前 言
正確的使用設備,有助於人機安全,減少維修和停機時間,增強機器的可靠性,延長機器的使用壽命,提高經濟效益。
操作人員是設備的直接使用者,如果不能保證科學合理準確地操作設備,操作事故過多,勢必造成維修方的被動,影響生產。如果操作人員對設備維護保養技能差或不能及時的發現設備隱患,就會導致突發性的設備故障增多,打亂設備維修計劃,最終導致生產的被動。要求操作人員掌握設備操作技能的同時,還要掌握設備的保養及維護,學習設備管理知識,做到正確使用、保養、檢查(發現隱患)、排除(簡單故障)。要求每位員工熟悉工藝要求,瞭解設備結構、性能及工作原理。要懂得設備有關知識,達到“操檢合一”的目的,使設備安全完好、節能、高效地運行。
第一章 擠出成型機概述
塑料擠出成型機簡稱擠出機,它是利用螺桿加壓的方式連續地將塑化好的物料從擠出機料筒經模具口擠出,使之在熔融狀態下,經冷卻定型處理後,由牽引裝置或成型裝置將它連續地從模具口擠出的產品牽引至切割機上進行定長切割。
1、擠出機生產線的主要組成部分及作用:
擠出機生產線主要由主機和輔機兩大部分組成。
A、 主機主要由:轉動系統、溫控系統、喂料系統、真空排氣系統組成。各部分的作用如下:
轉動系統:采用直流或變頻調速,對螺桿的轉速從0-31r/min或0-43r/min進行無級調速使螺桿連續的將熔融的物料經模具口擠出。
溫控系統:利用自動溫度調節機配以相應的加熱圈、熱電偶和恒溫裝置(風冷、油冷),間接對原料按要求進行控溫,使其達到理想的熔融塑化狀態。
喂料系統:由無級調速裝置或原料自身的重量加上料鬥封板將物料不斷均勻地供給擠出機的螺桿,以實現定量喂料而連續經模具口擠出。
真空排氣系統:由真空泵配備顆粒分離器抽取料筒內物料熔融時產生的水蒸氣、揮發物等,以達到排除水份、揮發物等的作用。
B、輔機主要由:定型箱(臺)或成型機、牽引機、切割機、印字(噴碼)機、翻料架、上料機、擴口機等組成,各部分的作用如下:
定型箱(臺):由定型套(模)配以噴淋式或侵泡式冷卻水,利用真空泵使定型箱(模)內產生負壓,使熔融狀態的制品定型凝固成理想的合格品。
成型機:由一定規格、數量的模塊組成,將模具擠出的制品定型並冷卻好後連續的牽引至切割機上進行定長切割(一般是波紋管材專用機組)。
牽引機:利用履帶式或滾筒式牽引機將主機從模具口擠出的制品平穩連續地牽引至切割機及翻料架。牽引機速度的變化將直接影響生產制品的橫切面壁厚及其形狀。
切割機:采用氣動機械裝置、計長裝置利用環形或軋刀式鋸片按要求長度將制品進行自動或手動切割。
印字(噴碼)機:將成型制品的名稱、型號、規格等連續的打印或噴印在生產的制品上。
翻料架:利用氣動裝置使制品脫離計長工位,以達到從新計長之目的。
擴口機:將生產出的合格制品按照客戶的要求進行自動或手動擴口。
2、模具的使用操作及維護保養:正確的工藝條件、合理的配方、適用的工藝參數、熟練的操作人員、正確的操作使用方法是看不見的維護保養設備及模具的關鍵。
A、拆、裝模具的操作方法:
拆、裝螺釘、螺帽:順時針方向為緊,反時針為松(特制模具的螺釘松緊方向有可能會改變)。
拆、裝螺釘、螺帽必須按照逐個對稱,對角方向順序先全部旋松後,再任一逐個拆個。
裝螺釘、螺帽首先應在螺釘螺帽的絲口上塗上高溫油脂[如:二流化鉬油(粉)等]再全部旋到位,逐個對稱,對角順序,視螺釘的大小可用適當的加力桿將扳手套上鎖緊。
拆模:根據生產計劃安排,負責人指揮。拆模前先根據實際情況加入或不加少許停機料,盡量把料筒內生產的物料擠出模具口為止,按生產或使用判斷,需半拆模還是解體拆模。
解體拆模:把全套模具的外模體、分流支架、芯棒等各零部件拆散後,取出殘留的物料,清理幹凈各零部件上的粘料、雜料,檢查模具完好無損後塗好防銹油,拼攏裝好整套模具,放在指定模具架上。
半拆模:根據生產安排及模具結構,判定隻需換芯棒口模的模具,實行半拆模,即把口模和壓板拆下,松脫芯棒拉桿螺帽或芯棒連接牙。取下芯棒,清理物料到可更換芯棒的位置(此時物料可能會因受熱而膨脹)。把預備好更換的芯棒、口模裝上。然後把拆下的口模清理幹凈,如有損壞的需修復後,塗好防銹油,放在指定的模具架上。
無論半拆模或解體拆模,必須對所有有必要上油的流道工作面上塗油維護,對於難拆卸的螺釘、螺帽應事先上好油或蠟後,再進行拆卸,這樣即可省力,又可減小對螺絲及工具的損壞。
裝模:根據生產計劃安排需換裝模,首先找到模具,記住規格型號,查找對應的芯棒、口模,配齊該用的螺釘、螺帽、加熱圈、定徑套、密封板、印字設備及工具等。對不上型號的找負責人查對,檢查過渡套的尺寸是否和模具與合流芯連接處相吻合。檢查芯棒內若帶加熱裝置的是否完好,並進行模具油污、雜物等清理。若放久生銹或損傷的應進行修復或拋光等處理好後,再逐件將機臺與模具連接法蘭片、模體、調模螺釘、口模壓板、鎖模螺釘後,調整好口模與芯棒之間的間隙,如是型材模具則用水平尺裝平,按順序把各連接螺釘、螺帽全部旋到位後對角鎖緊。依模體外型尺寸上好加熱圈(溫度計熱電偶座孔最佳的位置在上面),接好加熱線和熱電偶反饋線,並牢記熱電偶一定要插到位,並拆換好定徑套或真空箱密封板、或型材定型模上真空、冷卻水連接管並與模具裝水平。調整好牽引壓板和切割夾具以及定長裝置輔助設備的配件等,全部核對無誤後才算裝模完好(更換切割機鋸片時,必須關閉電源、氣源下進行,否則可能會引起不必要的麻煩)。
B、總之在裝模和拆模過程中,螺絲或扳手一定要套好,否則會損壞螺絲或扳手,並保護好塑料流道表面不受任何損傷。
第二章 擠出機操作規程
1、 目的:
保證擠出機操作在正常的規定方法下進行,確保產品質量以及設備的正常運行。
2、適應范圍:
擠出車間生產的各種塑料機械及制品。
3、操作規程內容:
A、檢查各加熱圈、熱電偶及加熱器(圈)後,分三段進行加溫(第一段80度,第二段120度,第三段生產需求溫度)在加熱的同時觀察加熱器(圈)及輔機試運轉是否正常。
C、 機筒和模具一定要充分加熱。大產品模具需加熱2-3,小產品模具需加熱2個小時左右。在保溫同時並做好開機準備。
D、 開機前徹底檢查料鬥內有無異物,若有應及時清除。
D、當溫度達到設定溫度並保溫後,檢查各個連接螺釘是否因材質的不同受熱膨脹系數的不一致而松動而再次鎖緊後進行開機。在料鬥內加入需要生產的物料。
E、將所有調速歸到‘0’位啟動同步主機並調主機調速,使其在低速下運轉(此時的主機螺桿轉速應不超過5r/min)根據實際情況是否需要緩慢加入少許停機料,防止速度緩慢運轉時物料在未出模具前因時間過長而炭化變色。然後啟動喂料輔機或拉開料鬥閘門進行同步供料並保證速度匹配,調速時要緩慢平滑調整,否則會因轉動系統的瞬間扭力而對螺桿與料筒等連動部件的磨損。設備在運轉時扭矩電流不能過高或過低,應根據不同型號的擠出機以及物料或正規的作業指導書,控制不同的扭矩電流,絕不允許超負荷運行。
F、從主機料筒抽真空孔處觀察物料在機筒內的塑化狀態,當物料呈半塑化時並配合主機扭矩電流,開啟主機抽真空系統,切勿使用金屬工具捅料筒上的真空眼處的物料,以防損壞螺桿料筒,真空度應在0。03-0。05Mpa左右為佳,並觀察所擠出的物料的顏色及塑化狀態,當完全塑化時,就可以將產品經過定型冷卻系統(成型機)送上牽引機進行產品生產。此時切割機的電源最好處於關閉狀態,也不要用加力桿打未成形的產品,最好用手鋸切斷理想的長度,否則會因產品的未成形而對切割片及人員的損傷。當產品完全成形後,打開切割機電源進行自動定長切割。
G、正常生產時,機筒和模具的溫度一定要按工藝要求設定,並隨時觀察是否有變化而進行調整。
H、認真觀察生產線的運行狀態,發現異常及時緊停,查明原因後自行處理或向負責人報告。排除故障後方可開機,絕不允許異常運行。
I、根據所生產產品的規格、型號、形狀等隨時檢查產品外觀、內壁、長度及切割端面等變化調整牽引速度、定型箱(臺)同心度以及調模螺釘,確定產品能達到標準要求。
J、產品在真空冷卻套(箱)要完全定型冷卻,水套(箱)內真空度要適合,以達到準確定徑。如果產品從冷卻套(箱)內出來時還未冷卻好,此時需水淋、浸泡冷卻或開啟輔助冷卻水箱。
K、 必須保證循環水的潔凈。定型槽內不允許放雜物,防止污染水質。經常保持生產線以及周圍環境衛生清潔。
L、 做好交接班工作,上一班要把設備運行情況以及註意事項向下一班交代清楚。
M、做好生產記錄設備運行記錄,接班後建議每隔2個小時記錄一次,認真填寫在《設備運行過程記錄表》上。
第三章 擠出機保養維護守則
A、設備要經常保持清潔和良好的潤滑狀態,平時做好擦試和潤滑工作,同時保護好周圍環境的清潔。
B、經常檢查各齒輪箱的潤滑油液面高度、冷卻水是否暢通以及各轉動部分的潤滑情況,發現異常情況時,及時自行處理或報告相關負責人員處理(減速箱分配箱應加齒輪油,冷卻機箱應加導熱油)。
C、經常檢查各種管道過濾網及接頭的密封、漏水情況,做好冷卻管的防護工作。
D、加料鬥內的原料必須純潔無雜質,決不允許有金屬混入,確保機筒螺桿不受損傷。在加料時,檢查鬥內是否有磁力架,若沒有應必須立即放入磁力架,經常檢查和清理附著在磁力架上的金屬物。
E、機器一般不允許空車運轉,以避免螺桿與機筒磨檫劃傷或螺桿之間相互咬死。,
F、每次生產後立即清理模具和料筒內殘餘的原料和易分解的停料機,若機器有段時間不生產時,要在螺桿機箱和模具流道部分表面塗防銹油,並在水泵、真空泵內註入防銹劑,
G、如遇電流供應中斷,必須將各電位器歸零並把驅動和加熱停止,電壓正常後必須重新加熱到設定值經保溫後(有的產品必須拆除模具後)方可開機,這樣不致於開冷機損壞設備。
H、輔機的水泵 真空泵應定期保養,及時清理水箱(槽)內堵塞的噴嘴以及更換定型箱蓋上損壞的密封條。絲桿軸承需定期加油脂潤滑,以防生銹。
J、定期放掉氣源三連件的積水。
K、及時做機器各緊固件,如加熱圈的緊固螺絲、接線端子、牽引機夾塊、切割機夾具及有機器外部護罩元件等的鎖緊檢查工作。
第四章 擠出技術問答
1、產品擠出生產有哪些工藝流程?
答:原(混合)料→加料→擠出→定型冷卻→移印(噴印)商標等信息→牽引→切割→檢驗→包裝→入庫堆放。
2、生產UPVC產品,請解釋“UPVC”之含義。
答:VC-聚乙烯,P—聚合,U-硬質、無增塑,PVC-聚氯乙稀,UPVC-硬質聚氯乙稀。
2、過濾板(多孔板)起什麼作用?
答:過濾板作用:A、建立機頭壓力;B、過濾物料中的雜質;C、將螺桿頭部物料由螺旋流動轉變為沿濾孔作軸向流動;。
3、什麼機臺需使用多孔板?
答:單螺桿、部分雙螺桿擠出機由其結構、塑化能力以及廢料回收過濾雜質等,並根據實際情況決定是否使用多孔板。
4、螺桿下料的冷卻水裝置有什麼作用?
答:防止物料受熱結團,造成螺桿加料段處的物料無法及時均勻的往前輸送,即所謂不“吃料”。
5、物料在料筒的塑化中跟哪些因素有關?
答:物料在料筒的塑化跟受熱與螺桿剪切熔融作用有關。同等條件下,受熱溫度越高,受剪切強度越大,塑化越好。
6、同一物料受剪切作用跟哪些因素有關?
答:同一物料受剪切作用強度取決於螺桿槽中物料的填充程度。螺桿間隙的大小,螺桿的直徑與螺槽深度越大,螺桿轉速越快,則剪切作用越大。
7、料筒內物料通常以何程度填充螺桿為佳?為什麼?
答:以使物料2/3程度填充螺桿為佳,因為填充螺桿太少,螺桿下方充料、上方無料,造成螺桿上翹,與料筒摩擦厲害,易使螺桿與料筒受損,且物料受剪切強度小,塑化不良,影響制品質量。反之太多的話,造成物料包住螺桿排氣性差。甚至從排氣孔冒料,也會影響制品質量。
8、料筒溫度采用反向設置有何好處?
答:A、促使PVC物料在排氣段前部分塑化,有利水汽揮發物的逸出,但塑化太好時,不利於充分排氣。B、避免幹粉在排氣段被抽跑。C、可適當降低扭矩,並可避免物料高溫粘附料筒。
10、塑化程度對沖擊性能有什麼影響?
答:塑化太好或不足都會減弱沖擊性能。因此沖擊性能不合格,一定要結合制品外觀內壁橫切面等的癥狀,在工藝及參數調整上作出正確措施。
11、什麼原因會造成產品內壁有規則螺桿印跡?
答:螺桿與物料溫度太高或轉速太快,都可能造成內壁出現規則螺桿印跡。原料潮濕也可能造成內壁有波浪裝的印跡(一般為PP、PE等物料的癥狀)
12、產品內壁毛糙是工藝溫度太高還是太低?怎麼判斷?
答:二者都會引起內壁毛糙,若內壁發亮或全面粗糙、外表變色是溫度偏高,特別是料筒三、四段偏高;若內壁有生料顆粒,表面暗淡,則溫度偏低。因此,小產品發生毛糙現象,要剖開判斷清楚,以免誤斷。
13、哪些因素造成產品外壁波浪紋?
答:A、真空太大;B、冷卻效果差;C、產品壁厚不勻;D、產品浸泡在冷卻水裡瞭。
14、產品進定徑套易堵死可采取何措施?改措施有何副效應?
答:產品進定徑套易堵死可用:A、檢查定型冷卻水是否堵塞;B、滴水解決或加快牽引速度;C、降低真空壓力或是關閉真空泵,減少牽引阻力。
該措施產生副效應有:A、冷卻水會流向模具局部或是產品破裂後進水,使產品內積水,使物料出料快慢不一,甚至會斷裂現象。
15、哪些因素造成產品彎曲?
答:A、壁厚偏差;B、機頭冷卻水槽(托架)牽引切割等設備中心不在同一條直線上;C、定型冷卻水冷卻不均勻;D、出料快慢不一致;E、產品內壁有水。
16、定徑套未與產品同心有什麼影響?為什麼?
答:A、產品易堵死;B、造成產品壁厚偏差。
因為靠近定徑套一邊,先受冷收縮拉動其四周物料往其靠攏,這一效應可在不造成堵死的情況,以調整壁厚偏差或同心線。
17、產品壁厚偏差由哪些因素造成?如何解決?
答:A、口模與芯模中心不對正,調整口模與芯模同心;B、機頭受熱不均,檢查加熱圈是否包緊或是否局部損壞;C、熔融料在機頭分解有滯料,應清理幹凈。
18、產品的壁厚尺寸由什麼因素決定?
答:由口模與芯棒之間的間隙和牽引速度與擠出速度(擠出量)決定。
19、哪些因素會造成白色產品有黑色花紋?
答:A、螺桿與料筒間隙太小或是螺桿料筒磨損嚴重,摩擦造成花紋有規律成線型(這種現象一般為白色產品從模具出來後一般在下方出現花紋);B、螺桿漏油;C、原料問題,主要是回收料污染,用含硫有機錫的物料和含有鉛鹽的物料,兩者混合會發生硫污染現象。
20、哪些因素會造成白色產品有紅色花紋?
答:A、回收料含有分解料或其他紅色破碎料;B、真空排氣孔堵死一段時間後積料掉下被帶出來;C、料溫度太低或機臺加工溫度不夠;D螺桿間隙變掉,出現不勻部分分解部分不塑化。
21、產品變形由哪些因素造成?應采取何措施?
答:A、定徑套本身變形,應更換或校正定徑套;B、定型水太小真空不夠大,造成產品未定型下墜失圓,應加大定型水或真空度;C、牽引壓的太緊壓扁,應適當調整牽引履帶間隙;D、定型箱內托輪位置太高,造成產品下端扁平,應調整好拖輪使得同心;E、冷卻水沖擊太大使得沒有被真空定型好就冷卻瞭,應適當減小水流量。
22、哪些因素造成產品外觀無關?
答:A、口模溫度太高或太低都會表面光澤暗淡;B、口模內表面粗糙,精度太低;C、擠出速度太快,真空度不夠。
23、哪些因素造成產品有焦粒?
答:A、原料本身問題;B、螺桿磨損嚴重間隙變掉;C、機頭內物料分解,粘有滯料。
24、哪些因素造成產品內有明顯拼縫線(支架線)?
答:A、機頭或芯棒溫度太低;B、擠出速度太快,熔料在模體塑化不良;C、模具結構設計不合理瞭,壓縮比太小;D、配料結構不合理,流動性太好。
25、哪些因素造成產品內有裂痕?
答:A、原料內混有雜質;B、加工溫度太低;C、牽引速度太快(大間隙拉薄產品);D、配料結構不理想。
26、哪些因素造成產品壁有塊狀物凸起?
答:A、原料內混有雜質;B、加工溫度太低,不塑化或是溫度太高分解後的氣體造成;C、配料結構不理想。
27、中途換料時,需註意哪些問題?
答:A、不管料溫如何,應先將各區溫度提前適當降低;B、換料時,密切註意電流或扭矩變化,如發現扭矩上升較快,需立即減少給料或停止給料;C、如扭矩基本不變,此時應打開機筒抽真空裝置,觀察真空塑化及料在螺槽的充滿情況;D、將料量控制在適當范圍,使料體積占螺槽體積的2/3左右,使其處於半塑化狀態;E、當產品擠出口模時觀察其狀況,然後再調整各轉速及各區溫度,使料塑化良好,達到生產要求。
28、產品內外壁分解的原因及調整方法是什麼?
答:一、產品內壁分解的原因及調整方法
A、產品溫度過高,降低機身各區及混料溫度;B、螺桿油溫過高,降低螺桿油溫;C、給料太多,真空冒料,降低給料轉速,控制冒料;D、機身串溫,降低同步轉速及找機修維修;E、同步轉速較高,適當降低同步轉速;、F、芯棒溫度太高,適當降低芯棒溫度;G、配方不合理,找工藝員解決。
二、產品外壁分解的原因及調整方法
A、機頭加熱圈失控,經常實測各區溫度,註意觀察熱電偶是否完全插在孔的底部或是熱電偶孔內有雜物使其接觸不好,或交流接觸器是否粘死;B、模具漏料造成外壁分解,拆模處理;C、擠出速度太慢造成外壁分解,適當提高同步轉速;D、配方不合理,找工藝員處理。
29、產品沖擊不合格的原因及改進措施是什麼?
答:一、內壁粗糙:該現象是造成產品偏脆最嚴重的一種現象,哪怕一點點粗糙也會給產品沖擊來很大影響,故在生產時寧可使產品偏皺一點也不能粗糙。改進方法:A、加大主機抽真空度,使填充料量控制在適當范圍,勿使其冒料;B、降低機身溫度及同步轉速;C、如配方未變,攪拌應縮短冷拌時間;D、避免機身串溫。
二、塑化不良:解決方法:A、配方改進;B、升高各區溫度或延長攪拌時間而提高混料溫度;C、降低同步轉速,使得物料在機臺裡面塑化好瞭再擠推出去。
三、模具壓縮比偏小:壓縮比偏小不易使物料塑化均勻,易造成產品密實度較小,使產品脆,應加大模具壓縮比。
第五章 生產異常情況分析探討
一、變形
張傢港中傲模具
手機:13862214168
電話:0512—58969967
E-mail : [email protected]

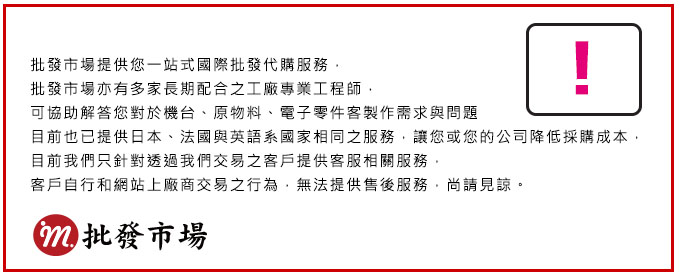
批發市場僅提供代購諮詢服務,商品內容為廠商自行維護,若有發現不實、不合適或不正確內容,再請告知我們,查實即會請廠商修改或立即下架,謝謝。