澆註系統的概述和作用
澆註系統是砂型中引導液態合金流入型腔的通道。生產中常常因澆註系統設計安排不當造成:砂眼、夾砂、粘砂、夾渣、氣孔、鐵豆、抬箱、縮孔、縮松、冷隔、澆不足、變形、裂紋、偏折等鑄造缺陷。此外,澆註系統的好壞還影響造型和清理工作的繁簡,砂型的體積大小和型砂的耗用運輸量,非生產性消耗的液態合金用量等等。所以,澆註系統與獲得優質鑄件,提高生產效率和降低鑄件成本的關系是密切相聯的。因此對澆註系統的設計必須慎重認真。
冷鐵放置計算
為瞭保證厚大部位重要表麵的質量,防止產生縮孔等缺陷,提高導軌硬度,需在導軌處放置外冷鐵激冷[5] 。 冷鐵尺寸=粗大部位尺寸×(0.25~0.4) 該工藝中導軌為粗大部位,應放置冷鐵,根據導軌尺寸得: 冷鐵尺寸=44mm×(0.25~0.4)=11~17mm 取中間尺寸15mm,選取15×40×100mm規格的石墨冷鐵。
澆註系統除導入液態合金這一基本作用外,正確的澆註系統還應具有以下功能和註意事項:
a)使液態合金平穩充滿砂型,不沖擊型壁和砂芯,不產生激濺和渦流,
不卷入氣體,並順利地讓型腔內的空氣和其他氣體排除型外,以防止 金屬過渡氧化及產生砂眼、鐵豆、氣孔等缺陷
b)阻礙夾雜物進入型腔,以免在鑄件上形成渣孔。
c)起一定的補流作用,一般是在內澆道凝固前補給部分液態收縮。 d)讓液態合金以最短的距離,最合宜的時間充滿型腔,並有合適的型內 液麵上升速度,得到輪廓完整清晰的鑄件。
e)充型流股不要正對冷鐵和芯撐,防止降低外冷鐵的激冷效果及表麵溶化,造成鑄件壁變化。
拔模斜度
為瞭在造型和製芯時便於起模而不致損壞砂型和砂芯,應該在模樣或芯盒的出模方向帶有一定的斜度。如果零件本身沒有設計出相應的結構斜度時,就要在鑄型工藝設計時給出拔模斜度。模樣的起模斜度,應不致使鑄件超出尺寸公差。該鑄件高度為525mm,起模斜度可選1:100。
外模設計 所謂外模設計也即形成工件外表麵的木模的設計過程,它主要從以下幾方麵考慮: a) 加工餘量; b) 透門處由芯子帶出還是由外模帶出,若由芯子帶出是否出芯頭及芯頭尺寸; c) 凸臺及牙邊等難撤料部位應采用活塊處理; d) 與外部表麵相關的不鑄出孔不鑄出麵; e) 外表麵上的螺絲窩及拐角等部位芯頭尺寸。
分型負數的選擇 起模後的修型和烘乾會引起砂型變形,致使分型麵凹凸不平,使合型不嚴密。為防止澆註時從分型麵跑火,合型時應在分型麵上放耐火泥條或石棉繩[1] ,這就增高瞭型腔高度。為瞭保證鑄件尺寸符合圖樣尺寸要求,模樣上必須減去相應的高度,減去的值稱為分型負數。 確定分型負數,應該註意下述幾點[2] : a)若模樣分成對稱的上、下兩半,則上、下半模各取分型負數的一半,否則,分型負數放在上半模樣。 b)多箱造型時,每個分型麵都要放分型負數。 c)自硬砂型和濕型一般不放分型負數,但是砂型平麵大於1.5m2時,也放分型負數,其值小於表中的數值。 d)在分型麵上的砂芯間隙不能比分型負數小。
排氣設計
濕砂芯,乾砂芯和自硬砂芯在澆註過程中,其粘合劑及表麵中的有機物要揮發、分解、燃燒(氧化反應)、短時間內放出大量氣體,以及水分蒸發[6] 。如果這些氣體不能及時排出型外,一旦鉆入金屬液體,就很可能留在裡麵而使鑄件產生氣孔。因此,在設計,製造砂芯及下芯,合箱的整個過程中,應十分重視砂芯的排氣。一定要讓澆註時砂芯中產生的氣體能夠及時地從芯頭排出鑄型外。 芯子的排氣一般都是用蠟線或尼龍管做排氣孔引氣,將蠟線或尼龍管埋入砂芯中,在做好砂芯後,尼龍管充當砂芯中排氣孔道。最終從芯頭排出;若芯子沒有出芯頭,則可在芯子與鑄型分芯處,擺放一圈防火泥通過排氣孔引出。
分芯原則
首先,先對芯子的分類做個簡單的瞭解。芯子分三類,即普通芯子(用X1等編號表示),置於砂芯中的NX,及預先粘到砂型上的SX三類。其中NX和SX是在特定情況下才用到的;NX應用在當一個芯子中間有凸臺等難撤料部位時,采用NX處理;SX用在當芯子較小,與砂型直接相接且粘上後不影響其它芯子下芯時,就預先粘到砂型的相應位置上,有定位準確,下芯便捷的優點。 其次,分芯的一般原則: a) 砂芯的填砂麵應寬敞,以便於造芯時填砂,舂砂,安放芯骨,及有利於采取排氣措施。 b) 砂芯在烘乾時的支承麵最好是一個比較大的平麵,以便於放置在平的烘乾板上烘乾。 c) 一個砂芯分成兩半時,應盡量沿著砂型的分型麵分開。這樣可使砂芯的拔模斜度與模樣的 斜度一致,保證鑄件壁厚均勻。 d) 便於下芯合箱,保證鑄件的精度。 e) 鑄件上位置精度要求高的部位,應盡可能用一個砂芯形成。 f) 尺寸過大的砂芯,為瞭方便製芯下芯或者為瞭解決車間起重量不夠的困難,可將大砂芯分 成數個較小的砂芯。
鑄造收縮率
鑄造在凝固和冷卻過程中,體積一般要收縮。金屬在液態和凝固過程中的收縮量以體積的改變量表示,成為體收縮。在固態下的收
縮量常以長度表示,稱為線收縮。由於鑄件的固態收縮將使鑄件各部分尺寸小於模樣原來的尺寸,因此為瞭使鑄件冷卻後的尺寸與
鑄件圖示一致,則需要在模樣或芯盒上加上其收縮的尺寸。加大的這部分尺寸稱為鑄件的收縮量,一般用鑄件收縮率表示。
最小鑄出孔和槽
機械零件上往往有許多孔、槽和臺階,一般來說,應盡可能在鑄造時鑄出[1] 。這樣既可以節約金屬,減少機械加工的工作量,降低成本,又可使鑄件壁厚比較均勻,減少形成縮孔,縮松等鑄件缺陷的傾向。但是,當鑄件上的孔、槽的尺寸太小,而鑄件的壁厚又較厚和金屬壓力頭較高時,反而會使鑄件產生粘砂,造成清鏟和機械加工困難;有的孔、槽,為瞭把它們鑄出,必須采用復雜而且難度較大的工藝措施,而實現這些措施還不如用機械加工的方法製出更為方便和經濟;有時由於孔距要求很精確,鑄出的孔如有偏心,就很難保證加工精度。因此,在確定零件上的孔和槽是否鑄出時,必須既考慮到鑄出這些孔或槽的可能性,又要考慮到鑄出這些孔或槽的必要性和經濟性。
工藝方案的分析和確定
方案一:以立柱導軌背麵為分模麵(樹脂砂造型) 該鑄件的導軌麵為重要麵應放在下箱或側麵,采用方案一將鑄件放在一個砂箱內,從而保證導軌的質量。這樣可以減少錯箱和加工定位尺寸,但是地腳筋板處起模困難需要從工藝上出芯子加以處理。
方案二:以立柱導軌的中心對稱線為分模麵(樹脂砂造型) 該鑄件的導軌麵為重要表麵,應放在下箱或側麵,采用方案二應將其放在沙箱側麵。可以保證導軌的質量,同時避免立柱地腳筋板處出芯子,由外模直接帶出。靠型內定位及模型製做準確度來減少錯箱的傾向。需在澆註系統加以考慮,否則會造成上下導軌在澆註過程中溫度不同從而導致硬度不同。本設計采用方案二。
澆註位置的確定原則
a) 澆註時主要加工表麵,主要工作麵和受力麵應盡量放在底部和側麵,以
防止產生砂眼,氣 孔,夾渣等缺陷。
b) 對於凝固體收縮較大的鑄件合金,應滿足順序凝固的原則,鑄件厚實部 分應盡可能置於上 方,利於冒口補縮。
c) 應有利於砂芯的定位,固定和排氣,盡量避免摽芯和懸臂砂芯。
d)大平麵應置於下部或傾斜位置,以防夾砂等缺陷,有時為瞭方便造型,
可采用“橫做立澆” “平做立澆”的方法。
e) 鑄件的薄壁部分應置於鑄件的底部或側麵,以防澆不到冷隔等缺陷。 f) 在大批量生產中,應使鑄件的飛翅,毛刺最少與易於清除。
g) 要避免厚實鑄件冒口下麵的受力麵產生偏析。 h) 盡量使冒口置於加工
麵上,以減少鑄件清理工作量。
分型麵的確定原則
分型麵是指上半鑄型和下半鑄型的分界麵,它往往也是模樣的分模麵。在確定鑄件分型麵的同時,實際上也確定瞭鑄件在砂箱中的位置(即澆註位置),因此,分型麵的選擇對鑄件的質量和整個生產過程影響很大,是鑄造工藝是否合理的關鍵問題之一。確定分型麵的原則有如下幾條:
a) 盡量將鑄件的全部或大部分放在同一箱內,以減少錯型和不便驗型造
成的尺寸偏差;
b) 盡量將加工定位麵和主要加工麵放在同一箱內。以減少加工定位的尺
寸。
c) 盡量減少分型麵數量,在機器造型中一般采用一個分型麵。
d) 在機器造型中應盡量不使用活塊,必要時用砂芯取代模樣打活動料。 e) 盡量減少砂芯數量。
f) 盡量使分型麵是平麵,必要時也可不做成平麵。
g) 為瞭方便起模,分型麵應在鑄件的最大截麵處,對於較高的鑄件應盡
量使鑄件在一箱內不 宜過高。
h) 在大量生產時,分型麵的選擇應有利於鑄件的整理。
i) 選擇分型麵應考慮到造型的不同。高壓造型與射壓造型相比砂型緊實
度較高。狹小吊砂處 易損壞,故在高壓造型中應避免狹小吊砂。
公司擁有一批優秀的工藝人員 ,砂型鑄造模具,雄厚的技術力量和先進的加工設備 砂型鑄造模具設計,嚴格的品質管理。為客戶提供模具的:設計 開發 工藝等全套方案。
行路致遠,砥礪前行。衡駿機械模具有限公司致力成為與您共贏、共生、共同前行的戰略夥伴,更矢志成為鑄造模最具影響力的企業,與您一起飛躍,共同成功!
公司網址;www.bthjmj.cn

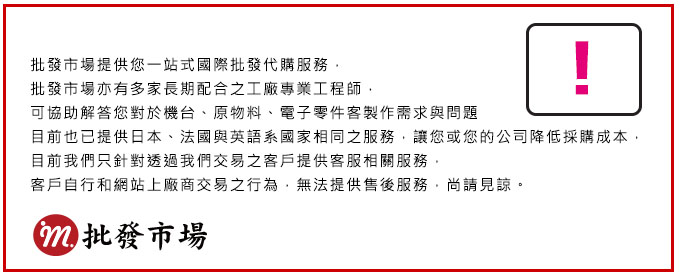
批發市場僅提供代購諮詢服務,商品內容為廠商自行維護,若有發現不實、不合適或不正確內容,再請告知我們,查實即會請廠商修改或立即下架,謝謝。