熱管餘熱鍋爐在黃磷尾氣技術應用
由於黃磷尾氣成分復雜,凈化工藝尚不成熟、凈化工程投資較大,因此大多數企業將其直接放空燃燒。據不完全統計,國內黃磷尾氣總有效利用率不超過30%,其中95%是代替煤做燃料用,用作生產高附加值有機產品的約占5%[2],可見能源浪費嚴重,不符合國傢提倡的發展循環經濟、促進節能減排理念。
將黃磷尾氣燃燒後利用其熱能的方式主要有烘乾焦炭等原材料、燒熱水鍋爐和用於五鈉、六偏等磷酸鹽乾燥、脫水聚合,此前國內尚無將黃磷尾氣用於燒鍋爐製取蒸汽的成功先例。
2黃磷尾氣用於燒蒸汽鍋爐的技術難題
用黃磷尾氣燒鍋爐製取蒸汽的原理類似於燃氣鍋爐,但是其技術難點在於鍋爐設備難以經受黃磷尾氣在燃燒過程中的腐蝕,其原因主要有兩點。
黃磷尾氣經過噴淋水收磷和簡單洗氣後,可以除去大部分的氟、砷、磷等元素,但仍有少量的硫和磷較難除去,這部分硫、磷物質燃燒後生成的酸性氣體會對鍋爐構成低溫腐蝕。在鍋爐煙道尾部,當溫度低於230℃以後,煙氣中的SO3、P2O5等酸性氣體結露後對爐壁形成腐蝕。但爐內燃燒溫度越高,則爐內原子氧的濃度越高[3],將有更多的SO2轉化為SO3,也會增強對設備的腐蝕。
另一方麵尾氣中的部分含磷顆粒在沒有燃燒完全的情況下受爐內定向風力、風速的作用做定向運動,黏附在換熱管壁上繼續燃燒,生成低熔點的磷鐵、碳酸鐵鹽,使保護管壁的氧化膜被破壞,進而受到腐蝕[4]。因此,黃磷尾氣在燃燒過程中會在極短時間內對燃氣設備產生非常嚴重的腐蝕而使設備報廢[5]。
3黃磷尾氣蒸汽鍋爐技術方案及工作原理
經多年的研究和摸索,我公司采用將燃燒和換熱分開進行的鍋爐結構,解決瞭如上所述鍋爐內產生的各種腐蝕難題。
從黃磷電爐出來的尾氣經過電爐三塔收磷、三級水洗塔洗滌,除去其中的大部分灰塵雜質、氟、磷、硫後,輸送至鍋爐燃燒室進行燃燒,在燃燒器內形成的高溫煙氣約為1500℃;由配風機鼓入冷風,對高溫煙氣進行稀釋降溫至約550℃,再進入鍋爐蒸發器與列管進行換熱;蒸發器本體與汽包通過上下循環管道組成蒸汽發生器,軟水在蒸發器本體內吸收熱量生成汽水混合物,經上循環管進入蒸汽聚集器進行汽水分離,分離出來的飽和蒸汽通過汽包的蒸汽出口向外輸送供生產使用;未汽化的軟水經下循環管返回蒸發器本體進行再吸熱蒸發;高溫煙氣的熱量在蒸發器內釋放後,溫度降至250℃左右,再由引風機抽出。
4 黃磷尾氣蒸汽鍋爐結構特點
4.1 解決瞭高溫煙氣對鍋爐設備的腐蝕難題
該裝置采用將燃燒和換熱分開的方式設計鍋爐結構,是解決黃磷尾氣鍋爐腐蝕的關鍵。首先避免瞭高溫火焰對鍋爐設備的直接沖刷;其次,尾氣燃燒完全,不會有含單質磷的顆粒隨煙氣附著在列管燃燒構成腐蝕;第三,采用密封板將高溫煙氣與軟水隔離開,保證瞭換熱列管上端與汽和水接觸的管道外壁麵不與煙氣接觸,防止腐蝕到蒸汽發生器裝置主體;第四,選取鍋爐裝置的運行溫度為550~250℃,提高瞭鍋爐的運行穩定性,還可以降低爐內煙氣中原子氧的濃度,從而降低SO2氧化生成SO3的轉化率,也降低瞭煙氣的腐蝕性。
4.2 獨特設計,延長設備使用壽命
鍋爐蒸發器部分采用高溫和低溫兩段串聯、中間用煙氣通道隔開的型式,每個蒸發器的出入口煙氣溫度差不會超過150℃,設備受的熱應力大大降低。
考慮熱管在工作溫度極限值時運行的穩定性,通過配入過量的空氣對煙氣進行稀釋,使煙氣溫度降低至550℃左右再與列管進行換熱以避免設備運行溫度過高。
在燃燒室配有火焰監測裝置,可對斷氣、熄火進行監控保護,防止系統非正常燃燒造成危險;配備有遠距離液位自動補水裝置,蒸發器內軟水的液麵可以控製在恒定位置;選用氣動調節閥控製煤氣流量,采用瞭PLC自動連鎖控製,並用光柱式液位計醒目表征鍋爐中水的液麵位置,保證瞭鍋爐運行的安全性。
5 黃磷尾氣蒸汽鍋爐運行情況
根據上述技術方案,我們在興發集團某化工園區開發建設瞭一臺套RZQ-B41型號的黃磷尾氣蒸汽鍋爐,鍋爐設計生產能力為6T/h、鍋爐壓力0.8MPa。運行以來,各項技術指標均達到設計能力,能夠為園區內的黃磷電爐等裝置穩定提供蒸汽,完全代替瞭原有的燃煤鍋爐。裝置運行半年以後,我們打開鍋爐蒸發器對爐內腐蝕情況進行瞭檢查,發現僅在鍋爐尾部處的換熱管翅片上出現瞭輕微的腐蝕斑,其他部位的列管和設備未被腐蝕。可見,整個鍋爐運行狀況和耐腐蝕情況比較好,預計可以繼續穩定運行。
裝置運行後,年可節約燃煤1.68萬餘噸,合經濟效益約336餘萬元,並減少瞭二氧化硫、二氧化碳等污染氣體的排放,具有非常好的社會經濟環境效益。
雖然將黃磷尾氣用來燃燒製取蒸汽的利用價值沒有生產碳一化學品的附加值高,但是在黃磷尾氣凈化工藝技術還沒實現工業化之前,該技術提供的途徑在目前來看無疑是進行節能減排的最好選擇,具有很廣闊的推廣前景。

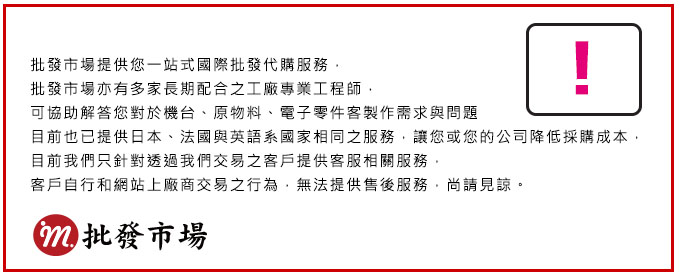
批發市場僅提供代購諮詢服務,商品內容為廠商自行維護,若有發現不實、不合適或不正確內容,再請告知我們,查實即會請廠商修改或立即下架,謝謝。