品名 | 膠合板 | 樹種 | 0534-2100877 |
產地 | 山東 | 規格 | 各種規格可定做 |
等級 | 優等 | 含水率 | 0534-2100877 |
表觀密度 | 0534-2100877 | 抗彎強度 | 0534-2100877 |
特殊功能 | 耐磨 |
主要產品有S系列手動泵, 四柱壓力機、腳踏油泵、彎管機、快速接頭、液壓泵、液壓缸、D系列電動泵系列、汽油機泵,各種超高壓集成塊、單向閥、分流閥、拉拴器、LL及CL系列超高壓工具,油缸液壓泵;液壓缸;油缸;千斤頂;工具缸;地下頂管;非開挖設備;電動泵;柱塞泵;壓力機;液壓系統;油頂;液壓機具;拉拴器;液壓三抓卸輪器;腳踏液壓泵;液壓泵站;液壓縮管機;液壓彎管機;液壓拉管機;,並承接,設計生產各種需求的液壓系統及執行工具,膠管總成。
其產品特點體積小、重量輕、結構緊湊、操作簡單,也可直接對壓力容器進行壓力測試。配備常用工具可以進行起重、彎曲、校直、擠壓、剪切、鉚焊、頂升、拉伸、拆裝、沖孔、建築鋼筋、擠壓連接、橋樑、工程機構等各種作業。
液壓機
液壓機
液壓機是一種以液體為工作介質,根據帕斯卡原理製成的用於傳遞能量以實現各種工藝的機器。液壓機一般由本機(主機)、動力系統及液壓控制系統三部分組成。
用途
液壓機是一種以液體為工作介質,用來傳遞能量以實現各種工藝的機器。液壓機除用於鍛壓成形外,也可用於矯正、壓裝、打包、壓塊和壓板等。液壓機包括水壓機和油壓機。以水基液體為工作介質的稱為水壓機,以油為工作介質的稱為油壓機。液壓機的規格一般用公稱工作力(千牛)或公稱噸位(噸)表示。鍛造用液壓機多是水壓機,噸位較高。為減小設備尺寸,大型鍛造水壓機常用較高壓強(35兆帕左右),有時也採用 100兆帕以上的超高壓。其他用途的液壓機一般採用 6~25兆帕的工作壓強。油壓機的噸位比水壓機低。
工作原理
液壓機的工作原理。大、小柱塞的面積分別為S2、S1,柱塞上的作
用力分別為F2、F1。根據帕斯卡原理,液體壓強各處相等,即F2/S2=F1/S1=p;F2=F1(S2/S1)。表示液壓的增益作用,與機械增益一樣,力增大了,但功不增益,因此大柱塞的運動距離是小柱塞運動距離的S1/S2倍。
工作介質
液壓機所用的工作介質的作用不僅是傳遞壓強,而且保證機器工作部件工作靈敏、可靠、壽命長和洩漏少。液壓機對工作介質的基本要求是:1有適宜的流動性和低的可壓縮性,以提高傳動的效率;2能防銹蝕;3有好的潤滑性能;4易於密封;5性能穩定,長期工作而不變質。液壓機最初用水作為工作介質,以後改用在水中加入少量乳化油而成的乳化液,以增加潤滑性和減少銹蝕。19世紀後期出現了以礦物油為工作介質的油壓機。油有良好的潤滑性、防腐蝕性和適度的粘性,有利於改善液壓機的性能。20世紀下半葉出現了新型的水基乳化液,其乳化形態是“油包水”,而不是原來的“水包油”。“油包水”乳化液的外相為油,它的潤滑性和防蝕性接近油,且含油量很少,不易燃燒。但水基乳化液價格較貴,限制了它的推廣。
結構
一、驅動系統
液壓機的驅動系統主要有泵直接驅動和泵-蓄能器驅動兩種型式。泵直接驅動 這種驅動
驅動系統
系統的泵向液壓缸提供高壓工作液體,配流閥用來改變供液方向,溢流閥用來調節系統的限定壓強,同時起安全溢流作用。這種驅動系統環節少,結構簡單,壓強能按所需的工作力自動增減,減少了電能消耗,但須由液壓機的最大工作力和最高工作速度來決定泵及其驅動電機的容量。這種型式的驅動系統多用於中小型液壓機,也有用泵直接驅動的大型(如120000千牛)自由鍛造水壓機。
泵-蓄能器驅動 在這種驅動系統中有一個或一組蓄能器。當泵所供給的高壓工作液有餘量時,由蓄能器儲存;而當供給量不足於需要時,便由蓄能器補充供給。採用這種系統可以按高壓工作液的平均用量選用泵和電動機的容量,但因為工作液的壓強是恆定的,電能消耗量較大,並且系統的環節多,結構比較複雜。這種驅動系統多用於大型液壓機,或者用一套驅動系統驅動數台液壓機。
二、結構型式
按作用力的方向區分,液壓機有立式和臥式兩種。多數液壓機為立式,擠壓用液
結構
壓機則多用臥式。按結構型式分,液壓機有雙柱、四柱、八柱、焊接框架和多層鋼帶纏繞框架等型式,中、小型立式液壓機還有用C型架式的。C型架式液壓機三面敞開,操作方便,但剛性差。沖壓用的焊接框架式液壓機剛性好,前後敞開,但左右封閉。在上傳動的立式四柱自由鍛造液壓機中,油缸固定在上梁中,柱塞與活動橫樑剛性連接,活動橫樑由立柱導向,在工作液的壓強作用下上下移動。橫樑上有可以前後移動的工作台。在活動橫樑下和工作檯面上分別安裝上砧和下砧。工作力由上、下橫樑和立柱組成的框架承受。採用泵-蓄能器驅動的大、中型的自由鍛水壓機常採用三個工作缸,以得到三級工作力。工作缸外還設有向上施加力的平衡缸和回程缸。
分類
按結構形式現主要分為:四柱式、單柱式(C型)、臥式、立式框架等。
按用途主要分為金屬成型、折彎、拉伸、沖裁、粉末(
四柱液壓機
金屬,非金屬)成型、壓裝、擠壓等。
熱鍛液壓機
大型鍛造液壓機是能夠完成各種自由鍛造工藝的鍛造設備,是鍛造行業使用最廣泛的設備之一。目前有800T、1600T、2000T、2500T、3150T、4000T、5000T等系列規格的鍛造液壓機。
四柱液壓機
該液壓機適用於可塑性材料的壓制工藝。如粉末製品成型、塑料製品成型、冷(熱)擠壓金屬成型、薄板拉伸以及橫壓、彎壓、翻透、校正等工藝。
液壓成形技術
一、優勢
與傳統的沖壓工藝相比,液壓成形工藝在減輕重量、減少零件數量和模具數量、提高剛度與強度、降低生產成本等方面具有明顯的技術和經濟優勢,在工業領域尤其是汽車工業中得到了越來越多的應用。
在汽車工業及航空、航天等領域,減輕結構質量以節約運行中的能量是人們長期追求的目標,也是先進製造技術發展的趨勢之一。液壓成形(hydroforming)就是為實現結構輕量化的一種先進製造技術。
液壓成形也被稱為“內高壓成形”,它的基本原理是以管材作為坯料,在管材內部施加超高壓液體同時,對管坯的兩端施加軸向推力,進行補料。在兩種外力的共同作用下,管坯材料發生塑性變形,並最終與模具型腔內壁貼合,得到形狀與精度均符合技術要求的中空零件。
二、優點
對於空心變截面結構件,傳統的製造工藝是先沖壓成形兩個半片,然後再焊接成整體,而液壓成形則可以一次整體成形沿構件截面有變化的空心結構件。與沖壓焊接工藝相比,液壓成形技術和工藝有以下主要優點:
□ 減輕質量,節約材料。對於汽車發動機托架、散熱器支架等典型零件,液壓成形件比沖壓件減輕20%~40%;對於空心階梯軸類零件,可以減輕40%~50%的重量。
□ 減少零件和模具數量,降低模具費用。液壓成形件通常只需要1套模具,而沖壓件大多需要多套模具。液壓成形的發動機托架零件由6個減少到1個,散熱器支架零件由17個減少到10個。
□ 可減少後續機械加工和組裝的焊接量。以散熱器支架為例,散熱面積增加43%,焊點由174個減少到20個,工序由13道減少到6道,生產率提高66%。
□ 提高強度與剛度,尤其是疲勞強度,如液壓成形的散熱器支架,其剛度在垂直方向可提高39%,水平方向可提高50%。
□ 降低生產成本。根據對已應用液壓成形零件的統計分析,液壓成形件的生產成本比沖壓件平均降低15%~20%,模具費用降低20%~30%。
液壓成形工藝應用
一、範圍
液壓成形工藝在汽車、航空、航天和管道等行業有著廣泛的應用,主要適用於:沿構件軸線變化的圓形、矩形或異型截面空心結構件,如汽車的排氣系統異型管件;非圓截面空心框架,如發動機托架、儀表盤支架、車身框架(約占汽車質量的11%~15%);空心軸類件和複雜管件等。圖2即為液壓成形工藝應用於汽車工業中所製造出的一些典型零件。
液壓成形工藝的適用材料包括碳鋼、不銹鋼、鋁合金、銅合金及鎳合金等,原則上適用於冷成形的材料均適用於液壓成形工藝。
二、特點
液壓機技術特點:
●本系列液壓機適合於可塑性材料的壓制工藝,如沖壓、彎曲、翻邊薄拉伸等
●也可以從事校正、壓裝、塑料製品及粉末製品的壓製成型。
選裝配置
●沖裁緩衝裝置
●PLC觸摸屏控制分流
●快速行程充液裝置
●20T--1000T可特殊訂貨
●下頂缸選裝
液壓機技術參考資料
公稱壓力 | kn | 3150 |
液體最大壓力 | mpa | 31 |
滑塊行程 | mm | 400 |
最大開口高度 | mm | 650 |
立柱中心距(左右×前後) | mm | 800×500 |
工作台有效面積(左右×前後) | mm | 700×700 |
工作台外形尺寸(左右×前後) | mm | 1000×700 |
工作台高度 | mm | 680 |
機器佔地面積 | mm | 2150×900 |
機器高度 | mm | 2400 |
電機功率 | kw | 11 |
關於貨運說明:1.貨運發貨不像快遞那麼方便,需要我們委託物流公司發貨,2.一般物流都要3-5天左右,延長1-2天之內是合理時間。買家請不要收到貨之後,說物流費用高或是其他原因(如物流慢)而拒絕收貨、付款。請大家諒解!

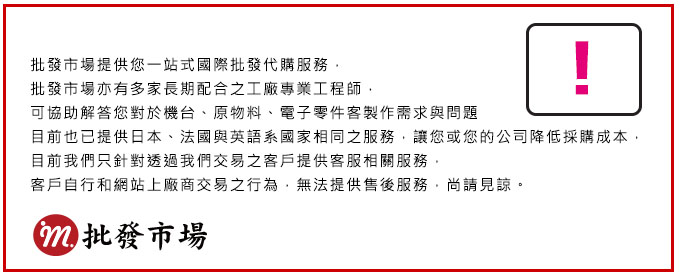
批發市場僅提供代購諮詢服務,商品內容為廠商自行維護,若有發現不實、不合適或不正確內容,再請告知我們,查實即會請廠商修改或立即下架,謝謝。