風或乾燥物料。節省燃料費用,降低生產成本,減少廢氣排放,節能環保一舉兩得。改造投資3-10個回收,經濟效益顯著。
(一)氣—氣式熱管換熱器
(1)熱管空氣預熱器系列
應用場合:從煙氣中吸收餘熱,加熱助燃空氣,以降低燃料消耗,改善燃燒工況,從而達到節能的目的;也可從煙氣中吸收餘熱,用於加熱其他氣體介質如煤氣等。
設備優點:
*因為屬氣/氣換熱,兩側皆用翅片管,傳熱效率高,為普通空預器的5-8倍;
*因為煙氣在管外換熱,有利於除灰;
*因每支熱管都是獨立的傳熱元件,拆卸方便,且允許自由膨脹;
*通過設計,可調節壁溫,有利於避開露點腐蝕
結構型式:有兩種常用的結構型式,即:熱管垂直放置型,煙氣和空氣反向水平流動,見圖1;熱管傾斜放置型,煙氣和空氣反向垂直上下流動,見圖2。
(二)氣—液式熱管換熱器
應用場合:從煙氣中吸收熱量,用來加熱給水,被加熱後的水可以返回鍋爐(作為省煤器),也可單獨使用(作為熱水器),從而提高能源利用率,達到節能的目的。
設備優點:
*煙氣側為翅片管,水側為光管,傳熱效率高;
*通過合理設計,可提高壁溫,避開露點腐蝕;
*可有效防止因管壁損壞而造成冷熱流體的摻混;
結構型式:根據水側加熱方式的不同,有兩種常用的結構型式:水箱整體加熱式(多采用熱管立式放置)和水套對流加熱式(多采用熱管傾斜放置),如圖3所示
(三)氣—汽式熱管換熱器
應用場合:應用熱管作為傳熱元件,吸收較高溫度的煙氣餘熱用來產生蒸汽,所產生的蒸汽可以並倂入蒸汽管網(需達到管網壓力),也可用於發電(汽量較大且熱源穩定)或其他目的。對鋼廠,石化廠及工業窯爐而言,這是一種最受歡迎的餘熱利用形式。
設備優點:
每支熱管都是一個獨立的傳熱單元,可根據不同的溫度水平而設計;
*根據需要可選擇易拆卸的熱管結構,使檢修和安裝更方便;
*熱管徹底隔離瞭熱源和冷源,不會產生冷熱流體的摻混;
*煙氣側為管外換熱,除灰容易。
結構型式:有兩種結構型式,見圖a和圖b。圖a為汽包內直接沸騰式,即熱管的冷卻段直接伸入汽包內,使汽包內的水產生沸騰;圖b為套管內沸騰式,即熱管的冷卻段被水套管包圍,使套管內的水在流動狀態下沸騰,所產生的蒸汽再匯入汽包。
簡介:
生產陶瓷的一個重要過程是燒成,燒成是在窯爐中進行的。陶瓷生產的窯爐有連續式的(隧道窯)也有間隙式的(倒焰窯),不管是隧道窯還是倒焰窯,其熱效率都比較低。效率低的原因除瞭燃燒損失、散熱損失等原因外,重要的一點是排煙損失。燒成隧道窯廢氣帶走的熱量損失約占總熱量的20%~40%,而倒焰窯廢氣帶走的熱量約占燃料消耗量的30%~50%。因之回收窯尾廢氣的熱量加以利用是提高窯爐效率的關鍵。國內隧道窯排煙溫度一般在200~300℃,也有高達400℃,個別倒焰窯的排煙溫度可高達560℃。一方麵窯爐排煙帶走大量餘熱,另一方麵為瞭乾燥坯件,一些工廠又另外建造窯爐或鍋爐產生熱風和蒸汽以滿足烘乾坯件的要求。采用熱管換熱器來回收煙氣中的餘熱加熱空氣作為烘乾坯件的熱源,可以取得較好的節能效果。
隧道窯餘熱回收主要用以加熱空氣作為烘乾坯件的熱源,也可作為助燃空氣以提高窯爐本身的熱效率,兩者的選擇可依據各工廠具體情況而定。其回收流程下圖所示。
將電瓷廠隧道窯冷卻帶400℃~450℃的廢氣抽出通過熱管換熱器換熱,煙氣溫度降至300℃,再返回窯爐中燒成帶作為氣氛膜風使用。被加熱的新鮮空氣送入烘房,乾燥電瓷坯件。
某廠倒焰窯排煙溫度為564℃,實測該窯爐熱效率僅為23%,由於坯件入窯前需要預熱烘乾,因之需再建一個烘乾窯,以煤作為燃料,燃燒的煙氣作為烘乾熱源。根據計算,如將560℃煙氣降到160℃排空,將新鮮空氣加熱到60~120℃,其熱量足夠烘乾坯件所用。
簡介:
在水泥生產中,回轉窯、冷卻機、懸浮預熱器、烘乾機等都是重要的熱工設備。在保證滿足工藝條件要求的基礎上,提高這些熱工設備的熱效率是水泥生產節能降耗的關鍵。根據近年來工業應用開發的實踐,熱管技術在以下幾方麵已獲得瞭較為成功的應用。
水泥生產回轉窯尾冷卻機低溫段排出的廢氣溫度一般為200~300℃,這部分餘熱的品位較低,它的最好用途是產生低壓蒸汽,作為生活用水,冬天用來取暖和浴室用水;夏天可作為溴化鋰制冷機的熱源制取冷氣供生產車間及生活區降溫,或作為其他工段餘熱鍋爐的換熱器加熱鍋爐給水。
許多小水泥廠的燒成回轉窯窯尾排出的廢氣溫度在450~600℃左右,由於產量較小,廢氣量也比較少,一般均將回收的餘熱產生壓力為0.3~0.8MPa的低壓蒸汽供生產工藝或者說生活使用。從乾法中空回轉窯尾排出的廢氣經過旋風除塵後進入熱管蒸汽發生器,廢氣溫度從600℃左右降至200℃以下,入佈袋收塵系統,經引風機排入煙囪。
其優點是:
◇將高溫廢氣降至200℃以下,可直接進入佈袋收塵器;
◇每噸熟料可回收0.4~0.5噸的低壓蒸汽;
◇結構緊湊壓力降小,一般小於500Pa;
◇不易積灰,管壁溫度可調整在煙氣露點以上,可以達到自清灰目的。
水泥生產中鍛燒熟料的回轉窯窯尾廢氣排出的溫度一般在900~1000℃左右,每噸熟料廢氣量約為(標準狀態)1.658 m3。該廢氣的主要用途一般用作懸浮物預熱器的熱源,預熱入窯的生料粉;另一種用途是與窯尾冷卻機的熱空氣混合進入窯外分解的分解爐;也有將窯尾廢氣用於發電等其他用途。
水泥旋窯工作時燒成段窯體表麵溫度達300-350℃,目前都采用風冷降溫,大量的熱能直接散發到大氣中,這不僅浪費瞭大量的熱能,也造成瞭窯體周圍的高溫污染。窯體表麵散失的熱能是可以回收利用的,我公司研制開發瞭集熱式窯體表麵餘熱回收系統。根據企業的需要,將回收的熱能加熱水或空氣,熱水可供生活和制冷,熱空氣可供烘乾用。既能降低窯體溫度又節省瞭加熱水或空氣所需的燃料費、風扇電費,減少粉塵和二氧化碳排放。節能環保一舉兩得,改造投資一年內可以全部收回,經濟效率十分顯著。
簡介:
冶金工業是耗能大戶,不論是有色冶金或黑色冶金工業都存在大量的節能問題。以鋼鐵企業為例,焦爐、高爐及煉鋼工序均有相當數量的的餘熱未能回收利用。餘熱的溫度最高可達1600℃,熱能的形態有固體、氣體、液體,其中很多為間隙排放,因之給餘熱回收帶來瞭一定的難度。由於熱管的的眾多特點,特別適用於上述場合的餘熱回收利用。高溫熱管及高溫熱管空氣預熱器、高溫熱管蒸汽發生器開發運用成功,給冶金企業的高品位餘能利用帶來瞭新的希望。
軋鋼連續加熱和均熱爐是鋼鐵企業中耗能較多的設備。其熱效率一般隻有20%~30%,約有70%~80%的熱量散失於周圍環境和被排煙帶走。其中煙氣帶走的熱損失約占30%~35%。加熱爐的煙氣量根據爐型大小不同,一般在(標準狀態)7000~300000m3/h的范圍內。煙氣溫度一般為550~990℃,也有超過1000℃以上的。從直接節能來考慮,工程界希望將煙氣的餘熱用來加熱助燃空氣。當助燃空氣被加熱到400℃時,可以得到節能20%~25%的效果。
下圖所示一線材退火爐,爐內溫度為1000℃左右,排煙溫度約800℃,在煙道中放置一高溫熱管空氣預熱器,高溫煙氣通過熱管換熱器熱管的蒸發段,煙氣降至150~170℃排空。20℃的常溫空氣通過換熱器熱管的冷凝段,被加熱到400~500℃,作為助燃空氣進入燃燒噴嘴。應用結果表明,節約燃料可達23%。
軋鋼連續加熱爐排出的煙氣溫度很高,有時可達1000~1100℃,餘熱回收利用的方式首推采用空氣預熱器。回收的餘熱,除瞭熱損失可以百分之百地用於燃燒爐內,不僅節約燃料而且可以改善燃燒效果。但常規的空氣預熱器體積龐大,所以許多工廠采用瞭餘熱鍋爐的辦法來回收餘熱產生蒸汽。這樣雖然可以達到節能的目的,但不能直接節約燃料,也得不到由於燃燒條件改善而對產品產量質量方麵帶來的好處。當前很多工廠采用餘熱鍋爐和空氣預熱器相結合的辦法來達到兼顧的目的。
燒結工序是高爐礦料入爐以前的準備工序。有塊狀燒結和球團狀燒結兩種工藝。塊狀燒結是將不能直接加入爐的煉鐵原料,如精礦粉、高爐爐塵、硫酸渣等配加一定的燃料和溶劑,加熱到1300~1500℃,使粉料燒結成塊狀。球團燒結則是將細磨物料,如精礦粉配加一定的黏結劑,在造球設備上滾成球,然後在燒結設備上高溫燒結。兩種燒結過程都要消耗大量的能源。據統計,燒結工序的能耗約占冶金總能耗的12%。而其排放的餘熱約占總能耗熱能的49%。回收和利用這些餘熱,顯然極為重要。燒結工序內廢氣溫度分佈示意圖如下圖。回收餘熱主要在成品顯熱及冷卻機的排氣顯熱兩個方麵。
燒結餘熱回收的應用流程如下圖所示:
高爐熱風爐是產生熱風的設備,由於風溫可高達1200℃以上,因之熱風爐都是蓄熱式。其工作原理是先使煤氣和助燃空氣在燃燒室燃燒,燃燒生成的高溫煙氣進入蓄熱室內的格子磚加熱,然後停止燃燒,再將鼓風機送來的冷空氣通過蓄熱式格子磚,將格子磚所積蓄的熱量帶走,冷空氣被加熱到所需的溫度進入高爐。熱風爐煙道廢氣的溫度一般限制在300~350℃,最高不得超過400℃。使用熱管換熱器回收的這部分餘熱,用來加熱助燃空氣則可以改善蓄熱爐內的燃燒狀況,從而使爐頂溫度提高。對於以煤氣為燃料的單位,一般多采用分離式熱管換熱器回收排煙餘熱,回收的餘熱同時用來加熱空氣和煤氣,因之稱為“雙預熱”。
簡介:
玻璃生產過程中,從池窯蓄熱室、換熱室(或換熱器)出來的煙氣一般在500℃以下。這些煙氣可以通過熱管餘熱鍋爐來產生蒸汽。蒸汽可用於加熱和霧化重油、管道保溫,以及生活取暖等。對於排煙量較大,溫度較高的煙氣,可通過熱管餘熱鍋爐產生較高壓力的蒸汽(3.5MPa)用於蒸汽透平來發電,或者直接驅動透平空壓機、風機、水泵等機械。對於從工作池和供料道等處排出的煙氣,氣量少而溫度高,可以采用少量的高溫熱管(工作溫度>650℃)來預熱空氣,當離爐煙氣溫度為1000~1200℃,空氣預熱溫度可達400~500℃,節油效果可達20%。在退火爐煙氣的煙道中,以及退火爐緩冷帶以後的部位都可以設制熱管換熱器以回收煙氣的餘熱和玻璃制品的散熱量來預熱空氣,作為助燃空氣、乾燥熱源或車間取暖等的熱源,都可以獲得很好的節能效果。
當前國內玻璃窯爐所使用的燃料大多為重油和渣油,對於這種燃料的煙氣餘熱回收應該特別註意熱管蒸發段管外的積灰堵塞問題。我們公司研制的熱管換熱器,重要的一條設計原則是防止和避免一切可能引起灰堵的因素,以及在結構上確保清洗方便。
簡介:
在紡織工業中使用瞭許多耗能機械,如熱定型機、漿紗機、烘乾機等。這些耗熱機械可以使用電、燃油、燃氣、蒸汽等作為熱源。如何盡可能的利用低溫餘熱減少高品位熱能的消耗是紡織行業節能降耗的重要任務。
熱定型機(或稱拉幅機)是紡織行業中主要耗熱機械之一。熱定型機是利用熱空氣對紡織物(如佈匹)進行乾燥和整理並使之定型的裝置。熱空氣的供給方式有多種途徑,可以直接在定型機內燃燒煤氣或輕柴油,也可以用循環的熱油或蒸汽加熱,或者利用電加熱。一般熱定型機內所需熱風溫度約為200℃左右。離開熱定型機的熱風溫度一般在170℃左右。因之大量的餘熱被排入空氣。如果加上燃料燃燒損失以及機體散熱損失等,經估算輸入熱定型機的熱量有90%以上由排氣散入大氣。真正處理織物所消耗的熱量隻占瞭輸入定型機熱量的2.9%。散失的熱量不僅浪費能源而且造成環境的污染。因之熱定型機的餘熱回收是勢在必行的。用於熱定型機餘熱回收的方式是用排出的熱風加熱新鮮空氣再返入熱定型機,如果熱定型機直接燃燒煤氣或者輕柴油,一部分預熱的空氣也可以作為助燃空氣或者用於加熱熱水。
從餘熱回收效率、壓力損失、防止堵塞、清冼等綜合指熱定型機餘熱回收。系統流程示意圖如下圖所示:
漿紗機是作漿紗乾燥之用。在漿紗機的下部有熱風加熱系統,熱風進入漿紗機後,吸收漿紗的水分,而後排出。由於乾燥過程主要是傳質過程,因而熱氣體的溫度下降不多,主要是濕含量加大。利用排除的濕空氣加熱新鮮空氣回收濕空氣的熱量,返回漿紗機內與熱源熱風混合,達到節能的目的。
漿紗機裝置餘熱回收系統流程示意圖如下圖所示:
簡介:
合成氨工業是一項基礎化學工業,在化學工業中占有很重要的地位。合成氨生產從造氣開始直到氨的合成都伴隨著熱的過程。合理地利用和控制合成氨生產過程中放出的熱量,不僅可以節約生產中的能源消耗,降低生產成本,而且可以提高CO變換率及氨的合成率,前者屬於餘熱利用,而後者屬於化學反應的熱控制。
根據我國工業發展的特殊情況,我國的合成氨工業從生產規模上可分為小合成氨、中合所氨和大合成氨生產。生產的原料路線有煤、油及天然氣。由於原料路線不同,因而生產工藝路線及采用的設備也不盡相同。針對不同工藝路線設備的特點,熱管技術在合成氨工業生產中有以下幾種應用類型。
◇回收低溫餘熱預熱助燃空氣,或生產低壓蒸汽作為生產原料;
◇回收高溫餘熱產生中壓蒸汽作為原料蒸汽的補充,或生產高壓蒸汽作為生產的動力源;
◇控制固定床催化反應器的化學反應溫度,使其向最佳反應溫度曲線無限逼近,從而提高CO變換反應器的CO變換率及合成氨塔內氨的合成率。
以上三種應用類型,在不同的生產規模及不同的原料工藝路線中應用的方式及設計思路均不同,針對不同的實際條件采用不同的結構設計都能取得良好的效果合成氨工業餘熱回收。
上、下行煤氣是指以煤或煤球為原料的生產路線中煤造氣爐所產生的上吹半水煤氣及下吹半水煤氣。由於生產原料不同,上、下行煤氣中所含塵粒及溫度也不相同。
※小合成氨上、下行煤氣餘熱回收
小合成氨生產大都使用煤球為原料造氣。其特點是出煤造氣爐的上、下行煤氣的溫度較低,氣體成分復雜含有大量粉塵及水蒸汽。
我公司生產的熱管換熱器具有如下特點:
① 氣體流動方向為從上到下,減少灰塵附著於管壁的可能性;
② 熱管的蒸發段全部采用直翅片。一方麵可以擴展傳熱表麵,另一方麵可消除熱管背部的渦流區,從而不使灰塵在此停聚。同時也減少瞭流動阻力損耗。
③ 從煤氣出來的上行煤氣先經過旋風除塵器,然後從蒸汽發生器的上部向下流過熱管管束,溫度從進口的360℃左右降到出口的140℃左右進入下一工段的洗氣塔,然後去煤氣櫃。下行煤氣從煤氣爐的底部出來經過旋風除塵器仍然從蒸汽發生器的頂部進入,溫度從300℃以上降至140℃進入洗氣塔,然後去煤氣櫃。
※中合成氨上行、下行煤氣餘熱回收
中合成氨與小合成氨生產除在產量規模不同外,主要的區別在於中型合成氨廠的煤造氣是以塊煤為原料。因此其上行煤氣出煤造氣的溫度遠較小化肥高,大約在600℃左右。與小合成氨不同之處在於煤造氣爐後有一吹風氣燃燒室。上行煤氣經過燃燒室後再進入列管式廢熱鍋爐。上行煤氣與吹風燃燒氣合用一個廢熱鍋爐產生低壓蒸汽(0.4~0.8MPa)或中壓蒸汽(1.9~2.5 MPa)供工藝使用。由於中合成氨煤造氣爐的下行煤氣溫度較低(200℃左右),因而一般不經過廢熱鍋爐而直接去冼氣塔。
中小合成氨不同之處在於所有中型合成氨廠以煤造氣的工段,吹風氣都經過燃燒室燃燒後再進入廢熱鍋爐回收餘熱。原有的列管式廢熱鍋爐都是按瞬時最大吹風氣流量設計的,而吹風氣在一個循環中隻占25%~28%的時間,所以設備的利用率不高。即使上行煤氣也通過廢熱鍋爐,也隻有50%~60%的利用率,何況上行煤氣的流量僅是吹風氣瞬時流量的1/3。所以合理的辦法就是將三臺煤氣爐的吹風氣通過一個燃燒室燃燒,燃燒後的煙氣再進入一個廢熱鍋爐,這就大大提高瞭設備的利用率。雖然利用原有的列管式廢熱鍋爐也可做到這一點,但原有的廢熱鍋爐設計的氣體流速均相當高,鍋爐進口處的流速高達20m/s以上。因此,高速磨損經常是管壁破壞的原因之一。根據中型合成氨生產的具體特點,吹風氣燃燒氣餘熱回收的熱管蒸汽發生器具有如下優勢:
①具有很高的可靠性及比較長的使用壽命;
②體積比較緊湊;
③金屬耗量少;
④保持合理的風速,能有效的防止快速磨損。
一段轉化爐是30萬噸/年大型合成氨廠的關鍵設備。一段轉化爐的任務是在外部供熱的情況下使烴類與水蒸汽的混合物在爐管內轉化為CH4、H2、CO、CO2等氣體混合物。其中CH4、H2是合成氨的原料。一段轉化爐有多種結構型式,目前國內主要有頂部燒嘴和側壁燒嘴二種形式。燒嘴噴出的燃料在空氣助燃下加熱爐內的轉化爐管。熱量大部分為轉化爐管吸收。轉化爐管所在區域稱為輻射段。為瞭充分合理地利用熱量必須使煙道氣通過對流段,在對流段內佈置有各種吸收煙道氣餘熱的管道。回收這部分熱量最合理的用途的是加熱助燃空氣。由於一段爐使用的燃料一般為輕柴油或天然氣,節約這部分燃料也就更有價值。
下圖為一段爐熱管空氣預熱器的餘熱回收系統佈置圖。該系統將熱管換熱器入口的空氣先經過爐墻各段的側面預熱後進入熱管換熱器,其優點是一方麵可起到隔熱作用,降低爐膛周圍操作環境的溫度,另一方麵可以提高熱管換熱器入口空氣的溫度,對提高煙氣出口處熱管的管壁溫度有利,在寒冷地區這一點特別重要。
在中、小型合成氨廠的變換工段,來自熱水飽和塔的半水煤氣要與來自變換爐變換氣進行熱交換。通過換熱,水煤氣的溫度升高,而變換氣的溫度降低。半水煤氣和變換氣的組分都是有毒、易爆、易燃物質(CO、H2)。所有的變換工段的變換熱交換器(第一熱交換器、第二熱交換器)都是采用列管式的,存在易腐蝕、匯露、串氣等問題。特別是第一熱交換器,由於溫度較低,極易腐蝕,維修工作量大。腐蝕還會引起列管管口堵塞,增加系統阻力,致使變換系統壓差增大,影響生產的安全正常運行。
在變換系統中應用熱管換熱器具有如下優點:
◇可以調整熱管管壁溫度,控制低溫腐蝕的產生;
◇個別熱管損壞不會發生二種氣體的串混;
◇設備緊湊,壓力降小,對變換生產有利;
◇使用壽命長,投資少。
變換工段的半水煤氣和變換氣都具有一定的壓力,因此熱管換熱器的殼體都是按壓力容器設計標準設計的。

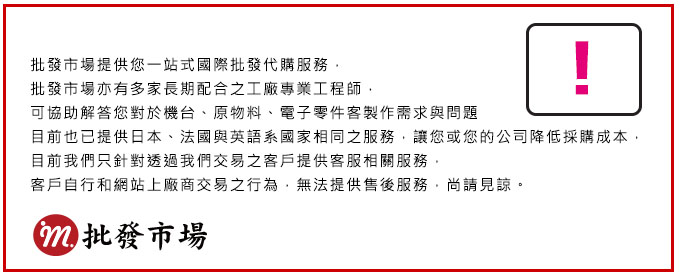
批發市場僅提供代購諮詢服務,商品內容為廠商自行維護,若有發現不實、不合適或不正確內容,再請告知我們,查實即會請廠商修改或立即下架,謝謝。