ng>AISP—E型鋁離子濃度穩定裝置ng>是鋁材生產中硫酸陽極氧化對氧 化液進行全自動處理的設備.(AISP—E型是Aluminium Ion StabiLization Plant E型設計的縮寫)在國外稱為硫酸回收精制裝置或鋁離子滲析器。本產品是消化吸收國外現代最新技術結合我國具體情況,經過第五次改進采用原裝進口的關鍵材料及器件制成。產品完全達到國際先進水平,價格僅為進口產品的50%以下。本設備是鋁材生產中降低產品成本,提高鋁材質量,減小環境污染的必備設備。本產品采用PLC(可編程控制器)結合人機介麵進行程序控制,使操作更直觀,工作更可靠。 ng>氧化工藝參數對氧化膜質量的影響ng> ng>1、硫酸濃度 ng>改變硫酸濃度對氧化膜的阻擋層厚度、電解液的導電性和對氧化膜 的溶解作用、氧化膜的耐蝕性和耐磨性以及後道處理的封孔質量都將產生一定的影 響。ng> ng> ng>2、槽液溫度 ng>在陽極氧化的過程中,部份的電能會轉化為熱能。隨著槽液溫度 的升高,膜質量與金屬損失比明顯減小,而且膜的外層硬度較低,在大氣條件下 這種膜會出現“粉化”現象。 ng>3、氧化電壓 ng>陽極氧化的氧化電壓決定氧化膜的孔徑大小,低壓生成的膜孔徑 小、孔數多,而高壓使膜孔徑大,但數量少。在恒定電壓下,電流密度會隨著氧化時 間的延長而下降,電流密度也隨槽液的溫度、濃度和鋁離子含量變化而變化。 ng>4、氧化電流密度 ng>氧化電流密度與生產效率有直接的關系。當采用較高的氧化 電流密度時,得到的預定厚度氧化膜所需時間可以縮短,生產效率高,但電源的容量 要大,此外氧化電流密度過高,使膜厚波動大,還易引起工件“燒傷”。 ng>5、槽液均勻性ng> ng>6、氧化時間 ng>陽極氧化的時間選擇,必須根據硫酸的濃度、槽液溫度、電流密 度、氧化鋁工件對氧化膜厚和性能的要求來決定。 ng>硫酸溶液中鋁離子的來源ng> 在我國鋁材生產中絕大多數采用硫酸陽極氧化工藝(硫酸濃度150~180g/L,鋁離子12~18g/L),在氧化生產中有約1/3形成氧化膜的鋁被硫酸溶液重新溶解使得槽液鋁含量不斷上升,陽極氧化30分鐘時每噸型材溶鋁量約為3.84Kg(每480m²為一噸計算)。 ng>硫酸溶液中鋁離子濃度的影響ng> 1.在設定氧化電壓下,電流密度隨鋁離子含量的升高而減小(如下圖),氧化膜厚度不均,欲達同一氧化膜厚度須提高電壓,造成電能損耗上升,過高電壓還可能造成氧化膜擊穿,最終使工件燒傷。對於電著色鋁材,鋁離子不穩定造成色差甚至著色困難。 
ng> ng>2.率離子濃度對氧化膜厚度、耐蝕性、耐磨性的影響  3、鋁離子濃度過高,在鋁材表麵產生不溶性的鋁鹽沉積於鋁材、槽壁和熱交換器上,影響產品外觀,熱交換效率降低,甚至會堵塞熱交換器,液溫上升,增加冷凍能耗。 4、過去一般采用定期排放部分槽液的方法降低鋁離子,既影響生產又對生產操作和鋁材質量造成困擾,對環境造成污染和破壞。ng>AISP-E鋁離子穩定裝置的工作原理:ng>利用酸泵將氧化槽液泵入分離罐內,由於分離罐內裝有進口特殊分離材料,快速高效地將硫酸與鋁離子分離,將鋁離子排出溶液之外,將硫酸送回氧化槽中繼續使用,從而使生產中不斷產生的鋁離子排出槽液之外,達到槽液中的鋁離子濃度穩定在一定工藝范圍之內目的,並能凈化槽液中有機物等雜物。長期運行無需更換槽液。其工作原理參見系統原理圖。運行時分為除鋁、回酸、預處理三個基本過程。 ng>除鋁:ng>定量的槽液由儲酸塔泵出,經活性炭過濾塔過濾後再經樹脂塔吸附遊離硫酸,最後由排廢口流入污水處理池。 ng>回酸:ng>與除鋁等量的水或純水由儲水塔泵出,經樹脂帶出樹脂吸附的硫酸,最後由回酸口流回氧化集液槽內。 ng>預處理:ng>水或純水由儲水塔泵出,對活性炭過濾塔進行定時清洗後排廢口排出。 正常使用進時,除鋁和回酸過程交替循環進行,每循環50次左右,對設備進行一次預處理,以清除活性炭吸附的雜質,恢復活性炭的過濾功能。 使用鋁離子濃度穩定裝置可獲得的ng>效益ng>: 1. 使鋁材氧化膜厚度及品質穩定,也為穩定型材著色工藝提供良好的基礎。 2. 氧化電耗減小。 3. 減小冷凍機能耗。 4. 減小換熱器阻塞和提高換熱效果。 5. 設備全自動運行,保持氧化槽液麵平衡,幾乎無需人員操作。 6. 在去除氧化槽液中的鋁離子時回收槽液中的硫酸可達90%,因此大量減少廢水設備 的處理負荷。 ng>效益分析:ng> 1.硫酸損耗計算:日產20噸,槽液量150M3,AL3+(14~18)g/L,硫酸180g/L 以氧化時間30分鐘時每噸型材溶鋁量約為3.84Kg(每480m2為一噸計算) 日產鋁量: 20噸X 3.84Kg/噸=76.8Kg 從14g/L至18g/L的時間:4g/L X 150M3÷76.8Kg/日=7.8天 排一次槽的酸損耗:4g/L X 150M3÷18g/L X 180g/L=6噸 年硫酸損耗:300天/年÷7.8天 X 6噸=230.8噸/年 使用鋁離子濃度穩定裝置:排鋁100Kg/24小時計算 每天開機:76.8Kg/天÷(110Kg/天÷24小時)=16.7小時 處理槽液量:1.5M3/小時 X 16.7小時/天=25M3/天 設備水量年損耗:16.7小時 X 1.5 M3/H X 300天=7515M3 設備電量年損耗:16.7小時 X 2KW/h X 300天=10020KW.h 年硫酸損耗:25M3/天 X 180g/L X 10% X 300天=135噸(10%為設備損耗率) 使用設備前後節省硫酸:230.8噸-135噸=94.8噸 2. 使用本設備後處理廢水化學品用量節省: H2SO4+2NaOH---Na2SO4+H2O 94.8噸H2SO4需要NaOH約77噸! 3. 電量損耗分析:鋁離子從14g/L至18 g/L工作電壓約升高0.4v(在氧化電流12000A 的條件下) 每年每臺電源電量損耗:0.4V X 12000A÷0.85 X 24小時 X 300 天 =40658.8KW.h (0.85為功率因數) 以四臺電源為例:4 X 40658.8Kw.h=162635.2 Kw.h 4. 冷凍機年能耗:162635.2KW.h X3600KJ/KW.h X 0.23卡/KJ=13466.2萬大卡 冷凍機總耗電量: 13466.2萬大卡÷ 40萬大卡/時X 120 KW=40399kw.h(以40萬 cal.H,120Kw為例,交換效率不計) 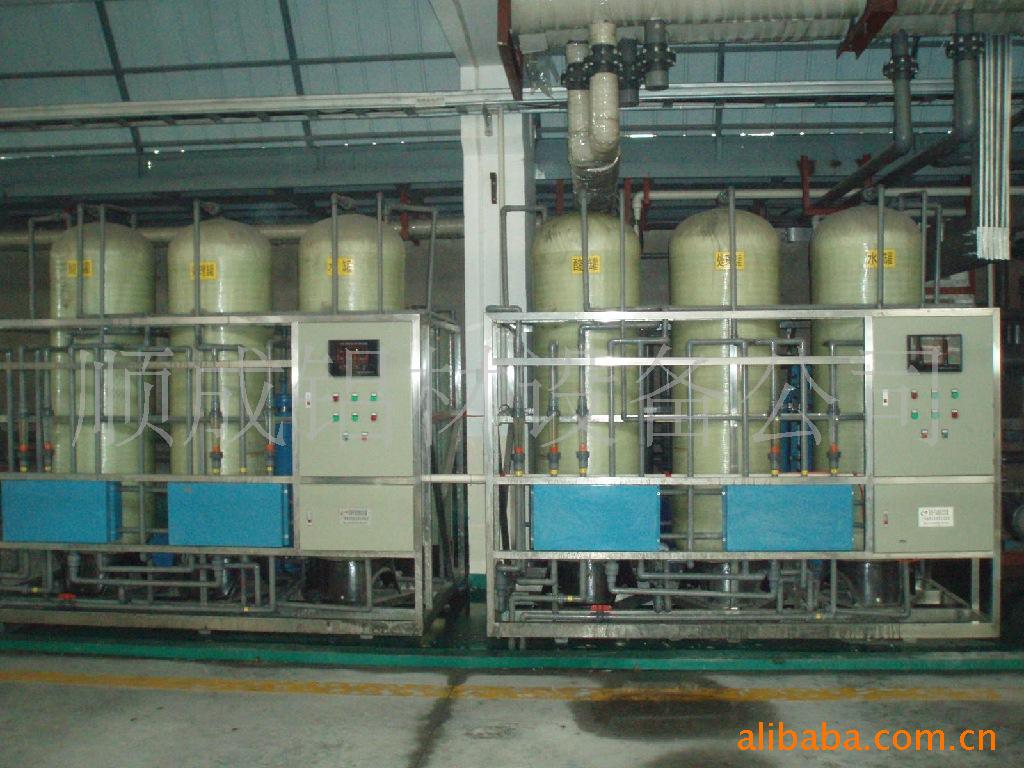
|