一、 反應釜結構形式應用環境
反應釜由鍋蓋、筒身、夾套、攪拌器、軸封傳動裝置及支承等組成,與鍋內物料接觸處的鍋體和零部件均采用OCr18Ni9或1Cr18Ni9Ti不銹耐酸鋼板製成。攪拌器有錨式、框式、槳式、渦輪式,刮板式,組合式,轉動機構可采用擺線針輪減速機、可滿足各種物料的特殊反應要求。無級變速減速機,密封裝置可采用機械密封,加熱冷卻可采用夾套、半管、盤管、米勒板等結構,加熱方式有蒸汽、電加熱、導熱油,以滿足耐酸、耐高溫、耐磨損、抗腐蝕等不同工作環境的工藝需要。可根據用戶工藝要求進行設計、製造。反應釜是我公司在吸收國內外先進技術的基礎上研製成功的新型產品。廣泛地應用於醫藥、建材、化工、顏料、樹脂、食品等行業,具有加熱迅速、耐高溫、耐腐蝕、衛生、無環境污染、無需鍋爐自動加溫、使用方便等特點。
推進漿型是把漿型分成快速型與慢速型兩類,前者在湍流狀態操作,後者在層流狀態操作。
反應釜選用時根據攪拌目的及流動狀態來決定漿型及擋板條件,流動狀態的決定要受攪拌介質的粘度高低的影響。其使用條件比較具體,不僅有漿型與攪拌目的,還有推進的介質粘度范圍、攪拌轉速范圍和槽的容量范圍。提出的選型表也是根據攪拌的目的及攪拌時的流動狀態來選型,它的優點還在於根據不同攪拌過程的特點劃分瞭漿型的使用范圍,使得選型更加具體。
二、主要技術參數:
型號 | 公稱容量L | 實際容量L | 加熱功率KW*支 | 油夾套容量L | 內鍋尺寸Dmm | 夾套尺寸D1mm | 支座螺孔中心D2mm | 攪拌轉速 | 重量kg |
50L | 50 | 78 | 2*4 | 96 | Ø400 | Ø600 | Ø828 | 85 | 4-25 |
100L | 100 | 127 | 2*6 | 127 | Ø500 | Ø700 | Ø928 | 85 | 4-25 |
300L | 300 | 327 | 4*6 | 218 | Ø800 | Ø1000 | Ø1148 | 85 | 4-25 |
500L | 500 | 509 | 4*9 | 269 | Ø900 | Ø1100 | Ø1252 | 85 | 4-25 |
1000L | 1000 | 1017 | 4*12 | 400 | Ø1200 | Ø1400 | Ø1588 | 85 | 4-30 |
2000L | 2000 | 2154 | 4*15 | 850 | Ø1400 | Ø1600 | Ø1840 | 85 | 4-30 |
3000L | 3000 | 3201 | 5*15 | 1015 | Ø1600 | Ø1750 | Ø2040 | 85 | 4-35 |
4000L | 4000 | 4020 | 5*15 | 1226 | Ø1600 | Ø1750 | Ø2070 | 85 | 4-36 |
5000L | 5000 | 5170 | 5*18 | 1400 | Ø1800 | Ø2000 | Ø2320 | 85 | 4-36 |
反應釜的加熱方式
反應釜加熱方式有電加熱、熱水加熱、導熱油循環加熱、遠紅外加熱、外(內)盤管加熱等,冷卻方式為夾套冷卻和釜內盤管冷卻,攪拌槳葉的形式等。支承座有支承式或耳式支座等。轉速超過160轉以上宜使用齒輪減速機。開孔數量、規格或其它要求可根據用戶要求設計、製作。
蒸汽反應釜
使用的前提是客戶本身備有外加入源(如蒸汽)或冷卻源(如自來水) 。必須註意,蒸汽加熱方式為上進下出液體加熱或冷卻為下進上出。在各種方式出口管路無閥門,保證暢通。
電加熱反應釜
電加熱反應釜具有加熱迅速、耐高溫、耐腐蝕、無環境污染等特點,廣泛應用於石油、化工、橡膠、農藥、染料、醫藥、食品等行業,也用來完成硫化、硝化、氫化、烴化、縮合、聚合等工藝過程。電加熱反應釜材質一般有碳錳鋼、不銹鋼、鋯、鎳基(哈氏、蒙乃爾、因康鎳)合金及其它復合材料;根據反應釜的製造結構可分為開式平蓋式反應釜、開式對焊法蘭式反應釜和閉式反應釜 三大類,每一種結構都有他的適用范圍和優缺點。根據反應釜的密封型式不同可分為:填料密封,機械密封和磁力密封。
三、反應釜的安裝使用:
1、 應安裝在堅固、平整的工作臺上,工作臺高度根據使用情況決定,設備與工作臺四周應留有一定的空間(≥360cm),以便安裝與後期維修。
2、 安裝時要求傳動軸與地水平麵垂直,不垂直度(傾斜度)不得大於設備總高度的1/1000。
3、 設備本身各工藝接管上的自備件,安全閥,必須按反應釜的要求配備。
4、 安裝完畢檢查各連接部件及傳動部位是否牢固可靠,各連接管道、管口、密封件及整機做氣密試驗,應無泡、冒、滴、漏現象。
5、 開機前減速機註入46#機械油,打開電機防護罩用手轉動風葉檢查有無卡怠現象,攪拌槳有無刮壁現象,清理釜內污物,方可開機。空車運轉30分鐘無不正常噪音、振動,方可正式投料生產。另視生產情況定期更換減速機油。
四、幾種密封的使用條件
1.通常在常壓或低壓條件下采用填料密封,一般使用壓力小於2公斤。
2.在一般中等壓力或抽真空情況會采用機械密封,一般壓力為負壓或40公斤。
3.在高壓或介質揮發性高得情況下會采用磁力密封,一般壓力超過14公斤以上。
除瞭磁力密封均采用水降溫外,其他密封形式在超過120度以上會增加冷去水套。
五、註意事項
維護及安全
1、應嚴格按 產品銘牌上標定的工作壓力和工作溫度操作使用,以免造成危險。 2、嚴格遵守產品使用說明書中關於冷卻、註油等方麵的規定,做好設備的維護和保養。 3、所有閥門使用時,應緩慢轉動閥桿(針),壓緊密封麵,達到密封效果。關閉時不易用力過猛, 以免損壞密封麵。 4、電氣控製機表應由專人操作,並按規定設置過載保護設施。
六、常見故障現象及原因
1、故障現象:密封麵處出現泄漏。 故障原因:螺桿螺紋松動;密封麵損傷。 排除方法:將螺桿重新上緊;重新修磨拋光密封麵。
2、故障現象:閥門處出現泄漏。 故障原因:閥桿(針)、閥口密封麵損傷。 排除方法:維修、更換閥桿(針)、閥口。
3、故障現象:外磁鋼旋轉,內磁鋼不轉,電機電流減小。 故障原因:釜內溫升過高,冷卻循環不暢,內磁鋼因高溫褪磁。 加氫反應,內磁鋼套有裂紋,內磁鋼膨脹。 排除方法:通知供貨商,重新更換內磁鋼。
4、故障現象:磁力耦合傳動器內有摩擦的噪音。 故障原因:軸套、軸承磨損,間隙過大,內磁鋼轉動出現跳動。 排除方法:與供貨商聯系,更換軸承、軸套。
反應釜幾種常見的結構示意圖
七、保養
反應釜要經常註意整臺設備和減速器的工作情況,減速器潤滑油不足應立即補充,電加熱介質油每半年要進行更換,對夾套和蓋子上等部位的安全閥、壓力表、溫度表、蒸餾孔、電熱棒、電器機表等要應定期檢查,如果有故障要即時調換或修理,設備不用時,一定用溫水在容器內外壁全麵清洗,經常擦洗鍋體,保持外表清潔和內膽光亮,達到耐用的目的。
八、設計參考
反應釜多半都設計成圓柱形,其徑/長比為0.66/1.0。其頂和底製成碟狀。頂蓋用凸緣狀的法蘭固定,底則焊接在殼體上。
頂蓋上設有若乾個開口如人孔、攪拌桿及熱電偶等。反應釜的加熱方式有如下幾種。
a)用煤、木材、燃油在底部直接加熱。
b)用電熱元件在外側加熱或用循環熱媒在夾套內加熱。
c)浸入的盤管通熱油加熱。
九、反應物料
在反應中常用的反應物料有:
1、相容或不相容的液體。液體的混合很容易通過攪拌或機械混合來實現,反應混合物的傳熱是通過對流進行的。
2、液體與適當粒徑的固體反應物的非均相混合。在這種情況下借助混合器不可能將這些物料完全混合。混合作用力一消失,固體物料便會沉淀到釜底形成一不導熱的物料層並出現下述現象:
·固體反應物炭化, ·混合物顏色變深, ·炭化的物料浪費瞭,
·熱能和時間浪費瞭, ·聚合反應不均勻, ·聚合物成分不均勻, ·由於物料和能量的浪費而影響生態環境。
為瞭避免出現這些問題,可以分兩步多次添加反應物料:
a)第一步先將液體反應物料加到反應釜中將介質溫度加熱到稍高於反應溫度或固體反應物的熔點。
b)在不斷攪拌的情況下慢慢添加固體反應物讓它不斷反應或溶解,避免發生沉淀。但是這種速度不可能精確保持,有時還會發生沉淀和結焦的現象。而且這樣需要很長時間才能完成反應。
十、新的設計概念
為瞭避免上述固體反應物料沉淀到釜底的情況發生,設計瞭一種新的反應釜。反應釜的基本設計和加熱方式保持不變。主要的變化是改進反應釜底。
因為所有的問題都是因為固體反應物料沉淀到釜底造成的。那麼主要的解決辦法是要在即使沒有混合或攪拌的情況下也要避免發生沉淀。這可通過加進一個輔助的釜底而實現,該輔助的底比實際的稍高一點,留出3~10厘米的間隙。這樣固體反應物將沉淀在這個輔助的底 上,而不會在實際的反應釜底上形成絕熱層。通過釜底間隙間的對流作用熱傳遞將是連續均 勻的。
輔助的釜底用高強度不銹鋼製成,上麵帶有許多小孔,孔徑比反應物料的粒徑略小。將這種篩網切成圓形。其邊緣向下彎曲作支撐。當固體反應物料負荷 很重時,輔助底下 麵可以加一個5~10厘米寬的金屬環作為支承。 這樣便可避免固體物料集中在釜底,因過熱而引起的物料炭化,產物顏色變深。 這種金屬篩網可從市埸上購到,對於50~100立升的小反應釜也可以自己設計製造。
十一、反應釜的技術特點
與傳統的夾套式反應釜相比,大容量反應釜具有以下特點:
1、 生產能力大
大容量反應釜以單層釜壁取代瞭傳統的夾套式釜壁,使反應容器不承受或隻承受較小的外壓,因而擺脫瞭傳統的外壓容器由於容積增加而帶來的釜壁過厚、傳熱不良等因素的限製,使得反應釜的容積量可達到 30m 3 ,甚至更大,這大大提高瞭單釜生產能力。
2、 傳熱系數高
反應介質的加熱和冷卻均采用內置板式換熱器,傳熱系數比傳統的盤管式換熱器高 40% ,而且板式換熱器結構較緊湊,有利於在容積較大的反應釜內佈置充足的加熱和冷卻麵積,使樹脂的合成反應過程進行得更加均勻、穩定。
3、 易於維修
由於內置板式換熱器是可拆卸的,因此易於清洗和維修,有利於減少操作故障,提高生產的穩定性。
綜上所述,大容量反應釜具有生產能力大、傳熱效果好、易於維修特點,應用於生產實踐中可以減少設備臺數,節約廠房投資,減少操作人員,降低生產成本。因此,大容量反應釜愈來愈廣泛地被應用於人造板膠粘劑的生產中。
發展趨勢
合理地利用熱能,選擇最佳的工藝操作條件,加強保溫措施,提高傳熱效率,使熱損失降至最低限度,餘熱或反應後產生的熱能充分地綜合利用。熱管技術的應用,將是今後反應釜發展趨勢。大容積化,這是增加產量、減少批量生產之間的質量誤差、降低產品成本的有效途徑和發展趨勢。染料生產用反應釜國內多為6000L以下,其它行業有的達30m3;國外在染料行業有20000~40000L,而其它行業可達120 m3。反應釜的攪拌器,已由單一攪拌器發展到用雙攪拌器或外加泵強製循環。反應釜發展趨勢除瞭裝有攪拌器外,尚使釜體沿水平線旋轉,從而提高反應速度。電加熱將電阻絲纏繞在反應釜筒體的絕緣層上,或安裝在離反應釜若乾距離的特設絕緣體上,反應釜操作溫度較高,通常化學反應需要在一定的溫度條件下才能進行,所以反應釜既承受壓力又承受溫度。獲得高溫的方法通常有水加溫要求溫度不高時可采用,其加熱系統有敞開式和密閉式兩種。敞開式較簡單,它由循環泵、水槽、管道及控製閥門的調節器所組成,當采用高壓水時,設備機械強度要求高,反應釜外表麵焊上蛇管,蛇管與釜壁有間隙,使熱阻增加,傳熱效果降低。蒸汽加熱加熱溫度在100℃以下時,可用一個大氣壓以下的蒸汽來加熱;100~180℃范圍內,用飽和蒸汽;當溫度更高時,可采用高壓過熱蒸汽。用其它介質加熱若工藝要求必須在高溫下操作或欲避免采用高壓的加熱系統時,可用其它介質來代替水和蒸汽,如礦物油(275~300℃)、聯苯醚混合劑(沸點258℃)、熔鹽(140~540℃)、液態鉛(熔點327℃)等。在反應釜中通常要進行化學反應,為保證反應能均勻而較快的進行,提高效率,通常在反應釜中裝有相應的攪拌裝置,於是便帶來傳動軸的動密封及防止泄漏的問題。反應釜多屬間隙操作,有時為保證產品質量,每批出料後都需進行清洗;釜頂裝有快開人孔及手孔,深圳網路優化,便於取樣、測體積、觀察反應情況和進入設備內部檢修。以生產自動化和連續化代替笨重的間隙手工操作,如采用程序控製,既可保證穩定生產,提高產品質量,增加收益,減輕體力勞動,又可消除對環境的污染。因此,在電阻絲與反應釜體之間形成瞭不大的空間間隙。前三種方法獲得高溫均需在釜體上增設夾套,由於溫度變化的幅度大,使釜的夾套及殼體承受溫度變化而產生溫差壓力。采用電加熱時,設備較輕便簡單,溫度較易調節,而且不用泵、爐子、煙囪等設施,開動也非常簡單,危險性不高,成本費用較低,但操作費用較其它加熱方法高,熱效率在85%以下,因此適用於加熱溫度在400℃以下和電能價格較低的地方。
關於反應釜高溫碳化的介紹
利用電加熱反應釜高溫碳化,這是去除活性炭上有機物的科學方法,一般情況下高溫炭化階段是使活性炭上吸附的一部分有機物沸騰、汽化脫附,一部分有機物就會發生分解反應,生成小分子烴脫附出來,殘餘成分留在活性炭孔隙內成為“固定炭”。在這一階段,溫度將達到800~900°C,為避免活性炭的氧化,一般在抽真空或惰性氣氛下進行。接下來的活化階段中,往反應釜內通入CO2、CO、H2或水蒸氣等氣體,以清理活性炭微孔,使其恢復吸附性能,活化階段是整個再生工藝的關鍵。其他應用也有。就是使其有機物變成水,二氧化碳的過程。電加熱反應釜用電熱棒加熱夾套裡麵的導熱油,使導熱油溫度升到所需要的溫度,然後有測溫控製機控製電熱幫使期斷電恒溫。加熱時受熱不均水產生的水蒸汽遇冷體積突然變為零,產生響聲。電加熱反應釜用多少水關鍵是看你反應釜裡有多少物料,這些物料需要多少能量才能升到80度,電加熱容易控製溫度,但是如果建立瞭平衡,水換熱溫度更穩定。反應釜開車時一定要遵守下麵的要求一定要按工藝操作規程進料,啟動攪拌運行;反應釜在運行中一定要要執行工藝操作規程,不要超溫、超壓、超負荷運行;如果出現超溫、超壓、超負荷等異常情況,應該立即按工藝規定采取相應處理措施。按工藝規定的物料配比加料,均衡控製加料及升溫速度,防止因配比錯誤或加料過快引起釜內劇烈反應,出現超溫等異常情況。設備在升溫及降溫時,操作一定要平穩,避免溫差應力和壓力應力突然疊加,避免設備產生變形或受損;嚴格執行電加熱反應釜開車是的管理製度,將設備運行與完好情況列入交接班,杜絕因交接班不清出現異常情況和設備事故。
十二、反應釜安全操作規程
開車前
1.檢查釜內、攪拌器、轉動部分、附屬設備、指示機表、安全閥、管路及閥門是否符合安全要求。
2.檢查水、電、氣是否符合安全要求。
開車中
1.加料前應先矛攪拌器,無雜音且正常時,將料加到釜內,加料數量不得超過工藝要求。
2.打開蒸氣閥前,先開回氣閥,後開進氣閥。打開蒸氣閥應緩慢,使之對夾套預熱,逐步升壓,夾套內壓力不準超過規定值。
3.蒸氣閥門和冷卻閥門不能同時啟動,蒸氣管路過氣時不準錘擊和碰撞。
4.開冷卻水閥門時,先開回水閥,後開進水閥。冷卻水壓力不得低於0.1兆帕,也不準高於0.2兆帕。
5.水環式真空泵,要先開泵後給水,停泵時,先停泵後停水,並應排除泵內積水。
6.隨時檢查設備運轉情況,發現異常應停車檢修。
停車後
1.停止攪拌,切斷電源,關閉各種閥門。
2.鏟鍋時必須切斷攪拌機電源,懸掛警示牌,並設人監護。
3.反應釜必須按壓力容器要求進行定期技術檢驗,檢驗不合格,不得開車運行。

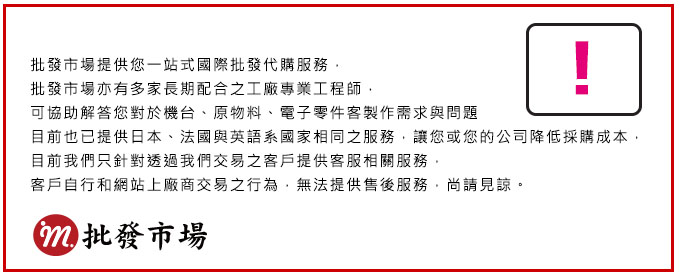
批發市場僅提供代購諮詢服務,商品內容為廠商自行維護,若有發現不實、不合適或不正確內容,再請告知我們,查實即會請廠商修改或立即下架,謝謝。