玻璃鋼管道是一種輕質、高強、耐腐蝕的非金屬管道。它是具有樹脂基體重的玻璃纖維按工藝要求逐層纏繞在旋轉的芯模上,並在纖維之間遠距離均勻地鋪上石英砂作為夾砂層。其管壁結構合理先進,能充分發揮材料的作用,在滿足使用強度的前題下,提高瞭鋼度,保證瞭產品的穩定性和可靠性。玻璃鋼夾砂管以其優異的耐化學腐蝕、輕質高強,不結垢,抗震性強,與普通鋼管比較使用壽命長,綜合造價低,安裝快捷,安全可靠等優點,被廣大用戶所接受。 玻璃鋼管道應用於石油、化工及排水等行業。
主要分為:夾砂管道,工藝管道,風管是一種輕質、高強、耐腐蝕的非金屬管道。它是具有樹脂基體重的玻璃纖維按工藝要求逐層纏繞在旋轉的芯模上,並在纖維之間遠距離均勻地鋪上石英砂作為夾砂層。其管壁結構合理先進,能充分發揮材料的作用,在滿足使用強度的前題下,提高瞭鋼度,保證瞭產品的穩定性和可靠性。玻璃鋼管道以其優異的耐化學腐蝕、輕質高強,不結垢,抗震性強,與普通鋼管比較使用壽命長,綜合造價低,安裝快捷,安全可靠等優點,被廣大用戶所接受。玻璃鋼 纏繞管道應用於石油、化工及排水等行業。近年來,我國玻璃鋼管道生產發展快,數量逐年上長,應用范圍及部門也越來越廣。
玻璃鋼纏繞管道采用樹脂(輸送飲用水采用食品級樹脂)、玻璃纖維、石英砂為原料,用特殊工藝製作而成。










1、具有優良的抗腐蝕性能
不要陰極防腐保護及其它防腐措施,不會對水和其它介質產生二次污染。產品使用壽命長。
2、重量輕
管道重量僅占同規格、同長度球墨鑄鐵管的1/4,水泥管道的1/10。運輸裝卸方便,易於安裝。
3、單根管道長度長
減少管線接頭,加速安裝速度,提高整條管線質量。
4、管壁內壁光滑
減少流阻、提高流速、降低能耗。用較小口徑的管道輸送同等流量的流體,與同規格鋼管相比可提高流量的10%左右;不結垢,長期使用不降低流速。擾和重蝕環境中電纜的防護都有較好效果。
(1)耐腐蝕性:化學惰性的材質,耐腐蝕性優異,並可根據輸送介質選擇不同的耐腐蝕管道。
(2)機械強度大:耐水壓強度,耐外壓強度和耐沖擊強度均良好並可按要求的壓力設計製造管道和管件。
(3)溫度適應性強:使用溫度范圍:大於-70攝氏度小於250攝氏度,冰凍介質下管道不裂。
(4)流體阻力小:管道內壁光滑,粗糙系數0.0084,相同流量下,管徑可予縮小。
(5)重量輕,壽命長:質輕,運輸便利,施工費用低,無須維修,使用壽命長達50年以上。
(6)保持水質:無毒,輸送飲水用水,能保持長期水質衛生。
由計算機控製,在芯模上按規定的與纖維纏繞玻璃鋼管相同的工藝製造內襯,凝膠後按設計好的線型和厚度纏繞結構層,並將石英砂與樹脂混合的砂漿纏在結構層中,最後纏繞外保護層。
四、原、輔材料:樹脂、短切纖維、連續玻璃纖維和石英砂。
五、產品規格
直徑:DN100-4000 壓力等級:0.1MPa、0.6MPa、1.0MPa、1.6MPa、2.0MPa、2.5MPa 剛度等級:SN1250、SN2500、SN5000、SN10000。
長度:6m、12m
管道安裝原則
管道安裝順序本著分片區、分系統,先大直徑後小直徑,先下層後上層,先難後易,先上管廊後連設備,與機器相連接的管道原則上是從裡向外配,以減少焊接應力對機器安裝精度的影響,室內與室外管線的碰口應留在室外。
一、管道安裝要求
1、管道在安裝前應對設備管口、預埋件、預留孔洞、鋼結構等涉及管道安裝的內容進行復核。
2、管道的坡度應按圖紙的要求進行調整,調整方法可以利用支座達到坡度要求,焊縫應設置在便於檢修、觀察的地方。
3、與傳動設備連接的管道,安裝前內部要處理乾凈,焊接固定管口一般應遠離設備,以避免焊接產生應力對傳動設備安裝精度的影響。
4、管道與機器連接前,應防止強力相對,在自由狀態下檢查法蘭的平行度和同軸度。
5、安全閥應垂直安裝,在投入試運行時,要及時調校安全閥。安全閥的最終調校在系統上進行,開啟和回座壓力要符合設計文件的規定。
6、閥門安裝前,按設計文件核對其型號,並按介質流向確定其安裝方向。當閥門與管道以法蘭或螺紋方式連接時,閥門應在關閉狀態下安裝;如以焊接方式安裝時,閥門不得關閉。
7、機表元件的臨時替代:所有機表元件安裝時,均采用臨時元件替代,等試壓、沖洗、吹掃工作結束後,投料前再正式安裝。
二、玻璃鋼管道及復合管的安裝
① FRP管在施工前,應對外觀和尺寸進行檢查,按出廠合格證進行驗收。
② 管道安裝圖是管道安裝工程的依據,FRP/PVC管的敷設(包括連接形式、座標、標高、坡度、坡向等)支承,FRP/PVC管和設備、管道附件的連接,管道附件的安裝位置、支承等,均應符合設計圖紙,如有變動,必須與設計單位協商解決。
③ 管道安裝,可按管道安裝圖所劃分的管段,從管道的一端依次安裝管道附件,直至另一端,再設支架或支座(必要時在安裝過程中需設臨時支撐)。管道吊裝時,外壁表麵必須采取保護措施,禁止與鋼絲繩直接接觸,以免造成局部受力。
④ FRP管的連接點隻允許在直管部分。對焊連接點與管道支座邊緣的距離,應大於管道的外徑且不小於100mm;承插連接處與管道支座邊緣的距離應大於150mm。
⑤ 管道的連接結構形式有承插式連接、法蘭式連接(焊環活套法蘭連接和復合平焊法蘭連接)、對焊連接三種。此工程中將根據設計文件的具體要求確定安裝方法。
⑥ 從事焊接的安裝工人必須持有焊工合格證,並熟悉FRP/PVC管的粘接劑性能及其安裝方法,並且有熟練的PVC焊接操作能力。
⑦ 管道在承插連接前,首先應清除連接處PVC管內壁污垢,然後將承插頭插入承插座內,承插口不得有歪斜,裂紋等缺陷,達到承插深度後,方可進行PVC焊接。
⑧ 承插部位應采用FRP增強,在增強處均勻塗一層R膠,塗層厚薄均勻,不得漏塗和流淌,再包一層玻璃佈,塗不飽和樹脂,包玻璃佈,反復進行,直至厚度達到要求為止。
⑨ 當承插口安裝不合格需返修時,承插頭和承插座必須重新製作,不得采用已使用過的承插件。
⑩ 法蘭與管道連接時,內外兩麵都必須與管子焊接,法蘭麵與管子軸線傾斜度應小於或等於管子外徑的1/100。法蘭連接應嚴格對中,軸向最大允許偏差不大於2mm,不得用強緊螺栓的方法消除歪斜。擰緊螺栓分兩次進行,第一次均勻對稱地擰一遍,然後再擰緊螺栓。
三、鋼襯膠管的安裝
①在搬運和堆放襯膠管及管件時,應避免強烈振動或碰撞。
②安裝前應檢查襯膠層完好,保持管內清潔。
③襯膠管安裝時,不得施焊,局部加熱,扭曲或敲打。
④對DN≤500的成品管件,安裝前要按單線圖對每管段進行編號,安裝時按單線圖和編號遂段組對安裝,其活口部分如要進行修正應將修正後的管段現場襯膠。
⑤襯膠管應采用軟墊片或半硬墊片,安裝時墊片要放正,必要時可有斜墊片找正。
⑥對DN≥500的管子,管件先按單線圖進行現場預製,預安裝,采用法蘭連接,法蘭麵之間需預留好襯膠層及墊片厚度約為7mm,現場試壓合格後,拆卸進行現場加工襯裡,預安裝後的管道應在管壁上做記號,按圖編號,使襯裡後仍能按原圖紙進行安裝。
⑦現場預製的管道法蘭應內外兩麵焊接,法蘭的內外表麵焊接後必須用角向砂輪機磨光銼平,不得有凹凸不平,氣孔等現象,以免空氣留在孔隙內,使襯膠層因空氣作用老化。
⑧管內襯膠如是反出到法蘭,要求管件在製作時達到法蘭裡口,轉角處應為r=5mm,如采用一般法蘭焊接,則法蘭裡口的焊縫必須加工成r=5mm的圓角。
⑨現場加工的彎管,其彎曲角度應不於90°彎曲半徑不應小於管徑4倍。
⑩鋼襯膠管開三通要做到內壁轉角處的小圓角r=5mm呈光滑狀,采用加熱拉製三通的方法,以符合襯膠要求。
四、卷管加工
① 卷管的同一筒節上的縱向焊縫不宜大於兩道;兩縱縫間距不宜小於200mm。
② 卷管組對時,兩縱縫間距應大於100mm。支管外壁距焊縫不宜小於50mm。
③ 卷管應按規定檢查圓弧度、端麵偏差、平直度等。
④ 焊縫不能雙麵成型的卷管,當公稱直徑大於或等於600mm時,宜在管內進行封底焊。
⑤ 在卷管加工過程中,應防止板材表麵損傷。對有嚴重傷痕的部位必須進行修磨,使其圓滑過渡,且修磨處的壁厚不得小於設計壁厚。
⑥卷管所有焊縫應經煤油滲透試驗合格。
五、管道支、吊架的製作與安裝
① 現場製作的管架嚴格按規范和圖紙進行,並塗漆保護,對拉桿吊架和彈簧吊架的吊耳支撐,應按鋼結構製作標準進行焊接並進行100%的滲透或磁粉探傷。
② 所有管架位置,應在單線圖中標明。
③ 管道安裝時,應及時固定和調整支架,支架位置應準確,安裝應平整牢固,與管子接觸應緊密。
④ 固定支架應按設計文件要求安裝,並應補償器預拉伸之前固定。
⑤ 導向支架或滑動支架的滑動麵應潔凈平整,不得有歪斜和卡澀現象。其安裝位置應從支承麵中心向反方向偏移,偏移量應為位移值的1/2或符合設計文件規定,絕熱層不得妨礙其位移。
⑥ 管道安裝使用臨時支架時,不得與正式支架位置沖突,並有明顯標記。在管道安裝完畢後應予拆除。
⑦ FRP/PVC管道與管架(包括支座)之間不得直接進行粘接或焊接固定。FRP/PVC管道固定管架的管道配合件(管卡、管托或管夾)與管道外壁之間,應墊有厚度不小於3mm的橡膠塊或其他軟墊。
⑧ 管道安裝完畢後,應按設計文件規定逐個核對支架的形式和位置。
六、玻璃鋼管道的試壓沖洗
① 為瞭減少吹掃時增加的臨時管線,節省試壓吹掃時間,提高試壓吹掃合格率,管道試壓、吹掃工作按系統、片區、壓力等級進行,試壓、吹掃前必須編製方案指導施工。
② 管道試壓采用潔凈水,當對連有不銹鋼管道進行試驗和沖洗時,水中的氯離子含量不得超過25×10(25ppm),管道試壓和沖洗程序執行總包商的規定。
③ 壓力試驗時,無關人員不得進入。壓力試驗完畢,不得在管道上進行修補。
④ 壓力試驗前,應具備下列條件:
a.試驗范圍內的管道安裝工程除塗漆、絕熱外,已按設計圖紙全部完成,安裝質量符合有關規定。
b.焊縫和其它待檢部位尚未塗漆和絕熱。
c.管道上的膨脹節已設置瞭臨時約束裝置。
d.試驗用壓力表已經校驗,並在周期內,其精度不得低於1.5級,表的滿刻度值應為被測最大壓力的1.5-2倍,壓力表不得少於兩塊。
e.符合壓力試驗要求的液體或氣體已備齊。
f.按試驗要求,管道已經加固。
g.待試管道與無關系統已用盲板或采取其它措施隔開。
h.待試管道上的安全閥及機表元件等已經拆下或加以隔離。
i.試驗方案已經批準,並進行瞭技術交底。
⑤ 液壓試驗應遵守下列規定:
a.試驗前,註液體時應排盡空氣。
b.試驗時環境溫度不宜低於5℃,當環境溫度低於5℃時,要采取防凍措施。
c.管道試驗壓力為設計壓力的1.5倍。
d.當管道的設計溫度高於試驗溫度時,試驗壓力按下式計算:
Ps=1.5P[σ]1[σ]2
式中 Ps----試驗壓力(表壓)(MPa);
P----設計壓力(表壓)(MPa);
[σ]1----試驗溫度下,管材的許用應力(MPa);
[σ]2----設計溫度下,管材的許用應力(MPa)。
當[σ]1[σ]2大於6.5時,取6.5。
e.當管道與設備作為一個系統進行試驗,管道的試驗壓力等於或小於設備的試驗壓力時,應按管道的試驗壓力進行試驗;當管道試驗壓力大於設備試驗壓力,且設備的試驗壓力不低於管道設計壓力的1.15倍時,經建設單位同意,可按設備的試驗壓力進行試驗。
f.對位差較大的管道,應將試驗介質的靜壓計入試驗壓力中。液體管道的試驗壓力以最高點為準,但最低點的壓力不得超過管道組成件的承受力。
g.液壓試驗壓力應緩慢升壓,待達到試驗壓力後,穩壓10min,再將試驗壓力降至設計壓力。停壓30min,以壓力不降、無滲漏為合格。
h.試驗結束後,應及時拆除盲板、膨脹節限位設施,排盡積液。排液時要防止形成負壓,並不得隨地排放。
i.當試驗過程中發現泄漏時,不得帶壓處理。消除缺陷後,應重新進行試驗。
⑥ 對輸送有毒流體的管道,還必須進行泄漏性試驗,泄漏性試驗介質采用空氣(即進行氣密試驗)。氣密試驗按下列規定進行:
a.氣密試驗壓力為設計壓力。
b.氣密試驗重點檢驗閥門填料函、法蘭或螺紋連接處、放空閥、排氣閥、排水閥等。
c.氣密試驗用塗刷肥皂水或其它發泡劑的方法進行檢查,以不泄漏為合格。
⑦管道在壓力試驗合格後,應按吹洗方案組織管道的吹掃或清洗工作案。

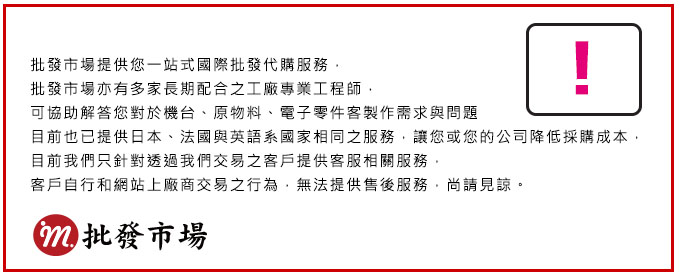
批發市場僅提供代購諮詢服務,商品內容為廠商自行維護,若有發現不實、不合適或不正確內容,再請告知我們,查實即會請廠商修改或立即下架,謝謝。