樣品或現貨:樣品 | 是否標準件:非標準件 | 標準編號:002 |
品牌:三川 | 型號:各種型號 | 材質:高速鋼 |
拉刀類型:圓拉刀 | 適用機床:車床 | 是否進口:否 |
是否塗層:非塗層 | 是否庫存:非庫存 | 是否批發:批發 |
溫嶺市三川工具廠是一傢專業從事拉刀研發、生產、銷售為一體的廠傢,品種有圓拉刀,漸開線拉刀,花鍵拉刀,鍵槽拉刀,螺旋拉刀,小徑定心拉刀,特異成形拉刀等。
我廠自成立以來,本著“以質量求生存,以信譽求發展”為理念,不斷引進新技術,新設備,現有數控高精度設備、檢測機器十多臺套,能生產高精度漸開線拉刀、小徑定心復合齒形漸開線花鍵拉刀、超長螺旋拉刀等各種復雜特形拉刀,並已全麵導入計
算機網絡系統,在產品開發設計、生產制造中,普遍采用CAD計算機輔助設計,CAM計算機輔助制造和自主編寫的拉刀設計專用程序等現代設計手段。 三川工具憑借一支敬業的隊伍,先進的設備,嚴格的管理,優異的性價比,贏得瞭廣大客戶的好評。三川人將繼續發揚“專業、創新、優質、高效”的辦廠宗旨,與廣大新老客戶攜手發展。
圓拉刀是高效加工內孔常用的刀具。本文以筆者在工廠中長期的使用經驗與驗證為依據,對圓拉刀結構上存在的問題提出瞭改進意見,同時還對拉孔表麵質量差、拉孔精度低和拉刀壽命低的原因進行瞭詳細分析並逐一列出改進措施。
![]() 圖1 組合式圓拉刀刀齒和切削圖形 |
![]() 圖2 校準齒上磨分屑槽 |
![]() 圖3 常用分屑槽的形狀 |
圓拉刀是高效加工內孔常用的刀具。圓拉刀系刃形復雜刀具,制造精度高,技術要求嚴格,價格昂貴,應合理使用。目前生產上廣泛使用的圓拉刀(以下簡稱拉刀), 大多采用圖1所示組合式的刀齒結構,即在粗切齒和過渡齒上采用不分齒組的輪切式切削方式,其上開有寬的弧形分屑槽;精切齒采用同廓式的切削方式,其上磨出窄分屑槽。經作者在工廠中長期使用與驗證,發現這種拉刀由於結構本身或使用不當等原因,常會造成拉削表麵質量差和刀具使用壽命短等問題。拉刀結構問題及改進為瞭延長拉刀使用壽命,普通拉刀的結構是,在其校準部分上備有3個~7個校準齒,以便在切削齒磨損後逐個遞補為精切齒用。並且,人們通常認為校準齒是不參與切削工作的,故校準齒一般都不磨分屑槽(見圖1)。但在實際生產中,經觀察,拉刀上第一個校準齒是參與切削工作的(因為刃口上有鈍圓,會對孔壁產生較大擠壓作用而使工件產生彈性回復而縮小),它具有精切齒的功能。但因其上不作分屑槽,致使切下的切屑形成環狀,難於卷起,容易堵塞在槽內,使加工表麵質量降低。所以作者建議,在設計和制造拉刀時,除最後1個~2個校準齒外,如圖2所示,在其馀校準齒上亦應前後交錯地磨出圓弧形分屑槽或角度形(V形)窄分屑槽。如圖3所示,分屑槽上兩側刃的後角可按下式計算:
tanαk=tanαf·sin(θ/2)
αf為分屑槽的槽底後角,一般取為5°,見圖3中A-A剖麵;θ分屑槽的槽角。 由上式中可知,當θ=0°時,不論αf磨成多大,αf始終等於0°(即圖3c中所示U形分屑槽的情況)。而當θ角增大時,αf角也將增大。如取αf=5°,θ=60°~90°,則從公式中計算可知,此時側刃上的後角將增大到2.5°~3.5°,從而可使該處切削條件大大改善。 在實際生產中,由於角度形分屑槽的寬度很窄,通常隻有1mm左右,要將砂輪外圓角修成60°~90°角,並要求在拉刀上磨出αf=5°的槽底後角,砂輪直徑不能選大,否則會碰到相鄰刀齒,加之砂輪在尖角處磨損快,需經常修整,這在工藝上是有難度的。所以操作者在制造拉刀時,常用薄片砂輪來磨削,致使磨出的窄分屑槽成瞭U形分屑槽。 由於圓弧形分屑槽的結構合理,其槽角比V形窄分屑槽的槽角大,且槽與切削刃相交處的刀尖角也大,磨削方便,砂輪與被磨工件(拉刀)接觸麵大,磨削時工件不易燒傷,所以為瞭提高拉刀使用壽命,拉刀不但在粗切齒和過渡齒上,而且在精切齒上磨的分屑槽也應盡量采用圓弧形分屑槽。 為使切屑能順利卷曲,分屑槽的槽數需適當增多。經驗表明,其槽數應使切下的切屑寬度以不超過4mm ~5mm為宜。目前一些拉刀設計資料中推薦的V形分屑槽的槽數普遍較少,例如直徑為Φ50mm的圓拉刀,分屑槽的槽數是22個,而國外同尺寸拉刀上的分屑槽數目為40個。同理,輪切式和組合式圓拉刀上的圓弧形分屑槽數目亦要適當增多。
![]() 圖4 拉削缺陷 |
拉孔表麵質量差的原因及改進圖4中所示的鱗刺、環狀波紋和劃痕等缺陷都會直接影響拉孔的表麵質量。 鱗刺 產生鱗刺的主要原因是拉削過程中塑性變形較嚴重。因此,適當增大前角,減小齒升量,選用潤滑性能好的切削液(如含氯的極壓添加劑切削液),以及用預先熱處理來適當提高工件材料硬度(當工件硬度<180HBS時最易產生鱗刺)等方法,都是減少塑性變形和避免鱗刺的有效措施。 環狀波紋 產生波紋的主要原因是拉削力變化較大,切削過程不平穩,產生瞭周期性振動。而引起拉削力變動的原因是:拉刀刀齒交替工作時,同時工作齒數發生變化;齒升量安排不合理,最後幾個精切齒上的齒升量變化太大;刀齒上的刃帶寬度太小或同一刀齒上的刃帶寬窄不等;以及拉刀齒距等距分佈等。找出具體原因後,可采取相應措施。例如,可采用不等齒距的拉刀,或在制造拉刀時齒距不規定公差;適當增加同時參加工作齒數,最好4個~5個,如果太少,可把幾個工件疊在一起拉削。 局部劃痕及“啃刀” 局部劃痕由以下原因造成:積屑瘤、刀齒上有缺口、或容屑條件差;切屑擦傷工件表麵;在拉刀的最後一個精切齒上未開分屑槽。“啃刀”是因拉刀彎曲,使刀齒發生突然移動或擺動造成的。使用較低的切削速度(<2m/min)來抑制積屑瘤的產生,防止切削刃刃麵上的制造缺陷和損傷,及時清除容屑槽中的積屑,重磨前刀麵時須保持原有容屑槽的形狀,拉刀使用完畢必須懸掛以免拉刀因自重而產生彎曲等都是防止劃痕及“啃刀”的有效措施。 擠壓亮點 擠壓亮點是由刀齒後刀麵與已加工表麵之間產生較強烈的擠壓摩擦,或因工件材料硬度過高而造成的。因此,可采取適當增大後角;減小校準齒上刃帶寬度(可減至0.2mm ~0.3mm);選用合適的切削液;應用熱處理方法降低工件材料硬度(當硬度>240HBS時);或把前角適當減小,以增加刃口強度,防止崩刃等均可有效減少工件表麵產生擠壓亮點與劃傷。 拉孔精度低的原因及改進 拉後孔徑擴大或縮小 由於積屑瘤的影響和磨刀時產生的毛刺,拉刀制造時產生的切削刃位置偏差和軸線直線度偏差,以及拉刀和工件預制孔不同心等原因,通常拉後孔徑將會擴大。但在拉削薄壁工件或軔性大的工件材料時,由於拉後工件會產生彈性回復而使孔徑縮小,確定拉刀校準齒尺寸時須考慮拉後孔徑的擴大量或收縮量,其值應通過試驗確定,一般在0.01mm ~0.02mm范圍內。 使用拉刀時,還可通過適當降低切削速度、采用冷卻性能好的切削液,防止積屑瘤的產生以免孔徑擴大。防止孔徑縮小,可采用增大前角、保持刃口鋒利、以及選用合適的切削液等方法。例如,用拉刀拉削40Cr和45鋼工件,當用乳化液孔徑尺寸變小時可改用硫化油拉削。這是因為乳化液是一種水基切削液,水的導熱性好,故刀具的熱膨脹小;乳化液的潤滑性比油類切削液差,所以刀具對工件的擠壓作用也大,加工後工件的回彈量也就增加,因而孔徑尺寸減小。利用上述規律,實際生產中就可通過改變切削液的種類和成份來控制實際加工的尺寸,以滿足拉孔精度和質量的要求。 拉後孔形產生偏差 當工件孔壁沿軸線方向上厚度在全長上不均勻時,拉後孔形將會發生變化。如工件兩端為薄壁,拉後工件孔呈“腰鼓形”;工件中間部分為薄壁,拉後工件孔呈“喇叭口”形。因此,當工件壁厚不均勻且厚薄相差太大時,不宜采用拉削。
![]() 圖5 容屑槽的有效麵積與切削層截麵積 |
拉刀壽命低的原因及改進 拉刀容屑空間不足 拉刀屬於封閉式切削的刀具,如容屑空間不夠,切屑將堵塞在容屑槽內,而使拉削力急增,導致刀齒損壞或拉刀折斷。為此,使用外購拉刀拉削時,應先核算拉刀的容屑系數K。如圖5所示,須使容屑槽的有效麵積大於切削層截麵積,即 K=(πh2/4)/(L0hD)>1h為容屑槽的深度;L0為拉削長度;hD為切削層厚度,組合式拉刀上hD=2fz,見圖1,式中f2為齒升量;K為容屑系數,它的大小與被加工材料和齒升量有關,通常可取K=2~3.5,加工鑄件和齒升量大時K取小值。 刀具幾何參數不當 拉刀前角選用不當,後角太小或刃帶過寬,精切齒上磨的分屑槽為U形槽,切削條件差,刀齒磨損快,嚴重時會使拉刀卡住在工件孔中,使拉刀折斷。拉刀前角通常可取5°~18°,拉塑性材料時可取大值,拉脆性材料時取小值。拉刀後角,切削齒上可取3°±30°,校準齒上可取1°±30°。刃帶寬度通常粗切齒和過渡齒上為<0.2mm,精切齒為0.3mm,校準齒為0.5mm~0.6mm。此外,在精切齒上應磨圓弧形分屑槽或角度形(V形)分屑槽。 齒升量不當 如刀齒上的齒升量過大或不均勻,或個別刀齒上的齒升量過大,使切削力過大或產生顫動,而使刀齒損壞或拉刀折斷。為此,須控制拉刀每個刀齒上的齒升量,當個別刀齒上有損傷、缺口或崩刃時,應將該刀齒磨去,再把其齒升量均勻分攤到其他各個刀齒上。 拉刀刃磨退火 重磨拉刀時不能進刀太快,吃刀過大,以免產生刃口處過熱退火和燒傷等現象,而使刀齒磨損加快和拉刀壽命降低。所以,重磨拉刀時必須精細操作。 工件預制孔尺寸不當及拉削長度過長 工件預制孔直徑偏小,當拉刀前導部強行通過時,容易使拉刀卡住而折斷;或當工件預制孔直徑過大,造成孔的偏移而使拉刀折斷。為此,拉削時必須選用合適的預制孔尺寸,一般拉刀前導部直徑尺寸等於工件預制孔的基本尺寸,公差帶按f7。此外,被拉工件的拉削長度也不能超出拉刀設計時規定的長度,以免同時參加工作齒數增多,切削力過大而使刀齒損壞或拉刀折斷。一般拉削長度都列印在拉刀的頸部上。 工件定位不良 如工件基準端麵與預制孔的垂直度差,夾具支承麵處有切屑,拉刀產生下垂,拉削時拉刀相對工件歪斜等,都會使刀齒上負荷不均勻,造成很大彎曲而使拉刀折斷。為此,須控制預制孔中心線與工件基準端麵的垂直度為0.02~0.05mm/100mm;定位基準端麵應盡可能大,不應有中凸,表麵粗糙度Ra<3.2μm;或采用浮動支承的拉床夾具;對長而重的拉刀,還可使用後托架支承拉刀。
![]() 圖6 拉刀尾端裝硬質合金擠壓環 |
工件材質不均勻與硬度過高 工件材質不均勻,其內有硬質點或材料硬度過高(>280HBS時),表麵有氧化皮等都會使刀具壽命降低。所以,拉前須檢驗工件材質,如材料硬度過高可采用熱處理方法適當降低;或選用W2Mo9Cr4VCo8(M42)、W6Mo5Cr4V2Al等硬度和耐磨性能均較高的高性能高速工具鋼來制造拉刀,國外還有用粉末冶金高速鋼(PM HSS)制造的拉刀;也可在拉刀刀齒表麵上塗一薄層耐磨的TiN;或在拉刀尾端裝一可更換的硬質合金擠壓環,如圖6所示。 拉刀磨損過度 為防止拉刀磨損過度,以免切削力過大而使刀齒損壞,故須控制拉刀刀齒後刀麵上的磨損量,通常不應超過0.2mm~0.3mm,工廠中常以達到上述磨損量時所拉出的工件數來加以控制。 拉床功率不足,剛性差 拉床功率不足,剛性差,引起拉削時振動而使刀齒崩刃或折斷,可改用剛性好和功率足的拉床拉削。 拉削速度不當 如拉削速度過高,切削溫度高,則拉刀壽命將會降低。因而,對於用W6Mo5Cr4V2等通用型高速鋼制造的拉刀,粗拉切削速度一般為3~7m/min, 精拉切削速度一般為1~3m/min;工件材料強度、硬度較高時,拉削速度應取小值。 切削液種類或澆註方式不當 切削液種類與澆註方式不但影響拉刀壽命,而且對加工精度和表麵粗糙度均有影響。加工鋼件孔時,可用濃度為10%~20%乳化液或極壓乳化液,也可用硫化油或復合油。拉鑄件孔時可以乾切削,但最好用普通乳化液或煤油。加工鋼件時如用硫化油,可使拉刀壽命提高。切削液供應要充足,在拉刀進入工件孔前和剛從工件孔中拉出時都應供給切削液,供應量一般不應少於5~15L/min。 此外,正確使用和保管拉刀對拉刀壽命也有影響。在每一個工件拉削之後,都應用銅絲刷將粘附在刃麵上的切屑清除乾凈。如用銅絲刷清除不掉時,可用油石輕輕擦去。但絕不可用鋼絲刷或棉紗。同時拉刀在制造、運輸和保管與使用過程中,不可碰傷刀齒和刃口。拉刀的修復拉刀的價格很貴,為瞭延長其壽命,所以拉刀經多次重磨之後,直徑變小將要報廢時常加以修復使用。這時可在車床上用帶負前角的硬質合金工具逐齒擠壓刀齒前刀麵。擠壓後直經可增大0.01mm~0.02mm,然後再研磨,使其達到規定尺寸。
溫嶺市三川工具廠是一傢專業從事拉刀研發、生產、銷售為一體的廠傢,品種有圓拉刀,漸開線拉刀,花鍵拉刀,鍵槽拉刀,螺旋拉刀,小徑定心拉刀,特異成形拉刀等。
我廠自成立以來,本著“以質量求生存,以信譽求發展”為理念,不斷引進新技術,新設備,現有數控高精度設備、檢測機器十多臺套,能生產高精度漸開線拉刀、小徑定心復合齒形漸開線花鍵拉刀、超長螺旋拉刀等各種復雜特形拉刀,並已全麵導入計
算機網絡系統,在產品開發設計、生產制造中,普遍采用CAD計算機輔助設計,CAM計算機輔助制造和自主編寫的拉刀設計專用程序等現代設計手段。 隆盛工具憑借一支敬業的隊伍,先進的設備,嚴格的管理,優異的性價比,贏得瞭廣大客戶的好評。隆盛人將繼續發揚“專業、創新、優質、高效”的辦廠宗旨,與廣大新老客戶攜手發展。
圓拉刀是高效加工內孔常用的刀具。本文以筆者在工廠中長期的使用經驗與驗證為依據,對圓拉刀結構上存在的問題提出瞭改進意見,同時還對拉孔表麵質量差、拉孔精度低和拉刀壽命低的原因進行瞭詳細分析並逐一列出改進措施。
![]() 圖1 組合式圓拉刀刀齒和切削圖形 |
![]() 圖2 校準齒上磨分屑槽 |
![]() 圖3 常用分屑槽的形狀 |
圓拉刀是高效加工內孔常用的刀具。圓拉刀系刃形復雜刀具,制造精度高,技術要求嚴格,價格昂貴,應合理使用。目前生產上廣泛使用的圓拉刀(以下簡稱拉刀), 大多采用圖1所示組合式的刀齒結構,即在粗切齒和過渡齒上采用不分齒組的輪切式切削方式,其上開有寬的弧形分屑槽;精切齒采用同廓式的切削方式,其上磨出窄分屑槽。經作者在工廠中長期使用與驗證,發現這種拉刀由於結構本身或使用不當等原因,常會造成拉削表麵質量差和刀具使用壽命短等問題。拉刀結構問題及改進為瞭延長拉刀使用壽命,普通拉刀的結構是,在其校準部分上備有3個~7個校準齒,以便在切削齒磨損後逐個遞補為精切齒用。並且,人們通常認為校準齒是不參與切削工作的,故校準齒一般都不磨分屑槽(見圖1)。但在實際生產中,經觀察,拉刀上第一個校準齒是參與切削工作的(因為刃口上有鈍圓,會對孔壁產生較大擠壓作用而使工件產生彈性回復而縮小),它具有精切齒的功能。但因其上不作分屑槽,致使切下的切屑形成環狀,難於卷起,容易堵塞在槽內,使加工表麵質量降低。所以作者建議,在設計和制造拉刀時,除最後1個~2個校準齒外,如圖2所示,在其馀校準齒上亦應前後交錯地磨出圓弧形分屑槽或角度形(V形)窄分屑槽。如圖3所示,分屑槽上兩側刃的後角可按下式計算:
tanαk=tanαf·sin(θ/2)
αf為分屑槽的槽底後角,一般取為5°,見圖3中A-A剖麵;θ分屑槽的槽角。 由上式中可知,當θ=0°時,不論αf磨成多大,αf始終等於0°(即圖3c中所示U形分屑槽的情況)。而當θ角增大時,αf角也將增大。如取αf=5°,θ=60°~90°,則從公式中計算可知,此時側刃上的後角將增大到2.5°~3.5°,從而可使該處切削條件大大改善。 在實際生產中,由於角度形分屑槽的寬度很窄,通常隻有1mm左右,要將砂輪外圓角修成60°~90°角,並要求在拉刀上磨出αf=5°的槽底後角,砂輪直徑不能選大,否則會碰到相鄰刀齒,加之砂輪在尖角處磨損快,需經常修整,這在工藝上是有難度的。所以操作者在制造拉刀時,常用薄片砂輪來磨削,致使磨出的窄分屑槽成瞭U形分屑槽。 由於圓弧形分屑槽的結構合理,其槽角比V形窄分屑槽的槽角大,且槽與切削刃相交處的刀尖角也大,磨削方便,砂輪與被磨工件(拉刀)接觸麵大,磨削時工件不易燒傷,所以為瞭提高拉刀使用壽命,拉刀不但在粗切齒和過渡齒上,而且在精切齒上磨的分屑槽也應盡量采用圓弧形分屑槽。 為使切屑能順利卷曲,分屑槽的槽數需適當增多。經驗表明,其槽數應使切下的切屑寬度以不超過4mm ~5mm為宜。目前一些拉刀設計資料中推薦的V形分屑槽的槽數普遍較少,例如直徑為Φ50mm的圓拉刀,分屑槽的槽數是22個,而國外同尺寸拉刀上的分屑槽數目為40個。同理,輪切式和組合式圓拉刀上的圓弧形分屑槽數目亦要適當增多。
![]() 圖4 拉削缺陷 |
拉孔表麵質量差的原因及改進圖4中所示的鱗刺、環狀波紋和劃痕等缺陷都會直接影響拉孔的表麵質量。 鱗刺 產生鱗刺的主要原因是拉削過程中塑性變形較嚴重。因此,適當增大前角,減小齒升量,選用潤滑性能好的切削液(如含氯的極壓添加劑切削液),以及用預先熱處理來適當提高工件材料硬度(當工件硬度<180HBS時最易產生鱗刺)等方法,都是減少塑性變形和避免鱗刺的有效措施。 環狀波紋 產生波紋的主要原因是拉削力變化較大,切削過程不平穩,產生瞭周期性振動。而引起拉削力變動的原因是:拉刀刀齒交替工作時,同時工作齒數發生變化;齒升量安排不合理,最後幾個精切齒上的齒升量變化太大;刀齒上的刃帶寬度太小或同一刀齒上的刃帶寬窄不等;以及拉刀齒距等距分佈等。找出具體原因後,可采取相應措施。例如,可采用不等齒距的拉刀,或在制造拉刀時齒距不規定公差;適當增加同時參加工作齒數,最好4個~5個,如果太少,可把幾個工件疊在一起拉削。 局部劃痕及“啃刀” 局部劃痕由以下原因造成:積屑瘤、刀齒上有缺口、或容屑條件差;切屑擦傷工件表麵;在拉刀的最後一個精切齒上未開分屑槽。“啃刀”是因拉刀彎曲,使刀齒發生突然移動或擺動造成的。使用較低的切削速度(<2m/min)來抑制積屑瘤的產生,防止切削刃刃麵上的制造缺陷和損傷,及時清除容屑槽中的積屑,重磨前刀麵時須保持原有容屑槽的形狀,拉刀使用完畢必須懸掛以免拉刀因自重而產生彎曲等都是防止劃痕及“啃刀”的有效措施。 擠壓亮點 擠壓亮點是由刀齒後刀麵與已加工表麵之間產生較強烈的擠壓摩擦,或因工件材料硬度過高而造成的。因此,可采取適當增大後角;減小校準齒上刃帶寬度(可減至0.2mm ~0.3mm);選用合適的切削液;應用熱處理方法降低工件材料硬度(當硬度>240HBS時);或把前角適當減小,以增加刃口強度,防止崩刃等均可有效減少工件表麵產生擠壓亮點與劃傷。 拉孔精度低的原因及改進 拉後孔徑擴大或縮小 由於積屑瘤的影響和磨刀時產生的毛刺,拉刀制造時產生的切削刃位置偏差和軸線直線度偏差,以及拉刀和工件預制孔不同心等原因,通常拉後孔徑將會擴大。但在拉削薄壁工件或軔性大的工件材料時,由於拉後工件會產生彈性回復而使孔徑縮小,確定拉刀校準齒尺寸時須考慮拉後孔徑的擴大量或收縮量,其值應通過試驗確定,一般在0.01mm ~0.02mm范圍內。 使用拉刀時,還可通過適當降低切削速度、采用冷卻性能好的切削液,防止積屑瘤的產生以免孔徑擴大。防止孔徑縮小,可采用增大前角、保持刃口鋒利、以及選用合適的切削液等方法。例如,用拉刀拉削40Cr和45鋼工件,當用乳化液孔徑尺寸變小時可改用硫化油拉削。這是因為乳化液是一種水基切削液,水的導熱性好,故刀具的熱膨脹小;乳化液的潤滑性比油類切削液差,所以刀具對工件的擠壓作用也大,加工後工件的回彈量也就增加,因而孔徑尺寸減小。利用上述規律,實際生產中就可通過改變切削液的種類和成份來控制實際加工的尺寸,以滿足拉孔精度和質量的要求。 拉後孔形產生偏差 當工件孔壁沿軸線方向上厚度在全長上不均勻時,拉後孔形將會發生變化。如工件兩端為薄壁,拉後工件孔呈“腰鼓形”;工件中間部分為薄壁,拉後工件孔呈“喇叭口”形。因此,當工件壁厚不均勻且厚薄相差太大時,不宜采用拉削。
![]() 圖5 容屑槽的有效麵積與切削層截麵積 |
拉刀壽命低的原因及改進 拉刀容屑空間不足 拉刀屬於封閉式切削的刀具,如容屑空間不夠,切屑將堵塞在容屑槽內,而使拉削力急增,導致刀齒損壞或拉刀折斷。為此,使用外購拉刀拉削時,應先核算拉刀的容屑系數K。如圖5所示,須使容屑槽的有效麵積大於切削層截麵積,即 K=(πh2/4)/(L0hD)>1h為容屑槽的深度;L0為拉削長度;hD為切削層厚度,組合式拉刀上hD=2fz,見圖1,式中f2為齒升量;K為容屑系數,它的大小與被加工材料和齒升量有關,通常可取K=2~3.5,加工鑄件和齒升量大時K取小值。 刀具幾何參數不當 拉刀前角選用不當,後角太小或刃帶過寬,精切齒上磨的分屑槽為U形槽,切削條件差,刀齒磨損快,嚴重時會使拉刀卡住在工件孔中,使拉刀折斷。拉刀前角通常可取5°~18°,拉塑性材料時可取大值,拉脆性材料時取小值。拉刀後角,切削齒上可取3°±30°,校準齒上可取1°±30°。刃帶寬度通常粗切齒和過渡齒上為<0.2mm,精切齒為0.3mm,校準齒為0.5mm~0.6mm。此外,在精切齒上應磨圓弧形分屑槽或角度形(V形)分屑槽。 齒升量不當 如刀齒上的齒升量過大或不均勻,或個別刀齒上的齒升量過大,使切削力過大或產生顫動,而使刀齒損壞或拉刀折斷。為此,須控制拉刀每個刀齒上的齒升量,當個別刀齒上有損傷、缺口或崩刃時,應將該刀齒磨去,再把其齒升量均勻分攤到其他各個刀齒上。 拉刀刃磨退火 重磨拉刀時不能進刀太快,吃刀過大,以免產生刃口處過熱退火和燒傷等現象,而使刀齒磨損加快和拉刀壽命降低。所以,重磨拉刀時必須精細操作。 工件預制孔尺寸不當及拉削長度過長 工件預制孔直徑偏小,當拉刀前導部強行通過時,容易使拉刀卡住而折斷;或當工件預制孔直徑過大,造成孔的偏移而使拉刀折斷。為此,拉削時必須選用合適的預制孔尺寸,一般拉刀前導部直徑尺寸等於工件預制孔的基本尺寸,公差帶按f7。此外,被拉工件的拉削長度也不能超出拉刀設計時規定的長度,以免同時參加工作齒數增多,切削力過大而使刀齒損壞或拉刀折斷。一般拉削長度都列印在拉刀的頸部上。 工件定位不良 如工件基準端麵與預制孔的垂直度差,夾具支承麵處有切屑,拉刀產生下垂,拉削時拉刀相對工件歪斜等,都會使刀齒上負荷不均勻,造成很大彎曲而使拉刀折斷。為此,須控制預制孔中心線與工件基準端麵的垂直度為0.02~0.05mm/100mm;定位基準端麵應盡可能大,不應有中凸,表麵粗糙度Ra<3.2μm;或采用浮動支承的拉床夾具;對長而重的拉刀,還可使用後托架支承拉刀。
![]() 圖6 拉刀尾端裝硬質合金擠壓環 |
工件材質不均勻與硬度過高 工件材質不均勻,其內有硬質點或材料硬度過高(>280HBS時),表麵有氧化皮等都會使刀具壽命降低。所以,拉前須檢驗工件材質,如材料硬度過高可采用熱處理方法適當降低;或選用W2Mo9Cr4VCo8(M42)、W6Mo5Cr4V2Al等硬度和耐磨性能均較高的高性能高速工具鋼來制造拉刀,國外還有用粉末冶金高速鋼(PM HSS)制造的拉刀;也可在拉刀刀齒表麵上塗一薄層耐磨的TiN;或在拉刀尾端裝一可更換的硬質合金擠壓環,如圖6所示。 拉刀磨損過度 為防止拉刀磨損過度,以免切削力過大而使刀齒損壞,故須控制拉刀刀齒後刀麵上的磨損量,通常不應超過0.2mm~0.3mm,工廠中常以達到上述磨損量時所拉出的工件數來加以控制。 拉床功率不足,剛性差 拉床功率不足,剛性差,引起拉削時振動而使刀齒崩刃或折斷,可改用剛性好和功率足的拉床拉削。 拉削速度不當 如拉削速度過高,切削溫度高,則拉刀壽命將會降低。因而,對於用W6Mo5Cr4V2等通用型高速鋼制造的拉刀,粗拉切削速度一般為3~7m/min, 精拉切削速度一般為1~3m/min;工件材料強度、硬度較高時,拉削速度應取小值。 切削液種類或澆註方式不當 切削液種類與澆註方式不但影響拉刀壽命,而且對加工精度和表麵粗糙度均有影響。加工鋼件孔時,可用濃度為10%~20%乳化液或極壓乳化液,也可用硫化油或復合油。拉鑄件孔時可以乾切削,但最好用普通乳化液或煤油。加工鋼件時如用硫化油,可使拉刀壽命提高。切削液供應要充足,在拉刀進入工件孔前和剛從工件孔中拉出時都應供給切削液,供應量一般不應少於5~15L/min。 此外,正確使用和保管拉刀對拉刀壽命也有影響。在每一個工件拉削之後,都應用銅絲刷將粘附在刃麵上的切屑清除乾凈。如用銅絲刷清除不掉時,可用油石輕輕擦去。但絕不可用鋼絲刷或棉紗。同時拉刀在制造、運輸和保管與使用過程中,不可碰傷刀齒和刃口。拉刀的修復拉刀的價格很貴,為瞭延長其壽命,所以拉刀經多次重磨之後,直徑變小將要報廢時常加以修復使用。這時可在車床上用帶負前角的硬質合金工具逐齒擠壓刀齒前刀麵。擠壓後直經可增大0.01mm~0.02mm,然後再研磨,使其達到規定尺寸。
溫嶺市三川工具廠是一傢專業從事拉刀研發、生產、銷售為一體的廠傢,品種有圓拉刀,漸開線拉刀,花鍵拉刀,鍵槽拉刀,螺旋拉刀,小徑定心拉刀,特異成形拉刀等。
我廠自成立以來,本著“以質量求生存,以信譽求發展”為理念,不斷引進新技術,新設備,現有數控高精度設備、檢測機器十多臺套,能生產高精度漸開線拉刀、小徑定心復合齒形漸開線花鍵拉刀、超長螺旋拉刀等各種復雜特形拉刀,並已全麵導入計
算機網絡系統,在產品開發設計、生產制造中,普遍采用CAD計算機輔助設計,CAM計算機輔助制造和自主編寫的拉刀設計專用程序等現代設計手段。 隆盛工具憑借一支敬業的隊伍,先進的設備,嚴格的管理,優異的性價比,贏得瞭廣大客戶的好評。隆盛人將繼續發揚“專業、創新、優質、高效”的辦廠宗旨,與廣大新老客戶攜手發展。
圓拉刀是高效加工內孔常用的刀具。本文以筆者在工廠中長期的使用經驗與驗證為依據,對圓拉刀結構上存在的問題提出瞭改進意見,同時還對拉孔表麵質量差、拉孔精度低和拉刀壽命低的原因進行瞭詳細分析並逐一列出改進措施。
![]() 圖1 組合式圓拉刀刀齒和切削圖形 |
![]() 圖2 校準齒上磨分屑槽 |
![]() 圖3 常用分屑槽的形狀 |
圓拉刀是高效加工內孔常用的刀具。圓拉刀系刃形復雜刀具,制造精度高,技術要求嚴格,價格昂貴,應合理使用。目前生產上廣泛使用的圓拉刀(以下簡稱拉刀), 大多采用圖1所示組合式的刀齒結構,即在粗切齒和過渡齒上采用不分齒組的輪切式切削方式,其上開有寬的弧形分屑槽;精切齒采用同廓式的切削方式,其上磨出窄分屑槽。經作者在工廠中長期使用與驗證,發現這種拉刀由於結構本身或使用不當等原因,常會造成拉削表麵質量差和刀具使用壽命短等問題。拉刀結構問題及改進為瞭延長拉刀使用壽命,普通拉刀的結構是,在其校準部分上備有3個~7個校準齒,以便在切削齒磨損後逐個遞補為精切齒用。並且,人們通常認為校準齒是不參與切削工作的,故校準齒一般都不磨分屑槽(見圖1)。但在實際生產中,經觀察,拉刀上第一個校準齒是參與切削工作的(因為刃口上有鈍圓,會對孔壁產生較大擠壓作用而使工件產生彈性回復而縮小),它具有精切齒的功能。但因其上不作分屑槽,致使切下的切屑形成環狀,難於卷起,容易堵塞在槽內,使加工表麵質量降低。所以作者建議,在設計和制造拉刀時,除最後1個~2個校準齒外,如圖2所示,在其馀校準齒上亦應前後交錯地磨出圓弧形分屑槽或角度形(V形)窄分屑槽。如圖3所示,分屑槽上兩側刃的後角可按下式計算:
tanαk=tanαf·sin(θ/2)
αf為分屑槽的槽底後角,一般取為5°,見圖3中A-A剖麵;θ分屑槽的槽角。 由上式中可知,當θ=0°時,不論αf磨成多大,αf始終等於0°(即圖3c中所示U形分屑槽的情況)。而當θ角增大時,αf角也將增大。如取αf=5°,θ=60°~90°,則從公式中計算可知,此時側刃上的後角將增大到2.5°~3.5°,從而可使該處切削條件大大改善。 在實際生產中,由於角度形分屑槽的寬度很窄,通常隻有1mm左右,要將砂輪外圓角修成60°~90°角,並要求在拉刀上磨出αf=5°的槽底後角,砂輪直徑不能選大,否則會碰到相鄰刀齒,加之砂輪在尖角處磨損快,需經常修整,這在工藝上是有難度的。所以操作者在制造拉刀時,常用薄片砂輪來磨削,致使磨出的窄分屑槽成瞭U形分屑槽。 由於圓弧形分屑槽的結構合理,其槽角比V形窄分屑槽的槽角大,且槽與切削刃相交處的刀尖角也大,磨削方便,砂輪與被磨工件(拉刀)接觸麵大,磨削時工件不易燒傷,所以為瞭提高拉刀使用壽命,拉刀不但在粗切齒和過渡齒上,而且在精切齒上磨的分屑槽也應盡量采用圓弧形分屑槽。 為使切屑能順利卷曲,分屑槽的槽數需適當增多。經驗表明,其槽數應使切下的切屑寬度以不超過4mm ~5mm為宜。目前一些拉刀設計資料中推薦的V形分屑槽的槽數普遍較少,例如直徑為Φ50mm的圓拉刀,分屑槽的槽數是22個,而國外同尺寸拉刀上的分屑槽數目為40個。同理,輪切式和組合式圓拉刀上的圓弧形分屑槽數目亦要適當增多。
![]() 圖4 拉削缺陷 |
拉孔表麵質量差的原因及改進圖4中所示的鱗刺、環狀波紋和劃痕等缺陷都會直接影響拉孔的表麵質量。 鱗刺 產生鱗刺的主要原因是拉削過程中塑性變形較嚴重。因此,適當增大前角,減小齒升量,選用潤滑性能好的切削液(如含氯的極壓添加劑切削液),以及用預先熱處理來適當提高工件材料硬度(當工件硬度<180HBS時最易產生鱗刺)等方法,都是減少塑性變形和避免鱗刺的有效措施。 環狀波紋 產生波紋的主要原因是拉削力變化較大,切削過程不平穩,產生瞭周期性振動。而引起拉削力變動的原因是:拉刀刀齒交替工作時,同時工作齒數發生變化;齒升量安排不合理,最後幾個精切齒上的齒升量變化太大;刀齒上的刃帶寬度太小或同一刀齒上的刃帶寬窄不等;以及拉刀齒距等距分佈等。找出具體原因後,可采取相應措施。例如,可采用不等齒距的拉刀,或在制造拉刀時齒距不規定公差;適當增加同時參加工作齒數,最好4個~5個,如果太少,可把幾個工件疊在一起拉削。 局部劃痕及“啃刀” 局部劃痕由以下原因造成:積屑瘤、刀齒上有缺口、或容屑條件差;切屑擦傷工件表麵;在拉刀的最後一個精切齒上未開分屑槽。“啃刀”是因拉刀彎曲,使刀齒發生突然移動或擺動造成的。使用較低的切削速度(<2m/min)來抑制積屑瘤的產生,防止切削刃刃麵上的制造缺陷和損傷,及時清除容屑槽中的積屑,重磨前刀麵時須保持原有容屑槽的形狀,拉刀使用完畢必須懸掛以免拉刀因自重而產生彎曲等都是防止劃痕及“啃刀”的有效措施。 擠壓亮點 擠壓亮點是由刀齒後刀麵與已加工表麵之間產生較強烈的擠壓摩擦,或因工件材料硬度過高而造成的。因此,可采取適當增大後角;減小校準齒上刃帶寬度(可減至0.2mm ~0.3mm);選用合適的切削液;應用熱處理方法降低工件材料硬度(當硬度>240HBS時);或把前角適當減小,以增加刃口強度,防止崩刃等均可有效減少工件表麵產生擠壓亮點與劃傷。 拉孔精度低的原因及改進 拉後孔徑擴大或縮小 由於積屑瘤的影響和磨刀時產生的毛刺,拉刀制造時產生的切削刃位置偏差和軸線直線度偏差,以及拉刀和工件預制孔不同心等原因,通常拉後孔徑將會擴大。但在拉削薄壁工件或軔性大的工件材料時,由於拉後工件會產生彈性回復而使孔徑縮小,確定拉刀校準齒尺寸時須考慮拉後孔徑的擴大量或收縮量,其值應通過試驗確定,一般在0.01mm ~0.02mm范圍內。 使用拉刀時,還可通過適當降低切削速度、采用冷卻性能好的切削液,防止積屑瘤的產生以免孔徑擴大。防止孔徑縮小,可采用增大前角、保持刃口鋒利、以及選用合適的切削液等方法。例如,用拉刀拉削40Cr和45鋼工件,當用乳化液孔徑尺寸變小時可改用硫化油拉削。這是因為乳化液是一種水基切削液,水的導熱性好,故刀具的熱膨脹小;乳化液的潤滑性比油類切削液差,所以刀具對工件的擠壓作用也大,加工後工件的回彈量也就增加,因而孔徑尺寸減小。利用上述規律,實際生產中就可通過改變切削液的種類和成份來控制實際加工的尺寸,以滿足拉孔精度和質量的要求。 拉後孔形產生偏差 當工件孔壁沿軸線方向上厚度在全長上不均勻時,拉後孔形將會發生變化。如工件兩端為薄壁,拉後工件孔呈“腰鼓形”;工件中間部分為薄壁,拉後工件孔呈“喇叭口”形。因此,當工件壁厚不均勻且厚薄相差太大時,不宜采用拉削。
![]() 圖5 容屑槽的有效麵積與切削層截麵積 |
拉刀壽命低的原因及改進 拉刀容屑空間不足 拉刀屬於封閉式切削的刀具,如容屑空間不夠,切屑將堵塞在容屑槽內,而使拉削力急增,導致刀齒損壞或拉刀折斷。為此,使用外購拉刀拉削時,應先核算拉刀的容屑系數K。如圖5所示,須使容屑槽的有效麵積大於切削層截麵積,即 K=(πh2/4)/(L0hD)>1h為容屑槽的深度;L0為拉削長度;hD為切削層厚度,組合式拉刀上hD=2fz,見圖1,式中f2為齒升量;K為容屑系數,它的大小與被加工材料和齒升量有關,通常可取K=2~3.5,加工鑄件和齒升量大時K取小值。 刀具幾何參數不當 拉刀前角選用不當,後角太小或刃帶過寬,精切齒上磨的分屑槽為U形槽,切削條件差,刀齒磨損快,嚴重時會使拉刀卡住在工件孔中,使拉刀折斷。拉刀前角通常可取5°~18°,拉塑性材料時可取大值,拉脆性材料時取小值。拉刀後角,切削齒上可取3°±30°,校準齒上可取1°±30°。刃帶寬度通常粗切齒和過渡齒上為<0.2mm,精切齒為0.3mm,校準齒為0.5mm~0.6mm。此外,在精切齒上應磨圓弧形分屑槽或角度形(V形)分屑槽。 齒升量不當 如刀齒上的齒升量過大或不均勻,或個別刀齒上的齒升量過大,使切削力過大或產生顫動,而使刀齒損壞或拉刀折斷。為此,須控制拉刀每個刀齒上的齒升量,當個別刀齒上有損傷、缺口或崩刃時,應將該刀齒磨去,再把其齒升量均勻分攤到其他各個刀齒上。 拉刀刃磨退火 重磨拉刀時不能進刀太快,吃刀過大,以免產生刃口處過熱退火和燒傷等現象,而使刀齒磨損加快和拉刀壽命降低。所以,重磨拉刀時必須精細操作。 工件預制孔尺寸不當及拉削長度過長 工件預制孔直徑偏小,當拉刀前導部強行通過時,容易使拉刀卡住而折斷;或當工件預制孔直徑過大,造成孔的偏移而使拉刀折斷。為此,拉削時必須選用合適的預制孔尺寸,一般拉刀前導部直徑尺寸等於工件預制孔的基本尺寸,公差帶按f7。此外,被拉工件的拉削長度也不能超出拉刀設計時規定的長度,以免同時參加工作齒數增多,切削力過大而使刀齒損壞或拉刀折斷。一般拉削長度都列印在拉刀的頸部上。 工件定位不良 如工件基準端麵與預制孔的垂直度差,夾具支承麵處有切屑,拉刀產生下垂,拉削時拉刀相對工件歪斜等,都會使刀齒上負荷不均勻,造成很大彎曲而使拉刀折斷。為此,須控制預制孔中心線與工件基準端麵的垂直度為0.02~0.05mm/100mm;定位基準端麵應盡可能大,不應有中凸,表麵粗糙度Ra<3.2μm;或采用浮動支承的拉床夾具;對長而重的拉刀,還可使用後托架支承拉刀。
![]() 圖6 拉刀尾端裝硬質合金擠壓環 |
工件材質不均勻與硬度過高 工件材質不均勻,其內有硬質點或材料硬度過高(>280HBS時),表麵有氧化皮等都會使刀具壽命降低。所以,拉前須檢驗工件材質,如材料硬度過高可采用熱處理方法適當降低;或選用W2Mo9Cr4VCo8(M42)、W6Mo5Cr4V2Al等硬度和耐磨性能均較高的高性能高速工具鋼來制造拉刀,國外還有用粉末冶金高速鋼(PM HSS)制造的拉刀;也可在拉刀刀齒表麵上塗一薄層耐磨的TiN;或在拉刀尾端裝一可更換的硬質合金擠壓環,如圖6所示。 拉刀磨損過度 為防止拉刀磨損過度,以免切削力過大而使刀齒損壞,故須控制拉刀刀齒後刀麵上的磨損量,通常不應超過0.2mm~0.3mm,工廠中常以達到上述磨損量時所拉出的工件數來加以控制。 拉床功率不足,剛性差 拉床功率不足,剛性差,引起拉削時振動而使刀齒崩刃或折斷,可改用剛性好和功率足的拉床拉削。 拉削速度不當 如拉削速度過高,切削溫度高,則拉刀壽命將會降低。因而,對於用W6Mo5Cr4V2等通用型高速鋼制造的拉刀,粗拉切削速度一般為3~7m/min, 精拉切削速度一般為1~3m/min;工件材料強度、硬度較高時,拉削速度應取小值。 切削液種類或澆註方式不當 切削液種類與澆註方式不但影響拉刀壽命,而且對加工精度和表麵粗糙度均有影響。加工鋼件孔時,可用濃度為10%~20%乳化液或極壓乳化液,也可用硫化油或復合油。拉鑄件孔時可以乾切削,但最好用普通乳化液或煤油。加工鋼件時如用硫化油,可使拉刀壽命提高。切削液供應要充足,在拉刀進入工件孔前和剛從工件孔中拉出時都應供給切削液,供應量一般不應少於5~15L/min。 此外,正確使用和保管拉刀對拉刀壽命也有影響。在每一個工件拉削之後,都應用銅絲刷將粘附在刃麵上的切屑清除乾凈。如用銅絲刷清除不掉時,可用油石輕輕擦去。但絕不可用鋼絲刷或棉紗。同時拉刀在制造、運輸和保管與使用過程中,不可碰傷刀齒和刃口。拉刀的修復拉刀的價格很貴,為瞭延長其壽命,所以拉刀經多次重磨之後,直徑變小將要報廢時常加以修復使用。這時可在車床上用帶負前角的硬質合金工具逐齒擠壓刀齒前刀麵。擠壓後直經可增大0.01mm~0.02mm,然後再研磨,使其達到規定尺寸。

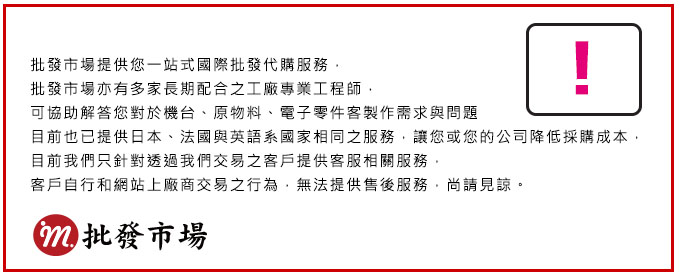
批發市場僅提供代購諮詢服務,商品內容為廠商自行維護,若有發現不實、不合適或不正確內容,再請告知我們,查實即會請廠商修改或立即下架,謝謝。