加工定製 | 是 | 作用對象 | 鑄鐵 | 工藝類型 | 翻砂鑄造模 |
適用范圍 | 日用品,汽車,醫療,餐具,工藝品,電子,傢電 |
壓鑄
將熔融合金在高壓、高速條件下充型,並在高壓下冷卻凝固成形的精密鑄造方法。
壓鑄模
壓力鑄造成形工藝中,用以成形鑄件所使用
壓鑄模的結構組成
一).壓鑄模結構組成
定模:固定在壓鑄機定模安裝板上,有直澆道與噴嘴或壓室聯接
動模:固定在壓鑄機動模安裝板上,並隨動模安裝板作開合模移動合模時,閉合構成型腔與澆鑄系統,液體金屬在高壓下充滿型腔;開模時,動模與定模分開,借助於設在動模上的推出機構將鑄件推出.
二).壓鑄模結構根據作用分類
型腔:外表麵直澆道(澆口套)
成型零件二)澆註系統模澆道(鑲塊)
型芯:內表麵內澆口
餘料
(三)導準零件:導柱;導套
(四)推出機構:推桿(頂針),復位桿,推桿固定板,推板,推板導柱,推板導套.
(五)側向抽芯機構:凸臺;孔穴(側麵),鍥緊塊,限位彈簧,螺桿.
(六)排溢系統:溢澆槽,排氣槽.
(七)冷卻系統
(八)支承零件:定模;動模座板,墊塊(裝配,定位,安裝作用)
壓鑄模采購
選擇信譽好、技術高、經驗豐富的專業壓鑄模具廠製造模具。壓鑄模是一種特殊的精密機械,那些專業壓鑄模具廠,他們有適合生產壓鑄模具的精密機床,能確保模具尺寸精度;他們有經驗豐富的高級模具技師,技師的豐富經驗是壓鑄模具實用好用的保證;他們與材料供應商和熱處理廠有密切的關系,他們有完善的售後服務體系……。良好的模具設計與製造是壓鑄模具長壽命、低故障、高效率的基礎。低價位的劣質壓鑄模,將會以壓鑄生產中表現出的低生產效率、高故障,讓您浪費很多昂貴的壓鑄工時,花去更多的金錢。
壓鑄模安裝
模具安裝調整工應經過培訓合格上崗
⑴、模具安裝位置符合設計要求,盡可能使模具漲型力中心與壓鑄機距離最小,這樣可能使壓鑄機大杠受力比較均勻。
⑵、經常檢查模具起重吊環螺栓、螺孔和起重設備是否完好,確保重吊時人身、設備、模具安全。
⑶、定期檢查壓鑄機大杠受力誤差,必要時進行調整。
⑷、安裝模具前徹底擦凈機器安裝麵和模具安裝麵。檢查所用頂桿長度是否適當,所有頂棒長度是否等長,所用頂棒數量應不少於四個,並放在規定的頂棒孔內。
⑸、壓板和壓板螺栓應有足夠的強度和精度,避免在使用中松動。壓板數量應足夠多,最好四麵壓緊,每麵不少於兩處。
⑹、大型模具應有模具托架,避免在使用中模具下沉錯位或墜落。
⑺、帶較大抽芯的模具或需要復位的模具也可能需要動、定模分開安裝。
⑻、冷卻水管和安裝應保證密封。
⑼、模具安裝後的調整。調整合模緊度。調整壓射參數:快壓射速度、壓射壓力、增壓壓力、慢壓射行程、快壓射行程、沖頭跟出距離、推出行程、推出復位時間等。調整後在壓室內放入棉絲等軟物,做兩次模擬壓射全過程,檢查調整是否適當。
⑽、調整合模到動、定模有適當的距離,停止機器運行,放入模具預熱器。
⑾、把保溫爐設定在規定溫度,配置好規定容量的舀料勺。
12 生產前確認模具完整性
有中子之模具正確接好中子油管及控製開關線路等,確認導電部分之金屬不外露,並選擇好控製程序方能操作。
13有倒拉裝置的模具必須裝好倒拉桿,頂針頂出後必須退回,否則會損壞模具型腔。
兩次開模斜抽芯模具,開模時,後模前半部分必須先彈開,否則會損壞模具型芯。
模具上方及左右有滑塊的模具,必須加裝適當的彈簧固定。
有滑塊型芯、抽芯和結構復雜易卡模之模具生產前應充分預熱(模具預熱前必須對模腔各部位打油)。
對型芯有方向要求或型腔共用之模具,須確認型芯之正確性。
確認每條冷確水路通暢
壓鑄模的正確使用
製定正確的壓鑄工藝,壓鑄工正確熟練的操作和高質量的模具維修,對提高生產效率,保證壓鑄件質量,降低廢品率,減少模具故障,延長模具壽命致關重要。
(一)製定正確的壓鑄工藝
壓鑄工藝是一個壓鑄工廠技術水平的體現,他能把壓鑄機特性、模具特性、鑄件特性、壓鑄合金特性等生產要素正確的結合起來,以最低的成本,生產滿足客戶要求的壓鑄產品。因此,必須重視壓鑄工藝工程師的選拔和培訓。壓鑄工藝工程師是壓鑄生產現場技術總負責人,除製定正確的壓鑄工藝,根據生產要素變化及時修訂壓鑄工藝外,還負責對模具安裝調整工、壓鑄操作工、模具維修工的培訓和提高。
⑴、確定最合理的生產率,規定每一次壓射周期的循環時間。過低的生產率固然不利於提高經濟效益,過高的生產率往往以犧牲模具壽命和鑄件合格率為代價,算總帳細帳經濟益可能更差。
⑵、確定正確的壓鑄參數。在確保鑄件符合客戶質量標準的前提下,應使壓射速度、壓射壓力、合金溫度最低。這樣,有利於降低機器、模具負荷,降低故障,提高壽命。根據壓鑄機特性、模具特性、鑄件特性、壓鑄鋁合金特性等腰三角形,確定快壓射速度、壓射壓力、增壓壓力、慢壓射行程、快壓射行程、沖頭跟出距離、推出行程、保壓時間、推瞭復位時間、合金溫度、模具溫度等。
⑶、使用水基塗料,必須製訂嚴格詳細的噴塗工藝。塗料品牌,塗料與水的比例,模具每一個部位的噴塗量(或噴塗時間)和噴塗順序,壓縮空氣壓力,噴槍與成型表麵的距離,噴塗方向與成型表麵的角度等。
⑷、根據壓鑄模實際確定正確的模具冷卻方案。正確的模具冷卻方案對生產效率、鑄件質量、模具壽命有極大的影響。方案應規定冷卻水開戶方法,壓鑄幾個模次開始冷卻,相隔幾個模次分幾次把冷卻水閥門開到規定開度。點冷卻系統的冷卻強度應由壓鑄工藝工程師現場調定,配合噴塗達到模具熱平衡。
⑸、規定對不同滑動動部位,如沖頭、導柱、導套、抽芯機構、推桿、復位桿等部位的不同潤滑頻率。
⑹、製訂每一個壓鑄件的壓鑄操作規程,並培訓和監督壓鑄工按規程操作。
⑺、根據模具復雜程度和新舊程度,確定適當的模具預防性維修周期。適當的模具預防性維修周期應當是模具使用中將要出現故障而還沒有出現故障的壓鑄模次。模具使用中已經出現故障,不能繼續生產,被迫進行修理,不是被提倡的方法。
⑻、根據模具復雜程度、新舊程度和粘模危險程度,確定模塊消除應力周期(一般5000—15000模次進行一次)和是否需要進行表麵出理。如氮化處理,氮化層深度。0.33,最大0.55。
(二)實施正確的壓鑄操作壓鑄工應經過培訓合格後上崗
⑴、嚴格執行壓鑄工操作規程,嚴格控製第一模次的循環時間,其誤差應小於10%。穩定的壓鑄循環時間,對一個鑄工廠的綜合效益至關重要。對產品質量穩定性、模具壽命、故障率等都有決定性影響。
⑵、嚴格執行模具冷卻方案,模具冷卻是提高生產效率、鑄件質量、模具壽命,減少模具故障的有效方法。但是,錯誤的水冷卻操作,將對模具造成致命傷害。停止壓鑄生產,必須立即關閉冷卻水。
⑶、澆柱撇潭、舀鋁、澆柱動作規范,做到舀入的金屬液不含氧化皮,澆入壓室的金屬液最少波動。手工澆註澆入量誤差控製在2—3%以內。
⑷、清模及時清除積留在分型麵、型腔、型芯、澆道、溢流槽、排氣道等處的金屬肖積垢,防止合模時壓塌模具表麵,堵塞排氣道,或造成合模不嚴。清模時禁止使用鋼製工具接觸成型表麵。
⑸、噴塗噴塗是最重要、難度最大的壓鑄操作之一,必須嚴格按噴塗工藝操作。不正確的噴塗會使產品質量不穩定和模具早期限損壞。
⑹、按規定及時對滑動部位進行潤滑。
⑺、隨時註意合模緊度,經常檢查模具壓板壓緊情況和模具托架支撐情況,防止在使用中模具下沉或墜落。
⑻、完成一個模具維修周期的模次,或完成規定的生產批量後停止生產,要保留最後一個壓鑄產品(最好帶澆、排系統),與模具一起送修。

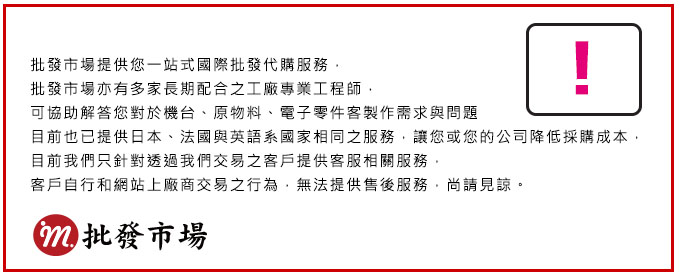
批發市場僅提供代購諮詢服務,商品內容為廠商自行維護,若有發現不實、不合適或不正確內容,再請告知我們,查實即會請廠商修改或立即下架,謝謝。