由於玻璃鋼拉擠成型工藝自動化程度高、工藝穩定,隨著玻璃鋼復合材料應用市場的不斷拓展,玻璃鋼拉擠製品所占份額也越來越大。在整個成型工藝中,玻璃鋼拉擠模具是實現順利生產的中心環節。模具的設計與加工水品決定瞭成型工藝的效率,同時還影響著製品的外觀與質量。模具一但加工定型後將很難改變,屆時會給生產造成很大的經濟損失。
玻璃鋼拉擠模具設計加工
在玻璃鋼拉擠成型工藝過程中,模具是各種工藝參數作用的交匯點,要求玻璃鋼拉擠模具有精密的尺寸穩定性、優良的耐磨性和極低的表麵粗糙度。玻璃鋼拉擠產品生產商目前常用的模具主要為獨孔模具和分型模具。
模具設計加工過程中註意以下要點
1、模具材料選擇及加工類型
玻璃鋼拉擠模具材料應能滿足強度高、熱處理變形小、加工性能好、使用過程中尺寸穩定性好、耐磨、耐熱及耐熱腐蝕等。目前常用模具材料為40Cr鍛件,耐磨要求高的可選用P20、Cr12MoV、38CrMoAl和優質S45C鋼材等,型腔表麵硬度應大於HRC50,型腔表麵粗糙度必須達到華氏十級。此外,為瞭使材料滿足玻璃鋼拉擠模具的工藝要求,通常還要經過鍛造,退火、粗銑、調質、精銑、淬火、研磨、電鍍等一系列工序。
目前玻璃鋼拉擠成型工藝中常用的模具類型主要有兩大類:一類是鍍鉻模具,即模具機加工完成後進行拋光、電鍍。對於一般產品和小件產品這種模具加工形式比較經濟耐用,使用過程中如果出現鉻層脫落的現象,還可以褪鉻後重新鍍鉻再次使用,但對於大件寬幅模具,鍍鉻過程中如果控製不當會出現鉻層薄厚不均的現象,主要是中間部位偏薄而周邊部位偏厚,對於尺寸精度要求較高的產品該類型不能滿足要求。另一類是直接采用高性能鋼材加工或模腔表麵進行氮化處理,這樣模腔尺寸精度較高,但如果長期不用模具必須註意保養,防止生銹。這裡需要註意的是拉擠生產過程中如果生產白色製品,建議使用鍍鉻模具,避免玻纖及填料在對模腔磨損過程中造成產品表麵有灰黑色的磨痕。
2、模具尺寸的設計
玻璃鋼擠拉模具的橫截麵應足夠大,以使模具具有一定的熱容,保證加熱均勻、穩定,一般來說,鋼模的橫截麵至少等於拉擠製品截麵積的10倍。但目前隨著模具材料性能及加工工藝水平、玻璃鋼拉擠成型工藝水平的提高,很多模具的橫截麵麵積設計比製品截麵積大不瞭多少,工藝性能同樣優異。為保證產品在模具內受熱均衡,有的模具的截麵形狀可加工成和產品截麵形狀一致或掏空一部分。
模具的長度與設備加熱能力,樹脂特性及配方,製品幾何尺寸及擠拉速度有關。典型的模具長度在500~1500 mm之間。對固定截麵的製品,適當增加模具長度可提高擠拉速度,提高生產效率,但會導致牽引力的加大。
模具型腔尺寸決定於製品的尺寸及收縮率。不飽和聚酯樹脂/玻璃纖維體系,收縮率一般在2%左右,乙烯基樹脂,環氧樹脂,收縮率要低些,一般在0.8%左右。填料,玻纖含量及所在截麵位置的不同,收縮率也有差異。需要註意,在設計中,拉擠製品的截麵形狀必須依照拉擠工藝的特點進行截麵形狀設計。早期人們沿用鋼構件標準設計FRP製品,由於FRP是非均質材料,固化過程中會收縮致使製品產生變形。因此在模具設計時需要加以補正。如角型材在模具設計時若采用90°,生產出的製品會向內收縮變形,實際角度會小於90°度,因此可通過模具設計時將角度放大1~2°來控製。另外一種方式就是在設計那些拐角位置時,內外圓角取值要做些相對調整,該處厚度不宜過厚。
3、玻璃鋼拉擠模具的一些細節設計
入口的設計:入口的設計也是玻璃鋼擠拉模具的關鍵之一,在此由於纖維束體積縮小而壓力升高,而入口處的幾何形狀是重要的影響因素。通常的入口形式可采用喇叭口形,但實際生產中有的模具隻作簡單的入模倒角設計即可,而有的模具不光要設計一定的入模角度進行加工,有時還需輔助加工一些倒紗溝,以利於產品尖角或凸臺的成型。有時為瞭產品下氈包氈順利,模具入口處可以考慮將下模突出一部分利於氈的定位和走向。
模腔內部倒角的設計:擠拉模具還有一特殊要求,那就是在模具設計時應盡量避免一些細小的突出和銳角出現,如果設計中有上述結構,在模腔內固化成型過程中該位置會出現紗和氈走不到位的情況,容易造成粘模,使製品表麵出現缺損,甚至最終導致擠拉的失敗。所以製品的棱邊最好采用2~5°的圓角過渡。當然隨著原材料種類的增加,如膨體紗的出現可有效避免邊角的粘模現象,如果產品在棱邊方麵有特殊要求的話,型腔棱邊處也是可以做到為直角的。

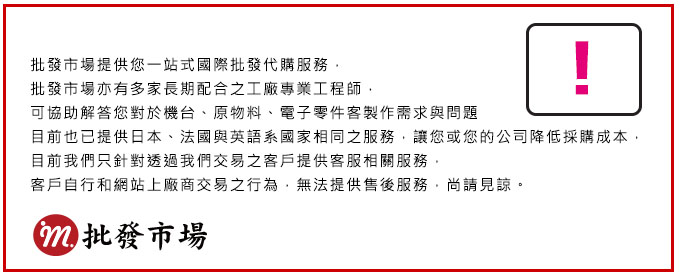
批發市場僅提供代購諮詢服務,商品內容為廠商自行維護,若有發現不實、不合適或不正確內容,再請告知我們,查實即會請廠商修改或立即下架,謝謝。